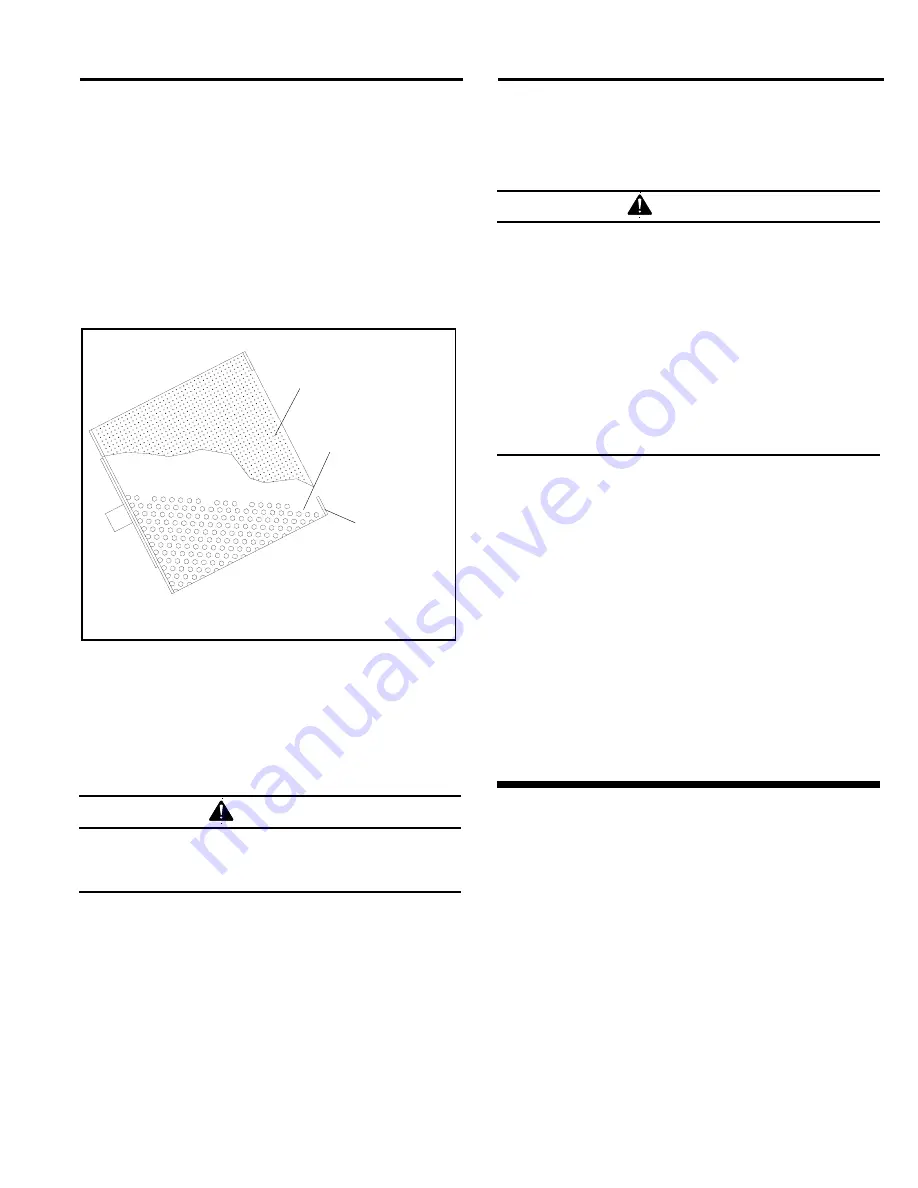
DCM-161 MINI TUMBLE BLAST CABINET
Page 4
3.4.5
Start the blast cycle by setting the timer for the
blast duration. Blasting begins as soon as the timer is
set.
3.3
Loading and Unloading Parts
3.3.1
Parts must be free of oil, water, grease, or other
contaminants that will cause media to clump or
contaminate parts.
3.3.2
Load parts directly into the tumble barrel. Do not
overload the barrel; maximum load should not exceed 25
lb., or the lower edge of the retainer as shown in Figure
2.
Figure
2
3.3.3
Close the cabinet door. Be certain door is
latched securely, or door interlock system will prevent
blasting.
3.4 Blasting
Operation
•
Keep door closed during blasting.
•
Stop blasting immediately if dust leaks are
detected.
3.4.1
Slowly open the air valve on the air supply hose
to the cabinet. Check for air leaks on the initial start up,
and periodically thereafter.
3.4.2
Adjust the pressure regulator (filter/regulator)
located on the side of the cabinet, to the required blast
pressure per Section 4.1.
3.4.3
Load media and parts.
3.4.4
Close door and latch securely.
Shut down the cabinet immediately if dust
discharges from the cabinet or filter bag. Make
sure that the bag is clamped securely over the
exhauster outlet, and that it is not worn or
damaged. Prolonged breathing of any dust
could result in serious lung disease. Short term
ingestion of toxic dust such as lead, poses an
immediate danger to health. Toxicity and health
risk vary with type of media and dust generated
by blasting. Identify all material being removed
by blasting, and obtain a material safety data
sheet for the blast media.
WARNING
Do not load parts
above the bottom
rim of the retainer.
Tumble Barrel
Retainer
3.4.6
Check media flow per Section 4.3.
3.5 Stop
Blasting
3.5.1
Blasting, and barrel rotation, and the exhauster
stop when the timer cycle is complete.
3.5.2
Open the door only enough to disengage the
door interlock, and turn the timer on. Let it run for several
seconds to clear airborne dust, then turn the switch off.
3.5.3
Remove parts and check blast coverage.
3.5.4
When finished, shut off the air supply valve,
drain the air filter.
CAUTION
4.0 ADJUSTMENTS
4.1 Blasting
Pressure
4.1.1
The filter/regulator, enables the user to adjust
blasting pressure to suit the application. The maximum
recommended pressure is 60 psi. Lower pressures may
be used for delicate work. Higher pressure may cause
dust or media to escape from the cabinet.
4.1.2
To adjust, unlock the knob, and turn it clockwise
to increase pressure or counter-clockwise to decrease
pressure. Pressure will usually drop from closed-line
pressure when blasting starts. Once operating pressure
is set, lock the knob to maintain the setting.