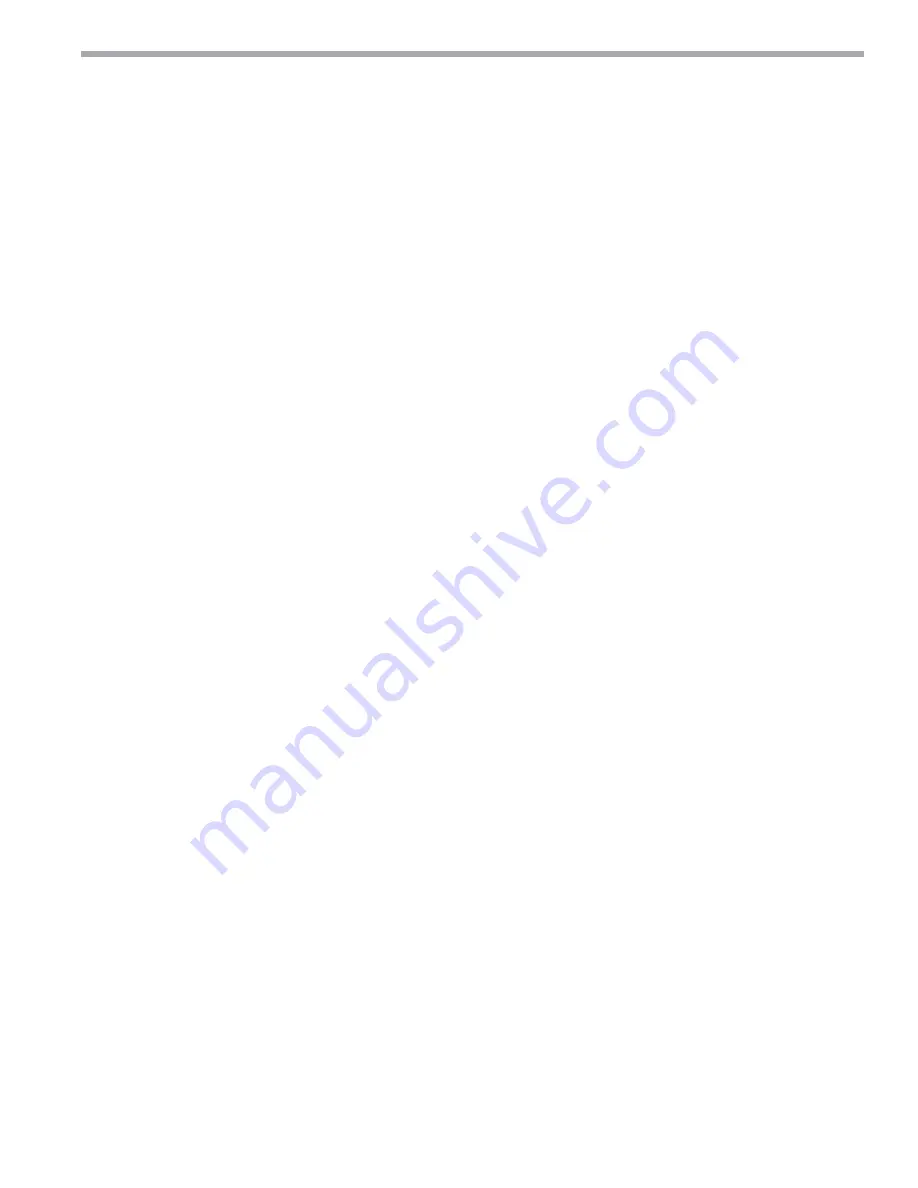
57
c l i m a t e m a s t e r. c o m
T H E S M A R T S O L U T I O N F O R E N E R G Y E F F I C I E N C Y
Tr a n q u i l i t y
®
2 0 ( T S ) S e r i e s
R e v. : 0 6 / 1 7 / 1 5
Preventive Maintenance
Water Coil Maintenance -
(Direct ground water
applications only) If the system is installed in an area with
a known high mineral content (125 P.P.M. or greater) in
the water, it is best to establish a periodic maintenance
schedule with the owner so the coil can be checked
regularly. Consult the well water applications section
of this manual for a more detailed water coil material
selection. Should periodic coil cleaning be necessary, use
standard coil cleaning procedures, which are compatible
with the heat exchanger material and copper water
lines. Generally, the more water fl owing through the unit,
the less chance for scaling. Therefore, 1.5 gpm per ton
[1.6 l/m per kW] is recommended as a minimum fl ow.
