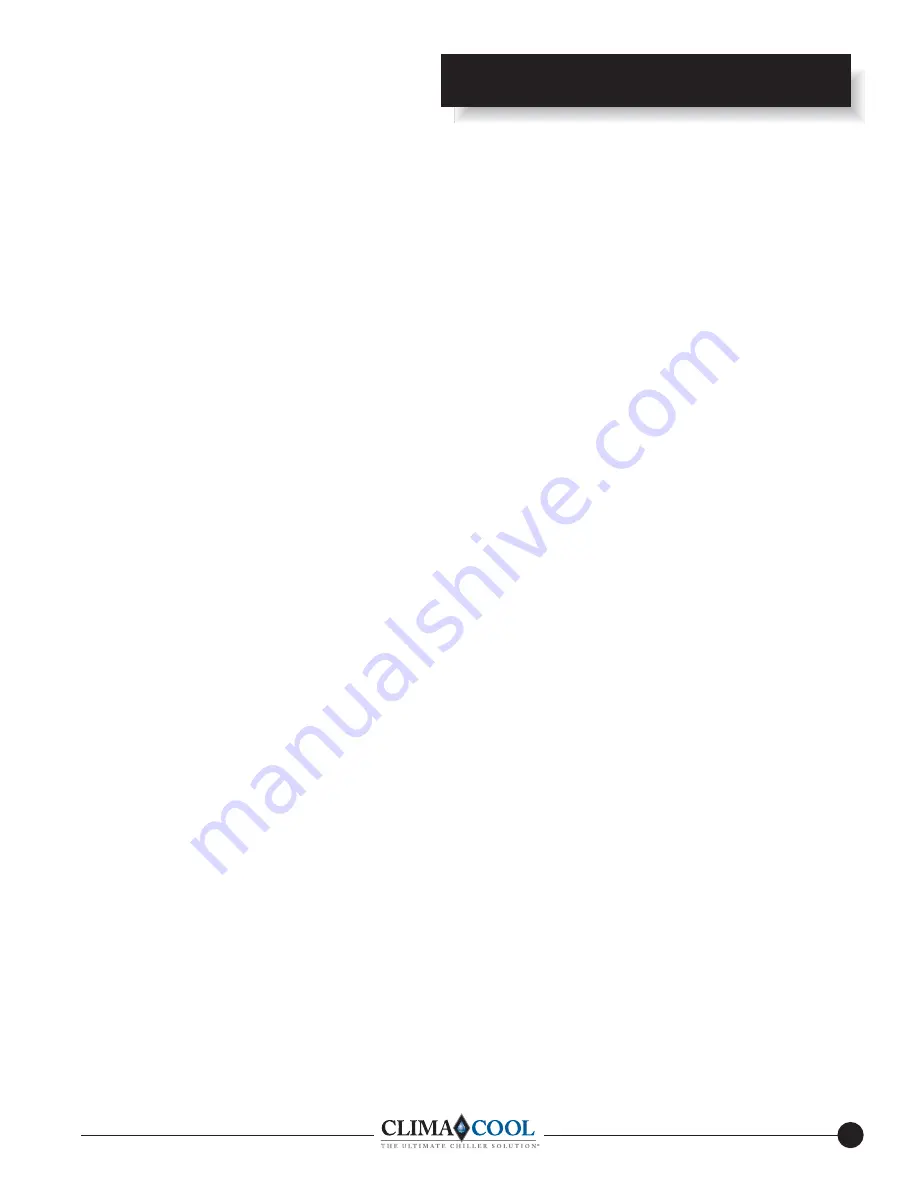
^^^JSPTHJVVSJVYWJVT
®
25
the "field wiring" terminal strip (terminals 8 &9). With
jumper in place, turn on the selector switch marked
"compressor #1" to bump the compressor and check for
proper rotation. Use pressure gauges to verify proper
rotation. Once this is complete and correct rotation
is verified, override output with DX commissioning
program or place a jumper between compressor 2 start
terminals on the control terminal strip (terminals 10 &
11). Turn on the switch marked "compressor #2" to bump
the compressor and verify that circuit #2 compressor has
correct rotation. Use pressure gauges to verify proper
rotation. Always use proper electrical safety precautions.
4. Slowly close the chiller water inlet isolating valve and
note that the flow switch stops the machine. Note the flow
rate at which this occurs. If too much flow is lost before
chiller is stopped, reset switch setting. The flow switch
should be set so the chiller shuts down when the flow rate
to each evaporator and condenser water circuits drops
below 60% of rated ARI full load conditions (indicating a
10°F temperature change through both the evaporator and
condenser heat exchangers).
5. Repeat the tests of all other safety interlocks which may
be connected.
6. The anti-freeze thermostat for each module should be set
to trip when the leaving chilled water temperature drops
below 38°F.
Start Up
An anti-short cycle timer protects the chiller and there will
be a delay before the controller will allow the compressors
to start.
1. If the chilled water temperature is above the normal
operating level, all load should be removed from the
chilled water system and the suction temperature should
be monitored to prevent high current draw.
2. If the condenser water temperature is below the normal
operating level, ensure that the condenser water
temperature control is in the correct position.
3. Re-install all fuses and set the controller.
4. When all temperatures are within operating limits, all
Start Up
high and low pressure safety switches should be tested
for each refrigeration system.
5. The condenser temperature controller should be
checked. Once stable conditions have been achieved,
the refrigeration system's high and low pressures,
compressor amp draw, voltage input level, and water
system temperatures and pressures should be logged for
each chiller module separately.
6. Check that oil level is between 1/3 and 1/2 of the sight
glass. See page 35 - Oil Levels.
7. The action of the controller should be checked for correct
operation and control.
Mechanical and General
All covers, panels and doors should be in place and secured.
Start Up Documentation
All start-up paperwork and documentation must be submitted
to ClimaCool. Future warranty claims cannot be processed
without the Start up documentation on file.
Supervision and Training
ClimaCool provides factory supervision and training as an
extra cost option per installation of one or multiple chiller
modules. This training is to provide general information
about the installation and operating characteristics to the
start-up contractor. Cost for the start-up service contractor
is not ClimaCool’s responsibility. Supervision and training
for new service contractors is also available, contact
ClimaCool for a quotation.
ClimaCool’s supervision and training is not intended to take
the place of the installation and start-up contractor. The
start-up contractor is responsible for complete mechanical
and electrical installation and adherence to all local
and federal codes or regulations. Consult an authorized
ClimaCool representative for a list of authorized start-up
service contractors in your area.