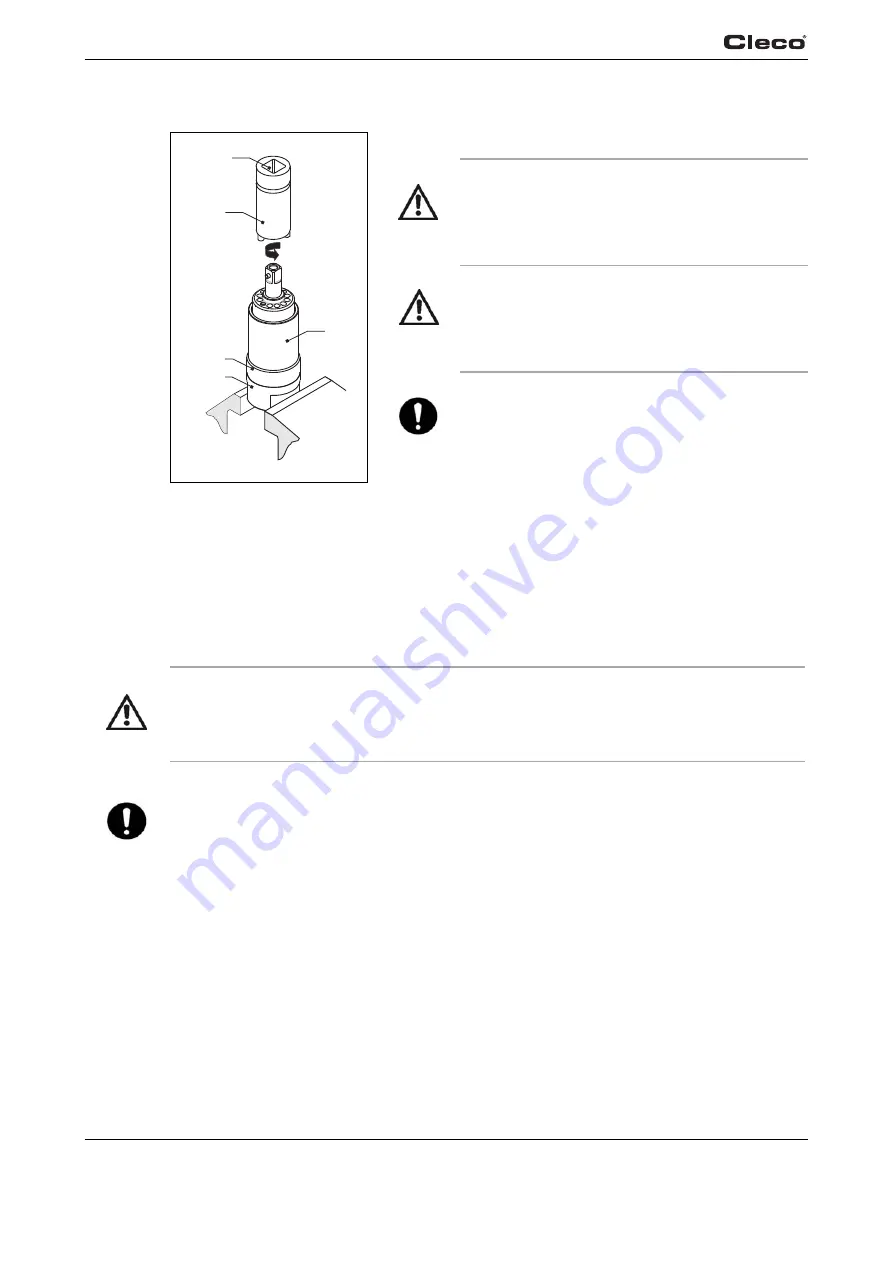
24
P2120BA/EN 2014-06
2123d_Reparatur_en_bedingt.fm, 03.07.2014
Assembly instructions
8
7.3
Remove pulse unit
Abb. 7-1
8
Assembly instructions
<…>
Please refer to 9 Spare parts, page 29 und 9.5 Equipment order list, page 38
8.1
Install motor unit
CAUTION!
Skin irritation in case of direct contact with oil.
Wear protective gloves.
CAUTION!
Hydraulic blade is under spring pressure!
Wear protective goggles.
NOTE
Permitted only if filling is guaranteed with oil filling device,
see 6.2 Fill reserve oil, page 16. Pulse unit must have
cooled down to room temperature.
CAUTION!
•
Only perform installation in accordance with exploded drawing, see 9 Spare parts, page 29.
Incorrect installation can lead to uncontrolled reactions, e.g. unexpected start-up or parts being hurled
out.
•
Tighten all screwed joints of the tool carefully, according to the specifications.
NOTE
To prevent damage, lubricate the gaskets and O-rings using grease (order no. 914392) before assembly.
WAF 1/2"
<D3>
<D2>
<D1>
<84>