Minimum fl ow rate for entering water temperatures
below 50°F [10°C] is 2.0 gpm per ton [2.2 l/m per kW].
Water Coil Maintenance -
(All other water loop
applications) Generally water coil maintenance is not
needed for closed loop systems. However, if the piping
is known to have high dirt or debris content, it is best
to establish a periodic maintenance schedule with the
owner so the water coil can be checked regularly. Dirty
installations are typically the result of deterioration of iron
or galvanized piping or components in the system. Open
cooling towers requiring heavy chemical treatment and
mineral buildup through water use can also contribute
to higher maintenance. Should periodic coil cleaning be
necessary, use standard coil cleaning procedures, which
are compatible with both the heat exchanger material
and copper water lines. Generally, the more water fl owing
through the unit, the less chance for scaling. However,
fl ow rates over 3 gpm per ton (3.9 l/m per kW) can
produce water (or debris) velocities that can erode the
heat exchanger wall and ultimately produce leaks.
Hot Water Generator Coils -
See water coil
maintenance for ground water units. If the potable
water is hard or not chemically softened, the high
temperatures of the desuperheater will tend to scale
even quicker than the water coil and may need more
frequent inspections. In areas with extremely hard water,
a HWG is not recommended.
Filters -
Filters must be clean to obtain maximum
performance. Filters should be inspected every month
under normal operating conditions and be replaced
when necessary. Units should never be operated without
a fi lter.
Washable, high effi ciency, electrostatic fi lters, when dirty,
can exhibit a very high pressure drop for the fan motor
and reduce air fl ow, resulting in poor performance. It is
especially important to provide consistent washing of
these fi lters (in the opposite direction of the normal air
fl ow) once per month using a high pressure wash similar
to those found at self-serve car washes.
Condensate Drain -
In areas where airborne bacteria
may produce a “slimy” substance in the drain pan, it may
be necessary to treat the drain pan chemically with an
algaecide approximately every three months to minimize
the problem. The condensate pan may also need to be
cleaned periodically to ensure indoor air quality. The
condensate drain can pick up lint and dirt, especially with
dirty fi lters. Inspect the drain twice a year to avoid the
possibility of plugging and eventual overfl ow.
Compressor -
Conduct annual amperage checks to
ensure that amp draw is no more than 10% greater than
indicated on the serial plate data.
Fan Motors -
All units have lubricated fan motors. Fan
motors should never be lubricated unless obvious, dry
operation is suspected. Periodic maintenance oiling is
not recommended, as it will result in dirt accumulating in
the excess oil and cause eventual motor failure. Conduct
annual dry operation check and amperage check to
ensure amp draw is no more than 10% greater than
indicated on serial plate data.
Air Coil -
The air coil must be cleaned to obtain
maximum performance. Check once a year under normal
operating conditions and, if dirty, brush or vacuum clean.
Care must be taken not to damage the aluminum fi ns
while cleaning. CAUTION: Fin edges are sharp.
Cabinet -
Do not allow water to stay in contact with the
cabinet for long periods of time to prevent corrosion of
the cabinet sheet metal. Generally, vertical cabinets are
set up from the fl oor a few inches [7 - 8 cm] to prevent
water from entering the cabinet. The cabinet can be
cleaned using a mild detergent.
Refrigerant System -
To maintain sealed circuit integrity,
do not install service gauges unless unit operation
appears abnormal. Reference the operating charts for
pressures and temperatures. Verify that air and water
fl ow rates are at proper levels before servicing the
refrigerant circuit.