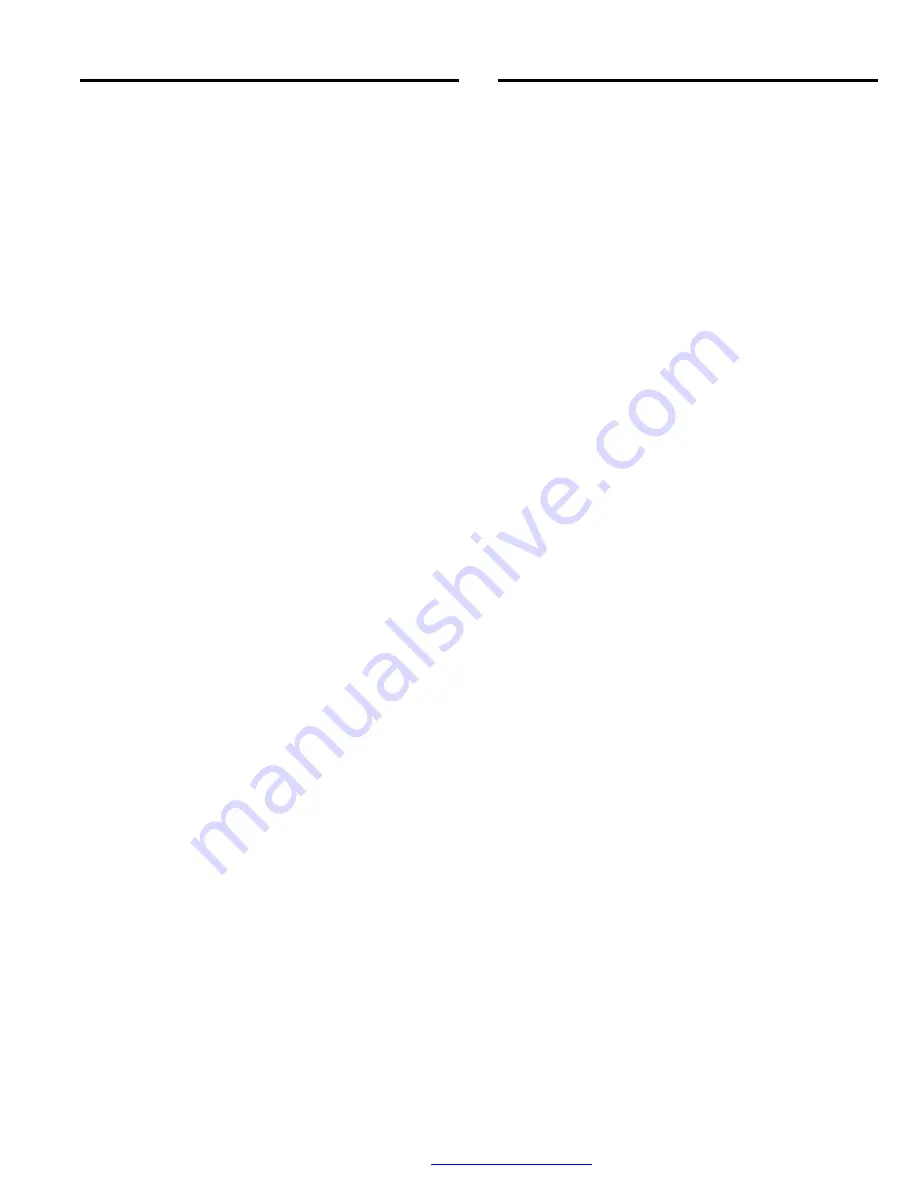
MEDIA RECLAIMER / SEPARATOR
Page 3
© 2005 CLEMCO INDUSTRIES CORP.
•
www.clemcoindustries.com
•
Manual No. 23438
•
Rev. E
1.4.2
A constant static balance is necessary for
efficient separation, as the reclaimer operates by a
centrifugal balance of velocity, particle weight and size.
The best way of ensuring a constant air balance is by
setting, and monitoring static pressure with an optional
manometer. See Section 9.1.
