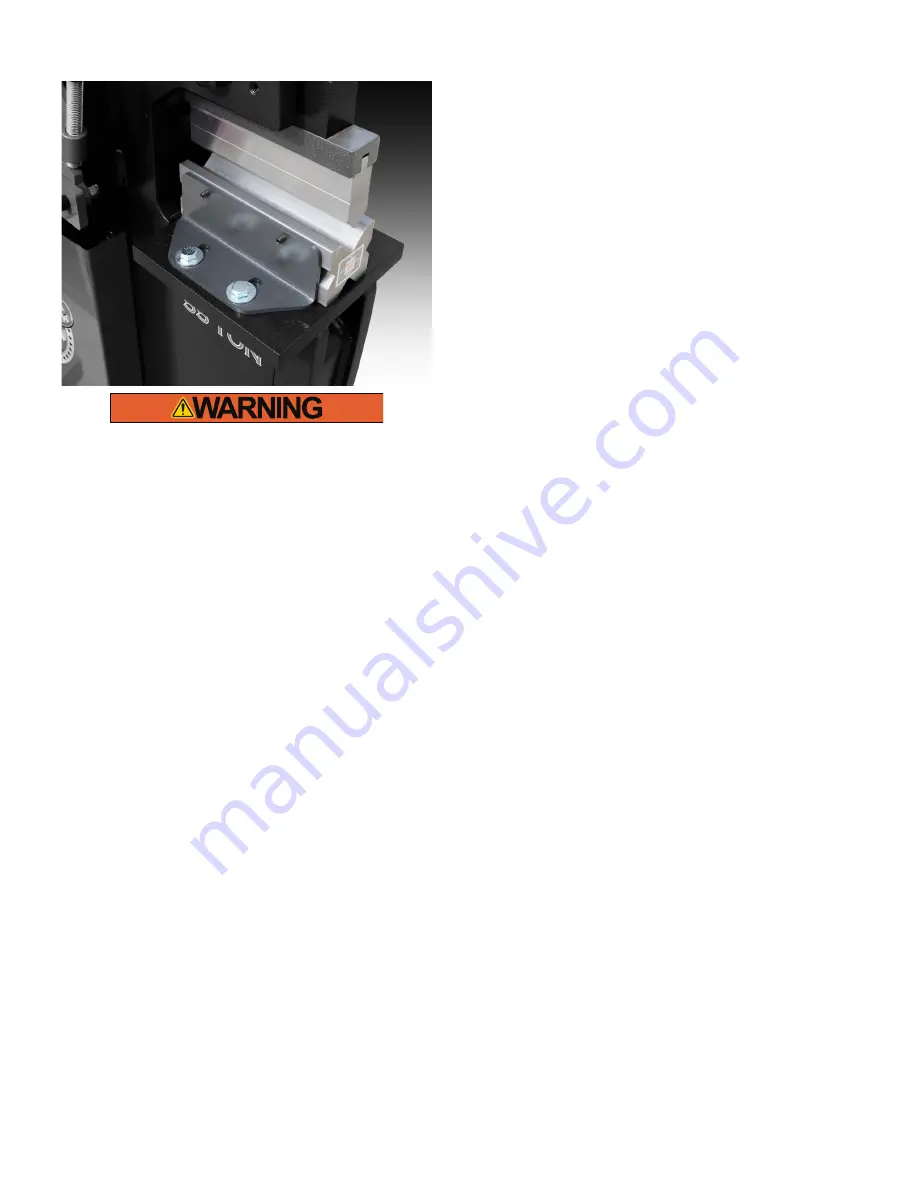
28
The 55 Ton Cleveland Steel Tool Ironworker can accommo-
date an 8" or 10" Press Brake. Press Brake tooling will allow
for the graduated bending of 1/16", 3/16", 1/8" and 1/4" flat
stock up to 90 degrees. This tooling is most effective when
operated with the factory installed Electric Stroke Control fea-
ture.
Setup
Press Brake tooling can be accommodated in either the open
station or punch station of the machine. Press Brake tooling
includes one mounting bracket to secure the “punch” to the
center of the machine, one “punch”, one “4-way die”, and
two bottom brackets that secure the “die” to the base table.
The moving “center” of the ironworker, pushes the top punch
into the shaped die to bend the specified material. If ordered
as a factory installed option, your Press Brake assembly is
setup for immediate operation. If ordered as an option, the
open station or punch station must be cleared of any existing
tooling, material or debris prior to tooling installation. To setup
your Press Brake, please observe the following steps:
Install the punch holder:
1. Remove all tooling and guarding from the open station or
punch station.
2. Secure the punch holder to the moving “center” with
bolts provided. The 1/2" tapped hole is positioned to the
outside of the machine.
3. Position punch in the holder so that the milled relief in the
keyway slips over the holder bolt. Tighten set screws in
the holder to secure the punch.
4. Depress the foot pedal to activate the Press Brake sta-
tion. When the Press Brake operation is complete, re-
lease the foot pedal to return the punch to the neutral
position.
Install the 4-Way Die:
1. Place the die assembly on the Ironworker support table.
2. Loosely secure the two support brackets to the support
table from the underside of the base with four 1/2" bolts,
nuts and washers (provided).
3. Check for punch and die alignment by powering on the
machine and slowly inching down the punch to meet the
bottom die with the foot pedal. Power the machine off.
4. In the event that the punch and die are not aligned,
simply loosen the bolts under the table allowing the die
block to be moved to center the punch. When aligned,
tighten the table bolts to secure the table.
5. Select 1/16", 3/16", 1/8" or 1/4" test material for
bending. Rotate your four-way die to your selected
material thickness. Power the machine on and jog the
center down until the punch pushes the sample material
into the die. If the punch stops before the material has
been formed to a 90 degree angle, a small steel shim
must be placed between the die and support table.
6. Re-install all guarding to the machine prior to machine
use.
Safe Operation
Observe the following guidelines when operating the Press
Brake Station.
• Never exceed the capacities of the machine or tooling
as described in the Ironworker specifications or listed at
the tooling station.
• Keep the Press Brake tooling clean.
• Check Press Brake clearance and alignment at every
tooling change, maintenance cycle or extended Press
Brake operation. Failure to maintain proper clearance
may damage punch, die and support brackets or
adjacent tooling.
• Press material towards the center of the Press Brake
length.
• Do not stack material in the Press Brake station.
• When not in use, remove the Press Brake die from the
holder.
Press Brake Operation
1. Clear the station of any tools or debris prior to powering
the machine on.
2. Turn the Ironworker on and place the material to be
“broken” on top of the bottom die.
3. Center your material within the length of the bottom die.
Bending material to the front or back of the Press Brake
die may damage your Ironworker.
4. Position your material for the desired Press Brake.
Clear your hands from the working area and depress
the foot pedal to activate the Press Brake station. When
the Press Brake operation is complete, release the foot
pedal to return the punch to the neutral position.
Optional Tooling - Press Brake Tooling
Guarding removed for clarity
Summary of Contents for 55 Ton
Page 2: ......
Page 41: ...37 55 Ton Exploded View ...
Page 42: ...38 55 Ton Parts List ...
Page 44: ...40 www clevelandsteeltool com 474 E 105th St Cleveland OH 44108 800 446 4402 ...