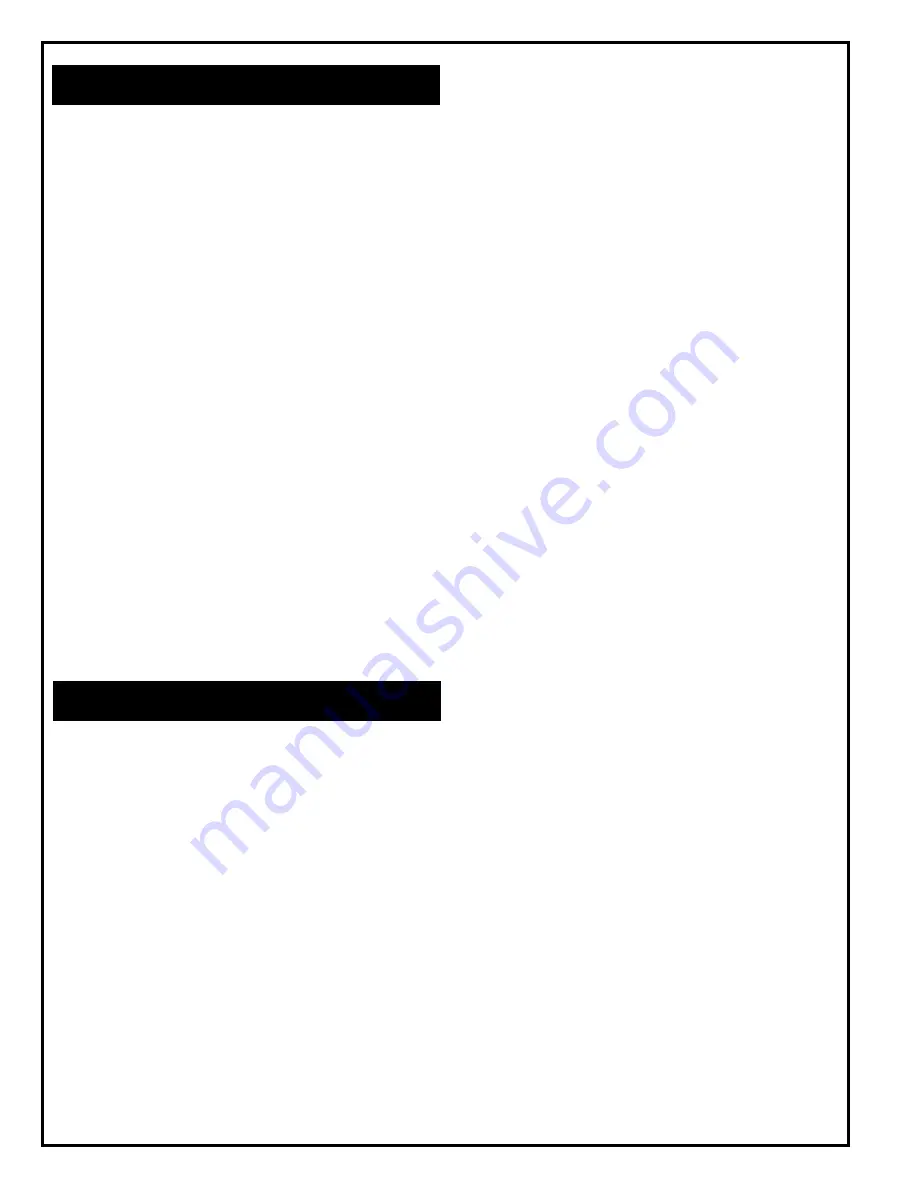
4
OPERATING INSTRUCTIONS
The 75MTC Nutrunner is designed to operate on 90 PSIG (6.2 bar)
air pressure using a 1/2" hose up to 8 ft. in length.
AIR SUPPLY
For maximum performance, use a 1/2" I.D. air hose no longer than
8' in length. If additional length is required, a 3/4" or larger hose
should be connected to the 1/2" hose. The air hose should be
cleared of accumulated dirt and moisture, then one (1) teaspoonful
of 10W machine oil should be pou- red into the tool's air inlet before
connecting the hose to the tool.