1.4.3
The size and style of the reclaimer is determined
by the size of the enclosure, media size and weight, type
of media, amount of media to be processed, and the
type of dust collection system.
1.5 Wear
Plate
1.5.1
A replaceable wear plate protects the reclaimer
inlet area from rapid wear. The wear plate is standard on
all non rubber lined reclaimers. See Figure 1.
1.6
Rubber Liners Option
1.6.1
Full, rubber lined reclaimers are recommended
when using aggressive media. This option requires a
reclaimer with a bolt-on top, and must be specified when
the reclaimer is ordered.
1.7
Externally Adjusted Vortex Cylinder
1.7.1
The externally adjusted vortex cylinder is
standard on 2500 cfm and larger exhauster-mounted
reclaimers, all job order reclaimers (built around user
specifications), and all pull-through. It is optional on
1800 cfm and smaller exhauster-mounted reclaimers.
1.7.2
The cylinder allows for fine tuning the reclaimer
per Section 5.2
1.8 Blast
Media
NOTE: This section applies to the reclaimer only. It
does not address the limitations of other parts of a
complete recovery system, such as blast room
floors or cabinet hoppers. Any air restrictions
external of the reclaimer will affect usable media
size. Particular attention must be giving to all other
components, especially when considering the use of
heavy and/or aggressive media.
1.8.1
Selection of blast media can play a significant
part in both the productivity and maintenance of the
reclaimer. Most systems with pneumatic recovery use
glass bead, manufactured media, or mineral media.
DO
NOT USE abrasives containing more than one
percent crystalline (free) silica. Obtain a material
safety data sheet (MSDS) for the blast media.
1.8.2
The reclaimer utilizes most common reusable
media specifically manufactured for dry blasting or
peening. The usable media size range depends on the
recovery rate and reclaimer cleaning rate. Several
factors affecting the reclaimer cleaning rate include:
reclaimer size, media friability, contamination of parts
being cleaned, and humidity. Media sizes shown under
the media headings and in Figure 2 are guidelines only,
based on average conditions.
1.8.3
Using media 200 mesh and finer, lightweight
media such as plastic, or glass bead finer than No. 12,
will usually require the removal of the inlet baffle, and
the addition of the externally adjustable vortex cylinder.
1.8.4 Steel:
Steel shot and steel grit are not
recommended for use with reclaimers having a standard
size inlet. 900 cfm and larger reclaimers may be used
with steel media if the inlet hose diameter is reduced as
shown in Figure 2. Conveying hose used with steel
media should have a smooth durable lining. Reclaimers
can be ordered from the factory with conveying hose
appropriately sized for steel grit, or they may be
converted at a later date.
1.8.5 Sand
and
Slag:
Sand should never be used
because of the respiratory hazards associated with the use
of using media containing free silica. Slags are not
recommended because they rapidly breakdown.
1.8.6 Silicon Carbide, Aluminum Oxide, and
Garnet:
These are the most aggressive, high volume
abrasive in the blasting industry.
Aggressive media such
as these may be used with the reclaimer, but the service
life will be reduced on any equipment components which
come in contact with the abrasive. To avoid unscheduled
down time, periodically inspect the reclaimer wear plate,
reclaimer booster exhauster and paddle wheel,
reclaimer vortex tube, reclaimer inlet adapter, hoses,
and nozzle for abrasive wear.
When occasionally using aggressive abrasive, install an
optional aluminum oxide kit. When routinely using these
media, use a fully rubber lined, pull through reclaimer
and a reverse-pulse dust collector. Interior rubber linings
on the blasting enclosures and a boron carbide nozzle
are suggested to prolong service life.
1.8.7 Glass
Bead:
Most beads have been treated to
ensure free-flow operation even under moderately high
humidity conditions. Glass beads subjected to excessive
moisture may be reused after thorough drying and
breaking up of any lumps.
1.8.8 Fine-mesh
Media:
When using very fine media
(200 mesh and finer, #13 glass bead, or lightweight
media), the inlet baffle of the reclaimer may need to be
removed. Consult the factory before proceeding with this
option. Reclaimers can be ordered from the factory