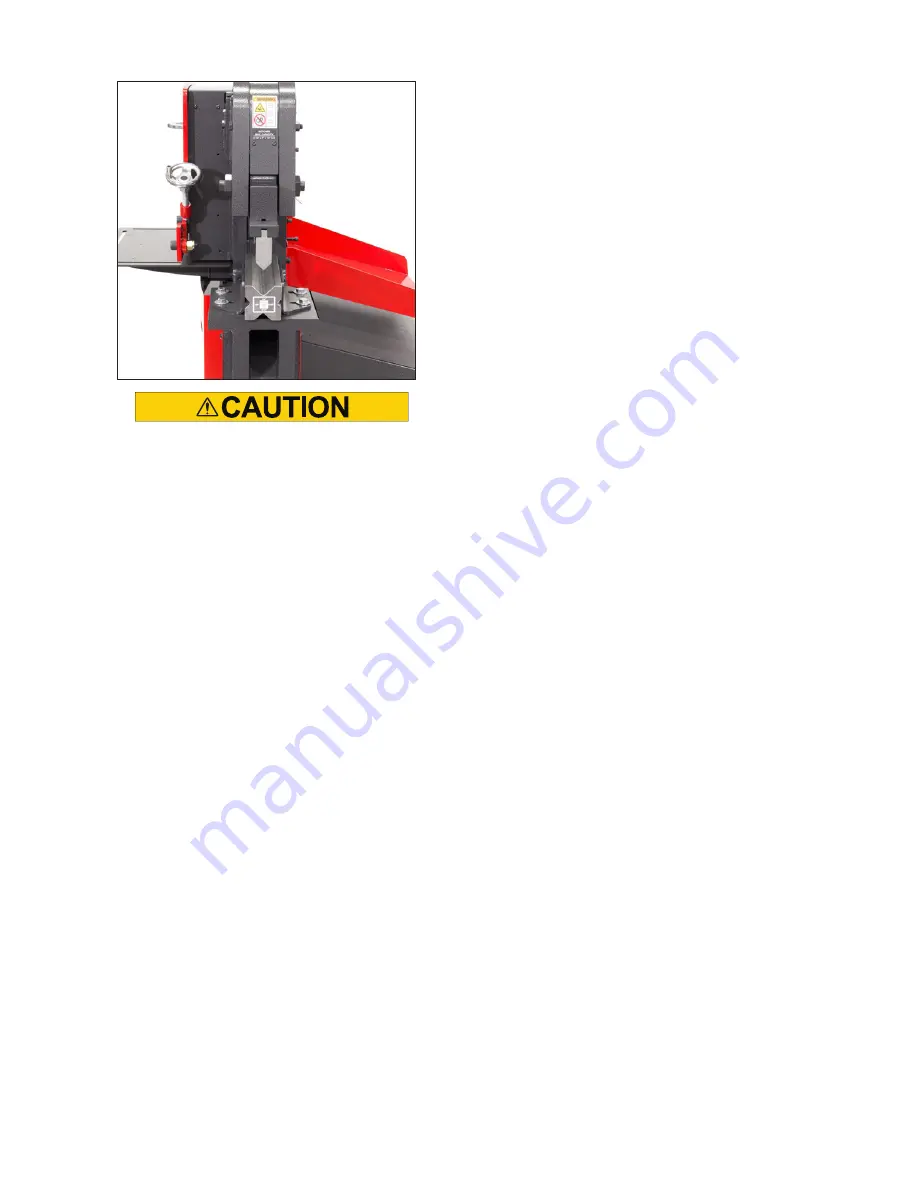
29
Turn off power to machine by depressing the red stop/off
button and lockout upstream power at the main electrical
panel.
Observe the following procedures when maintaining or replacing
components of the Ironworker Press Brake station.
Remove and replace moving Punch:
1. While supporting the punch, carefully remove the allen
screws that secure the punch to the punch holder.
Remove the punch.
2. If the punch holder requires replacement, remove the
two 1/2" socket head cap screws from the punch holder
assembly. Remove punch holder.
3. Clean the keyway in the moving center of any dirt or
debris.
4. Install the new punch holder with the two 1/2" socket
head cap screws. The 1/2" tapped hole is positioned to
the outside of the machine. Tighten the assembly into the
moving center.
5. Position punch in the holder so that the milled relief in the
keyway slips over the holder bolt. Tighten set screws in
the holder to secure the punch.
6. Re-install all guarding to the machine prior to machine
use.
Remove and replace stationary Four-Way Die:
1. Remove four 1/2" bolts, nuts and washers from the die
support brackets.
2. Remove support brackets.
3. Remove old die assembly.
4. Place new die assembly on the Ironworker support table.
5. Loosely secure the two support brackets to the support
table from the underside of the base with four 1/2" bolts,
nuts and washers (provided).
6. Check for punch and die alignment by powering on the
machine and slowly inching down the punch to meet the
bottom die with the foot pedal. Power the machine off.
7. In the event that the punch and die are not aligned, simply
loosen the bolts under the table allowing the die block to
be moved to center the punch. When aligned, tighten the
table bolts to secure the table.
8. Select 1/16", 3/16", 1/8" or 1/4" test material for bending.
Rotate your four-way die to your selected material
thickness. Power the machine on and jog the center down
till the punch pushes the sample material into the die. If
the punch stops before the material has been formed to
a 90 degree angle, a small steel shim must be placed
between the die and support table.
9. Re-install all guarding to the machine prior to machine use.
Maintenance - Press Brake Tooling
Summary of Contents for 55 Ton
Page 2: ......
Page 41: ...37 55 Ton Exploded View ...
Page 42: ...38 55 Ton Parts List ...
Page 44: ...40 www clevelandsteeltool com 474 E 105th St Cleveland OH 44108 800 446 4402 ...