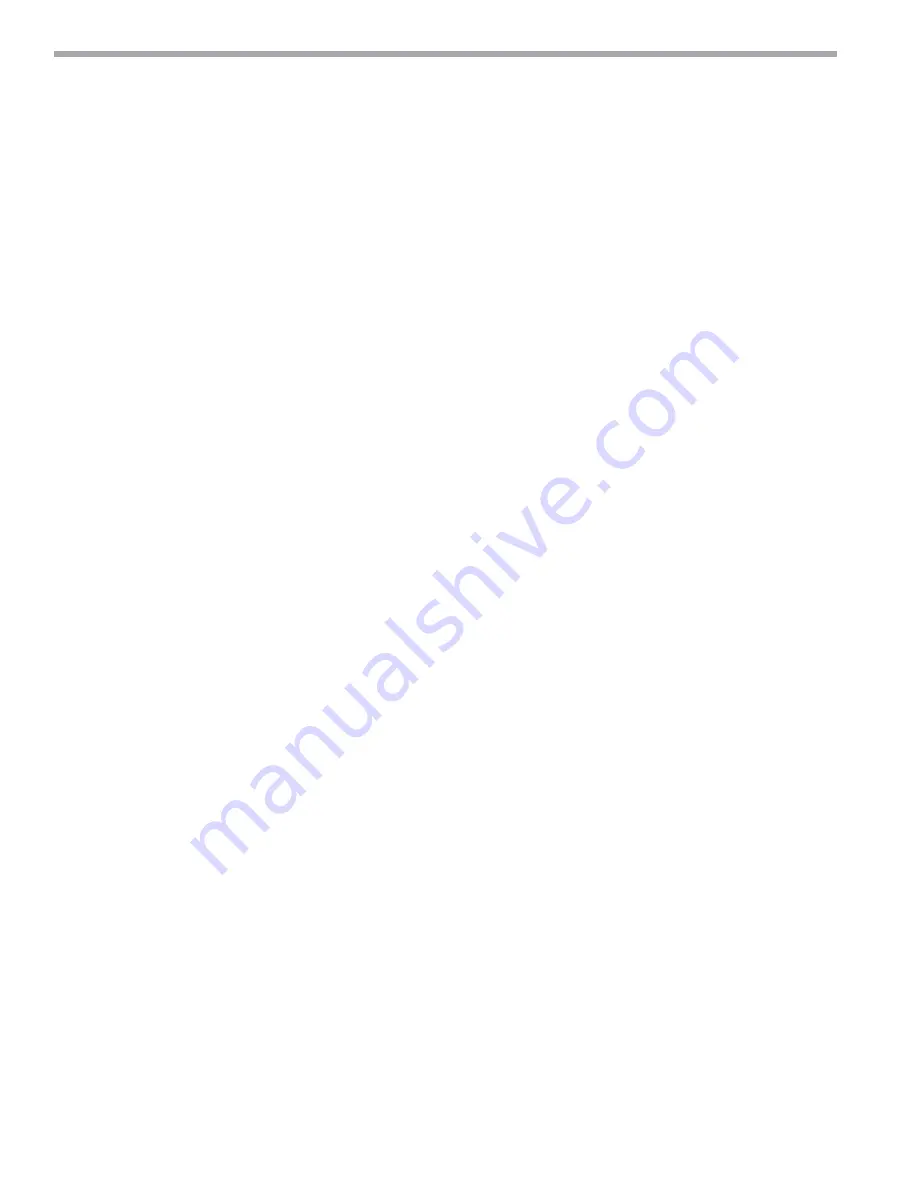
42
C l i m a t e M a s t e r Wa t e r- S o u rc e H e a t P u m p s
C L I M A T E M A S T E R W A T E R - S O U R C E H E A T P U M P S
Tr a n q u i l i t y
®
3 0 ( T T ) S e r i e s
R e v. : 0 7 / 1 8 / 1 3
Piping System Cleaning and Flushing
- Cleaning and
fl ushing the WLHP piping system is the single most
important step to ensure proper start-up and continued
effi cient operation of the system.
Follow the instructions below to properly clean and fl ush
the system:
1. Ensure that electrical power to the unit is
disconnected.
2. Install the system with the supply hose connected
directly to the return riser valve. Use a single length of
fl exible hose.
3. Open all air vents. Fill the system with water. DO NOT
allow system to overfl ow. Bleed all air from the system.
Pressurize and check the system for leaks and repair as
appropriate. ClimaDry
®
-equipped units have a manual
air bleed valve at the top of the reheat coil. This
valve must be used to bleed the air from the reheat
coil after fi lling the system, for ClimaDry
®
to operate
properly.
4. Verify that all strainers are in place (ClimateMaster
recommends a strainer with a #20 stainless steel
wire mesh). Start the pumps, and systematically
check each vent to ensure that all air is bled from the
system.
5. Verify that make-up water is available. Adjust make-up
water as required to replace the air which was bled
from the system. Check and adjust the water/air level
in the expansion tank.
6. Set the boiler to raise the loop temperature to
approximately 86°F [30°C]. Open a drain at the
lowest point in the system. Adjust the make-up water
replacement rate to equal the rate of bleed.
7. Refi ll the system and add trisodium phosphate in
a proportion of approximately one pound per 150
gallons (.8 kg per 1000 l) of water (or other equivalent
approved cleaning agent). Reset the boiler to raise
the loop temperature to 100°F [38°C]. Circulate the
solution for a minimum of 8 to 24 hours. At the end
of this period, shut off the circulating pump and drain
the solution. Repeat system cleaning if desired.
8. When the cleaning process is complete, remove the
short-circuited hoses. Reconnect the hoses to the
proper supply, and return the connections to each of
the units. Refi ll the system and bleed off all air.
9. Test the system pH with litmus paper. The system
water should be in the range of pH 6.0 - 8.5 (see
table 3). Add chemicals, as appropriate to maintain
neutral pH levels.
10. When the system is successfully cleaned, fl ushed,
refi lled and bled, check the main system panels,
safety cutouts and alarms. Set the controls to properly
maintain loop temperatures.
DO NOT use “Stop Leak” or similar chemical agent in
this system. Addition of chemicals of this type to the
loop water will foul the heat exchanger and inhibit unit
operation.
Note: The manufacturer strongly recommends all
piping connections, both internal and external to the
unit, be pressure tested by an appropriate method
prior to any fi nishing of the interior space or before
access to all connections is limited. Test pressure may
not exceed the maximum allowable pressure for the
unit and all components within the water system.
The manufacturer will not be responsible or liable
for damages from water leaks due to inadequate or
lack of a pressurized leak test, or damages caused
by exceeding the maximum pressure rating during
installation.
Piping System Cleaning and Flushing