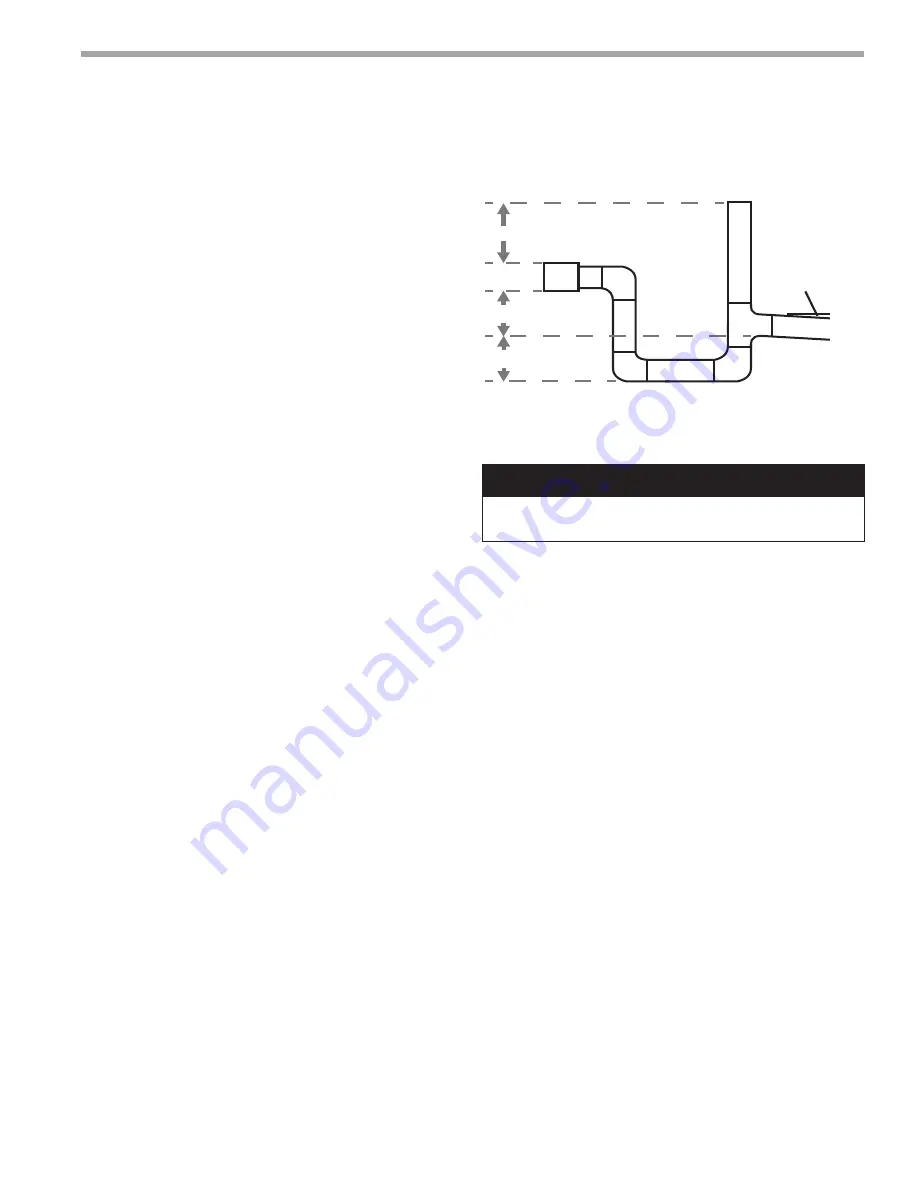
11
T H E S M A R T S O L U T I O N F O R E N E R G Y E F F I C I E N C Y
Tr a n q u i l i t y
®
( T R ) S e r i e s
R e v. : N o v e m b e r 2 , 2 0 2 0
c l i m a t e m a s t e r. c o m
2”
1.5”
1.5”
* Some units include a painted drain connection.
Using a threaded pipe or similar device to clear
any excess paint accumulated inside this fitting
may ease final drain line installation.
1/8” Per
Foot
Condensate Piping - Horizontal Units -
A condensate
drain line must be installed and pitched away for the unit
to allow for proper drainage. This connection must meet all
local plumbing/building codes.
Pitch the unit toward the drain as shown in Figure 2 to
improve the condensate drainage. On small units (less than
2.5 tons/8.8 kW), ensure that unit pitch does not cause
condensate leaks inside the cabinet.
Install condensate trap at each unit with the top of the trap
positioned below the unit condensate drain connection as
shown in Figure 6. Design the depth of the trap (water-
seal) based upon the amount of ESP capability of the
blower (where 2 inches [51 mm] of ESP capability requires
2 inches [51 mm] of trap depth). As a general rule, 1-1/2
inch [38 mm] trap depth is the minimum.
Each unit must be installed with its own individual trap and
connection to the condensate line (main) or riser. Provide
a means to flush or blow out the condensate line. DO NOT
install units with a common trap and/or vent.
Always vent the condensate line when dirt or air can
collect in the line or a long horizontal drain line is required.
Also vent when large units are working against higher
external static pressure than other units connected to the
same condensate main since this may cause poor drainage
for all units on the line.
WHEN A VENT IS INSTALLED IN
THE DRAIN LINE, IT MUST BE LOCATED AFTER THE
TRAP IN THE DIRECTION OF THE CONDENSATE FLOW.
Horizontal Installation
Figure 6: Horizontal Condensate Connection
CAUTION!
Ensure condensate line is pitched toward drain
1/8 inch per ft [11mm per m] of run.
�
CAUTION!
�
Duct System Installation -
Proper duct sizing and design
is critical to the performance of the unit. The duct system
should be designed to allow adequate and even airflow
through the unit during operation. Air flow through the
unit MUST be at or above the minimum stated airflow
for the unit to avoid equipment damage. Duct systems
should be designed for quiet operation. Refer to Figure 3
for horizontal duct system details or Figure 8 for vertical
duct system details. A flexible connector is recommended
for both discharge and return air duct connections on
metal duct systems to eliminate the transfer of vibration
to the duct system. To maximize sound attenuation of
the unit blower, the supply and return plenums should
include internal fiberglass duct liner or be constructed
from ductboard for the first few feet. Application of the
unit to uninsulated ductwork in an unconditioned space
is not recommended, as the unit’s performance may be
adversely affected.
At least one 90° elbow should be included in the supply
duct to reduce air noise. If air noise or excessive air flow is
a problem, the blower speed can be changed. For airflow
charts, consult submittal data for the series and model of
the specific unit.
If the unit is connected to existing ductwork, a previous
check should have been made to ensure that the
ductwork has the capacity to handle the airflow required
for the unit. If ducting is too small, as in the replacement
of a heating only system, larger ductwork should be
installed. All existing ductwork should be checked for
leaks and repaired as necessary.
Condensate Piping
Duct System Installation
Summary of Contents for Tranquility TR Series
Page 2: ......