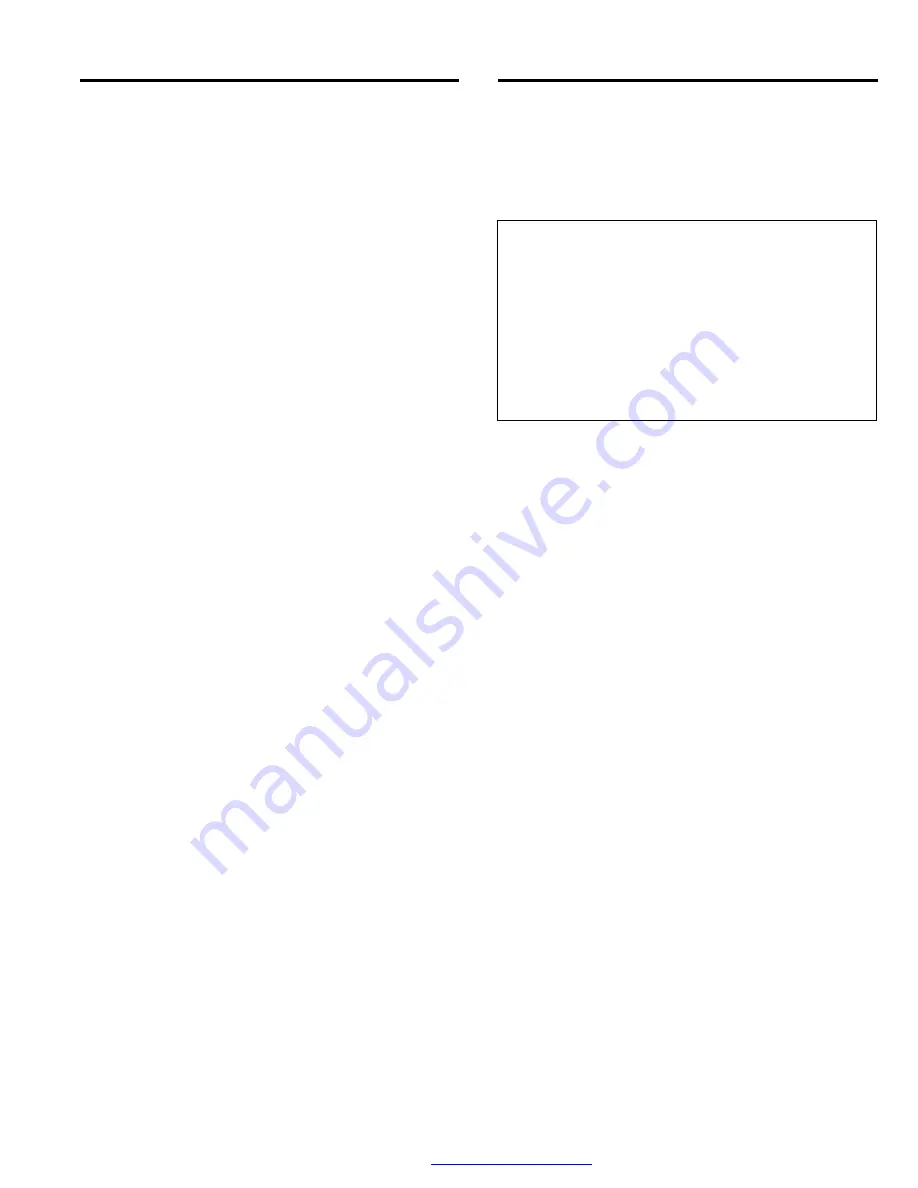
MEDIA RECLAIMER / SEPARATOR
Page 9
© 2005 CLEMCO INDUSTRIES CORP.
•
www.clemcoindustries.com
•
Manual No. 23438
•
Rev. E
static pressure has been adjusted, adjust the cylinder as
follows.
5.2.1
The adjusting lever for the vortex cylinder is
mounted on the outlet pipe on top of the reclaimer or the
spacer between the reclaimer body and exhauster
housing depending upon which system is provided.
5.2.2
Adjustments are made by loosing the handle's
locking knob and moving the handle to achieve the
correct setting. When the correct setting is established,
tighten the locking knob to prevent movement.
5.2.3
Start with the lever slightly to the right (about
one o’clock) of the vertical position.
5.2.4 Dusty
Media:
To increase media consumption,
raise the cylinder by moving the lever left toward
"COARSE", in 1/4" increments at the indicator plate. Do
not adjust again until the media has gone through
several cycles, to be certain that further adjustment is
required.
5.2.5 Media Carryover:
To decrease media
consumption (excessive usable media is being carried to
the dust collector), lower the vortex cylinder by moving
the lever right toward "FINE", in 1/4" increments at the
indicator plate. Note: If the cylinder is lowered too far,
the reclaimer will again begin to allow usable media to
be carried over, and cause abnormally high static
pressure.
5.2.6
When using very fine media (200 mesh and finer
or plastic media), the inlet baffle of the reclaimer may
also need to be removed. Consult the factory before
proceeding with this option.
5.3
Internal Vortex Cylinder
Note: Before adjusting the vortex cylinder, adjust
the damper per Section 5.1. After the static pressure
has been adjusted, adjust the cylinder as follows.
5.3.1
Remove the flex hose from the outlet pipe or
remove the exhauster assembly, depending on the
reclaimer style.
5.3.2
The internal cylinder is visible by looking into the
reclaimer from the top. The cylinder is held in position
with three bolts.
5.3.3
Adjustments are made by loosening the bolts,
and moving the cylinder up or down to achieve the
correct setting. When the correct setting is established,
tighten the bolts to prevent movement.
5.3.4
Start with overall length of the internal tube and
cylinder, when measured from the top of the reclaimer to
the bottom of the inner cylinder equaling the distance
shown in Figure 7. If the reclaimer is rubber lined, add
1/4
″
to the starting point depth.
Reclaimer Size
Starting Point Depth
900
cfm .........................................15 1/2 Inches
1200
cfm .......................................18 1/2 Inches
1800
cfm .......................................20 1/2 Inches
2500
cfm .......................................22 1/2 Inches
3200
cfm .......................................24 1/2 Inches
3600
cfm .......................................25 1/2 Inches
Figure
7
5.3.5 Dusty
Media:
To increase media consumption,
raise the cylinder in 1/4" increments. Do not adjust again
until the media has gone through several cycles, to be
certain that further adjustment is required.
5.3.6 Media Carryover:
To decrease media
consumption, lower the vortex cylinder in 1/4"
increments. NOTE: If the cylinder is lowered too far,
usable media will carryover, and cause abnormally high
static pressure.
5.3.7
When using very fine media (200 mesh and finer
or plastic media), the inlet baffle of the reclaimer may
need to be removed. Consult the factory before
proceeding with this option.
5.4
Metering Valve Adjustment, Figure 8
5.4.1
While blasting, check the media stream through
the blast nozzle, or through each, clear, metering valve
tube. With the correct media/air mixture, media will flow
smoothly through the tube and nozzle.
5.4.2
If media does not flow smoothly, loosen the
locking nut, and adjust the metering screw until the upper
holes in the metering stem are closed-off, and the lower
holes are fully open. See Figure 8. This adjustment is a
starting point.
5.4.3
If pulsation occurs in the media hose, either media
is damp and caked, or not enough air is entering the media
stream. While blasting, loosen the locking nut and slowly
turn the adjusting screw out (counterclockwise when
viewed from the top) until the media flows smoothly.
Tighten the locking nut finger-tight to maintain the setting.