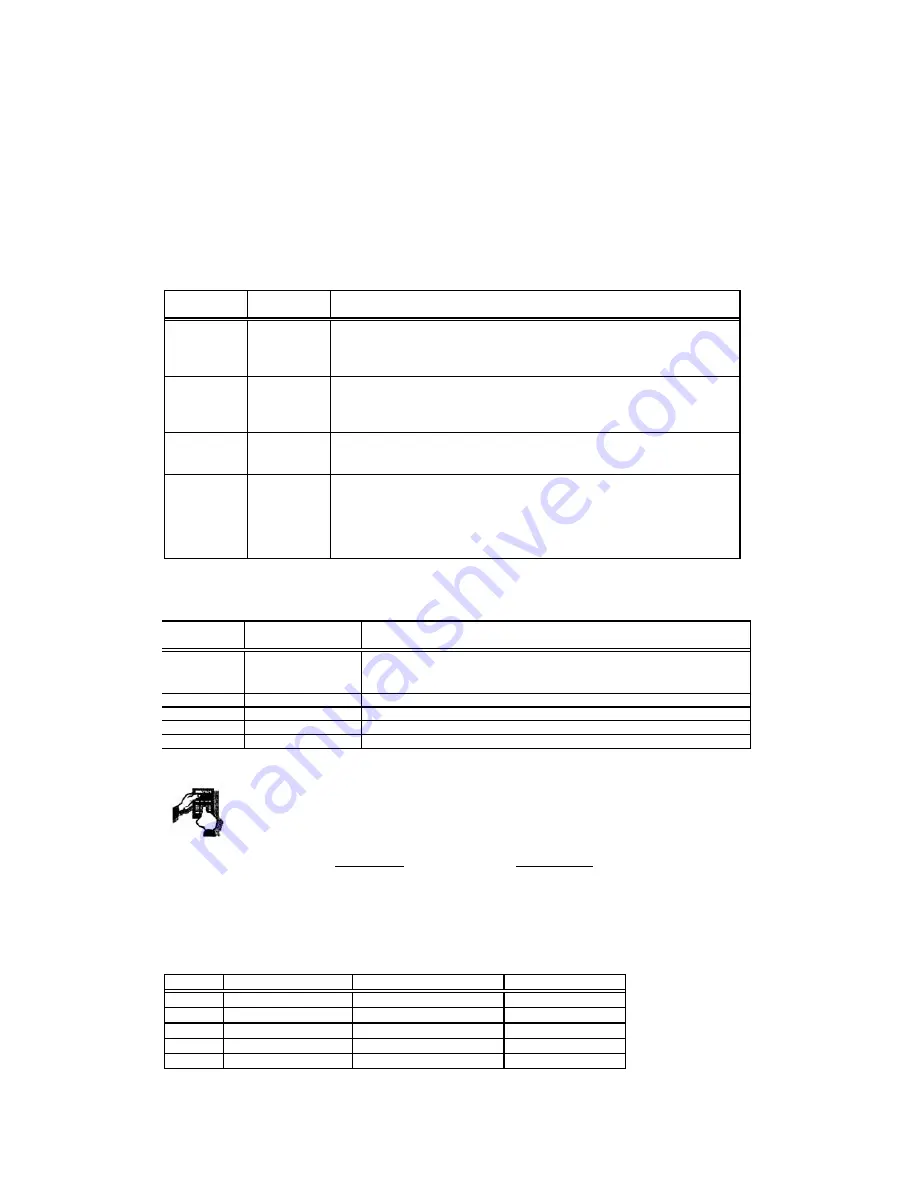
Page 12
PL12-1014EN
10/16/2014
Cleco
®
General Information
8.1
Service schedule
Only qualified and trained personnel are permitted to perform maintenance on these tools.
Regular maintenance reduces operating faults, repair costs and downtime. In addition to the following
service schedule, implement a safetu related maintenance program that takes the local regulations for
repair and maintenance for all operating phases of the tool into account.
This maintenance schedule uses values that are valid for most applications. For a specific maintenance
interval, refer to 8.1.1 Calculating a customer-specific maintenance plan.
8.1.1
Calculating a customer specific maintenance plan
A service interval W(1, 2, 3) depends on the following factors:
8.2
Lubricants
For proper function and long service life, use of the correct grease is essential.
Maintenance
Interval
Rundowns
Daily
Daily
Ú
Ú
Ú
Ú
Visual inspection of air supply hose and connections
Inspect airline filter, regulator and lubricator for proper operation
Check the tool excessive vibration or unusual noises
Visual inspection of all external components of the tool
W1
100,000
Ú
Ú
Ú
Ú
Inspect the air hose for damage or wear
inspect the square drive output spindle for damage or wear
Inspect the air inlet adapter for a secure fit
Check the maximum free speed
W2
500,000
Ú
Ú
Ú
Check individual parts and replace if necessary
Replace O-rings and seals
Clean bronze mufflers
W3
1,000,000
Ú
Ú
Ú
Ú
Ú
Ú
Check individual parts and replace if necessary
Throttle valve
Motor
Gearing
Clutch (19RAA)
Angle attachment
Designation
Part No.
Packaged
Designation
Vendor
540450
18 oz. (0.51 kg)
Black Pearl EP-NLGI-0
Chevron
540395
2 oz. (0.06 kg)
Magnalube-G
Carleton-Stuart Corp.
513156
16 oz. (0.45 kg)
Magnalube-G
Carleton-Stuart Corp.
541444
2 oz. (0.06 kg)
Rheolube 363AX-1
Nye Lubricants, Inc.
541445
16 oz. (0.45 kg)
Rheolube 363AX-1
Nye Lubricants, Inc.
Example for service interval W2:
After 500,000 rundowns (V),
a specific rundown time of 1.8 seconds (T1)
with an actual fastening time of 3 seconds (soft joint) and
3 completed shifts per day and 750 rundowns per shift.
V x T1
500000 x 1.8
T2 x S x VS
3 x 3 x 750
You will need to perform the maintenance indicated as W2 after an operating time of 133 days.)
W (1, 2, 3) =
W2 =
= 133 (days)
Factor
Value assumed in
"Service Schedule"
Description
V
V1 = 100,000
V2 - 500,000
V3 = 1,000,000
Number of rundowns after a maintenance measure is prescribed by Apex
Tool Group.
T1
1.8 seconds
Specific rundown time, measured in life and endurance tests.
T2
2 seconds
Actual rundown time, depending on the hardness of the joint.
S
1; 2; 3
Number of shifts per day.
VS
750
Number of rundowns per shift.
T2, S and VS are variable factors and can differ depending on the specific application.