LUBRICATION
An automatic in-line filter-lubricator is recommended as it increases
tool life and keeps the tool in sustained operation. The in-line
lubricator should be regularly checked and filled with a good grade
of 10W machine oil. Proper adjustment of the in-line lubricator is
performed by placing a sheet of paper next to the exhaust ports and
holding the throttle open for approximately 30 seconds. The lubri-
cator is properly set when a very light stain of oil collects on the
paper. Excessive amounts of oil should be avoided.
Application of the tool should govern how frequently it is greased.
It is recommended that the idler gears and right angle gears receive
a generous amount of NLGI 2-EP grease at every repair cycle.
STORAGE
In the event that it becomes necessary to store the tool for an
extended period or time (overnight, weekend, etc.), it should receive
a generous amount of lubrication at that time and again when
returned to service. The tool should be stored in a clean and dry
environment.
SERVICE INSTRUCTIONS
DISASSEMBLY—GENERAL
Clamp the flats of the motor housing in a vise with the tool in a
vertical position. Using a suitable wrench, unscrew and remove the
clutch and gear case assemblies. Slip the motor unit out the front of
the handle. It may be necessary to bump the handle on the work
bench to loosen the motor.
SUBASSEMBLY DISASSEMBLY
Gear Case
Slip the entire gear train out the rear of the gear case. The 2nd
reduction idler gears may be removed for inspection by driving the
idler gear pins, No. 869908, out the rear of the spider.
Motor
Use a soft faced mallet to drive the rotor out of the front rotor bearing.
This will allow the removal of the front bearing plate, cylinder, and
five (5) rotor blades, from the rotor. Clamp the rotor lightly in the vise
and unscrew the rotor lock nut. Rest the rear bearing plate on the
vise jaws and use a soft faced mallet to drive the rotor out of the rear
rotor bearing.
Handle
Unscrew the inlet bushing for inspection of the throttle compo-
nents. The air inlet screen should be washed in a solvent and
blown out in the reverse of normal airflow. Replace if damaged or
clogged.
REASSEMBLY
The tool is reassembled in the reverse order of disassembly.
Clean all parts thoroughly in a solvent and inspect for damage or
wear. Check all bearings for wear which can be detected by
excessive end play and/or roughness which would indicate a
brinelled condition. The rotor blades should be replaced at every
repair cycle or if they measure less than 3/8" (9.5mm) at either
end. All gear teeth, bearings, and pins should receive a close
inspection and be replace if necessary. All gears and open
bearings should receive a generous amount of NLGI 2-EP grease
during reassembly.
Motor
To assemble the motor, install the rear rotor bearing into the rear
bearing plate. Make sure the outer bearing race is firmly seated in
the bearing plate. Clamp the rotor body lightly in the vise with the
threaded end up and slip the rear bearing plate assembly onto the
rotor shaft far enough for the bearing lock nut to start. Tighten the
lock nut until there is approximately .0015" clearance between the
rotor and bearing plate. The outer bearing race should be firmly
seated and the rotor bumped forward when checking this clear-
ance. Pack both rotor bearings with a good grade of NLGI 2-EP
grease after assembly of the motor unit.
IMPORTANT: During reassembly of the complete tool, it is
important that the motor be free. After the tool is completely
assembled, the square drive spindle should turn freely using a
small hand wrench. If the spindle does not turn freely, the motor
should be checked for proper spacing. Do not run the tool until the
spindle turns freely. Failure to do this could result in damage to
motor components.
1st REDUCTION GEAR TRAIN REASSEMBLY
-2 Gear Train (13 Tooth Spider)
21 Tooth idler gears on inner set of gear pins.
-3 Gear Train (19 Tooth Spider)
21 Tooth idler gears on inner set of gear pins.
-4 Gear Train (13 Tooth Spider)
17 Tooth idler gears on outer set of gear pins using 16 tooth pinion
on rotor.
-5 Gear Train (19 Tooth Spider)
17 Tooth idler gears on outer set of gear pins using 16 tooth pinion
on rotor.
Summary of Contents for 75MTC Series
Page 14: ...14 NOTES ...
Page 15: ...15 NOTES ...
Page 16: ...16 670 Industrial Drive Lexington SC 29072 Phone 803 359 1200 Fax 803 359 2013 ...