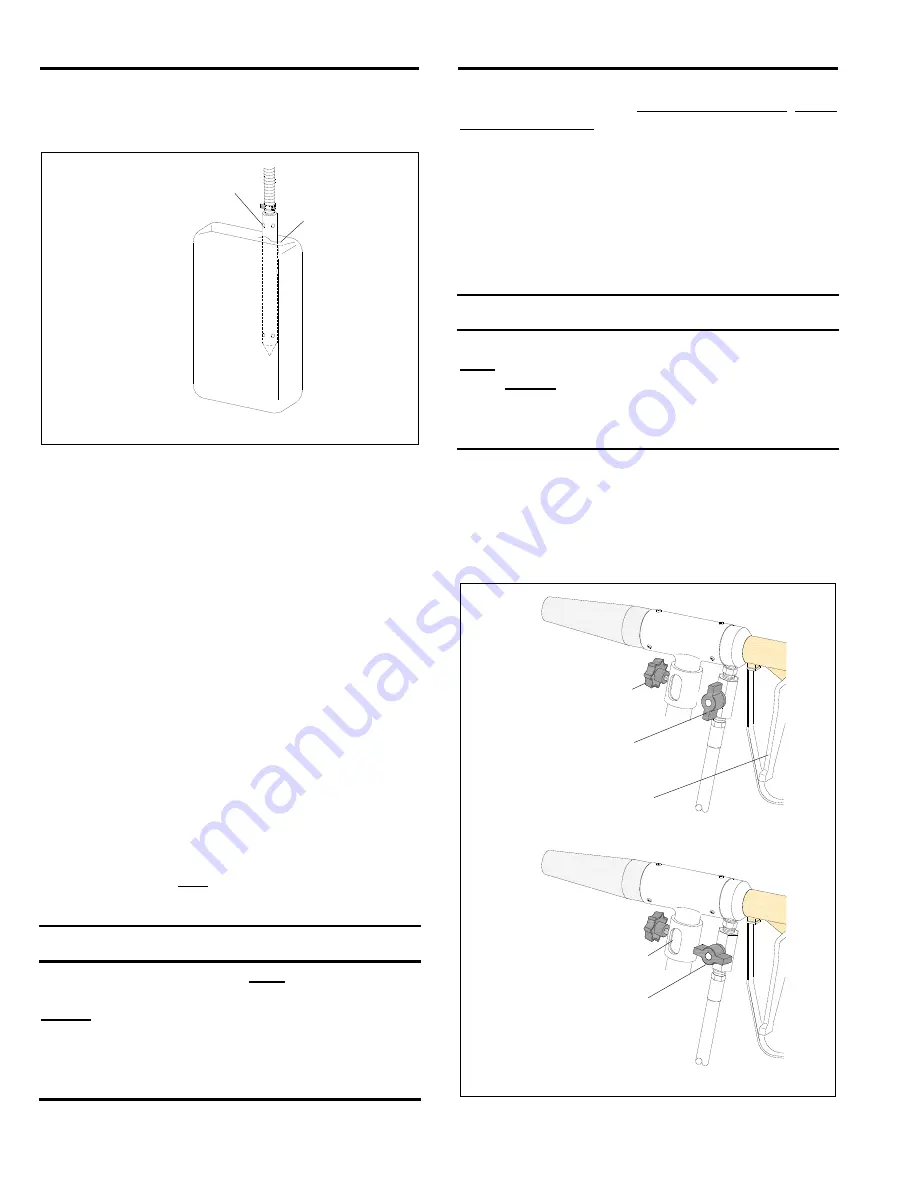
POWER GUN SUCTION BLAST TOOLS
Page 6
© 2018 CLEMCO INDUSTRIES CORP.
www.clemcoindustries.com
Manual No. 24189, Rev. C 06/18
abrasive. Using bagged abrasive requires repositioning
of the lance as the abrasive level drops.
SILICA
FREE
ABRASIVE
Figure
7
4.5 Dry
Blasting
4.5.1
Don appropriate protective gear, including a
NIOSH-approved supplied-air respirator, abrasive
resistant clothing, leather gloves, and hearing protection
as required. Refer to Section 4.2.
4.5.2
Hold the gun approximately 6 inches from the
blast surface and squeeze the trigger. Adjust the stand-
off distance and angle for optimum performance.
4.5.3
Adjust blast pressure per Section 5.1.
4.5.4
To stop blasting release the trigger.
4.6
Wetblasting, H2O Model Only
‒
Figure 8
4.6.1
Set up water connections per Section 3.2.
4.6.2
Close air-induction valve and begin dry blasting,
and set blast pressure per Section 4.5.
4.6.3
A moment after pulling the trigger, open the
water valve and adjust water flow per Section 5.3.
NOTICE
Open the water valve only after pulling the
trigger to begin blasting and always close it
before releasing the trigger to stop blasting.
Failure to have the water valve closed when the
trigger is released can allow water to flow into
the mixing chamber and material hose, causing
blockage from wet abrasive.
4.6.4
To stop blasting, close the water valve before
releasing the trigger. By not closing the water valve first
will allow water to flow into the mixing chamber and
material hose, causing blockage.
4.6.5 Wash
Down:
While blasting, loosen the air-
induction tensioning knob and rotate the sleeve to fully
open the induction port. This step stops abrasive flow
while air and water continue to flow through the nozzle
as long as the trigger is pulled.
NOTICE
Whenever using water, open the water valve
after pulling the trigger and close the water
valve before releasing the trigger. By having the
valve open when the trigger is not pulled can
allow water to flow into the mixing chamber and
material hose, causing blockage
4.6.6 Air Drying and Blow-off:
After wash-down,
close the water valve and continue to hold the trigger.
Doing so will have air alone coming from the gun to
speed up the drying process. This process can also be
used to blow-off the blasted surface after dry blasting.
Figure
8
Air-Intake Holes
Lance
Some items rotated for clarity.
Trigger
Tensioning Knob
Water Valve
Handle shown fully open
.
Water Valve
Handle shown fully Closed
Air Induction Valve
Shown Open.