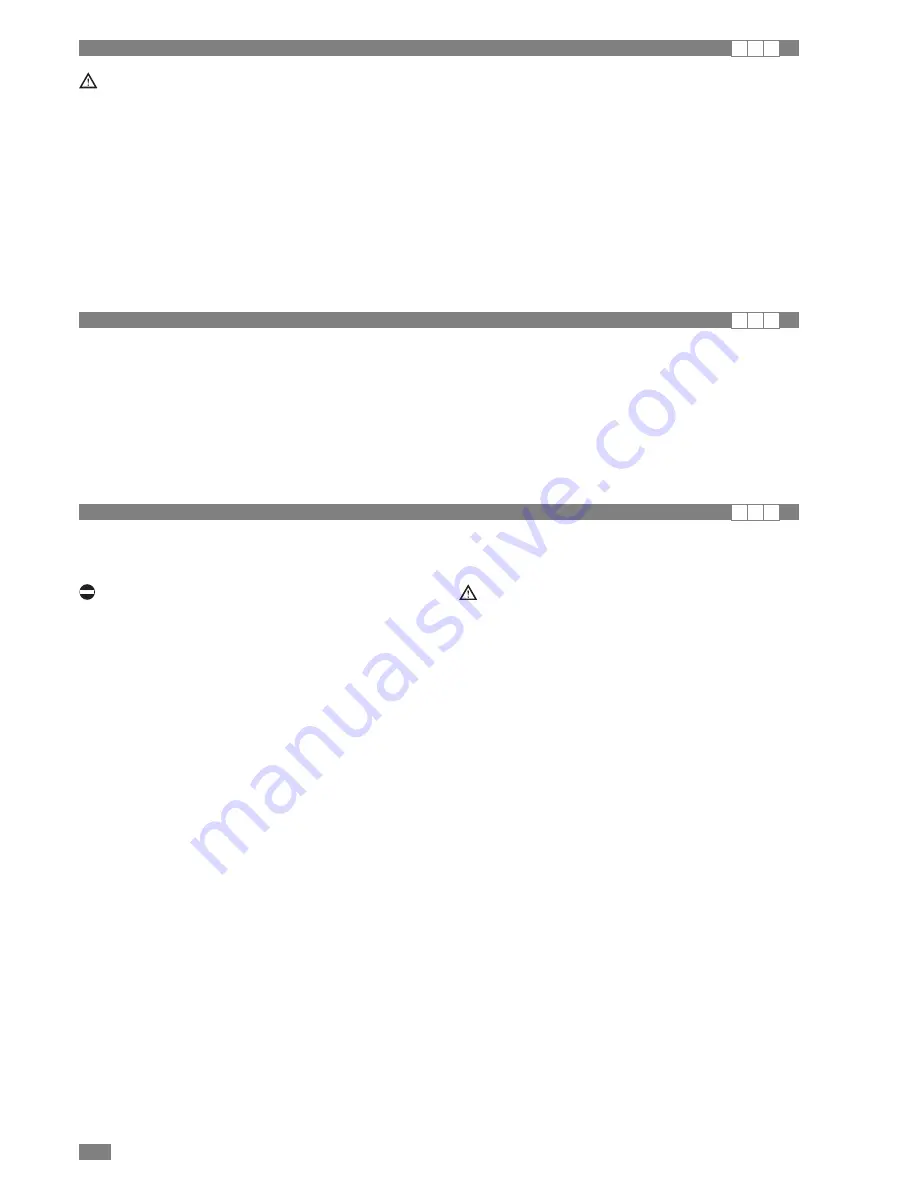
GENERAL WARNINGS
4
BRH FF
GB 01/20010
U I A
FUNDAMENTAL SAFETY RULES
U I A
WAIVER OF LIABILITY
U I A
These appliances have been designed
to chill water
and must be used in applications compatible with their
performance characteristics.
Incorrect installation, regulation and maintenance or
improper use absolve the manufacturer from all liability,
whether contractual or otherwise, for damage to people,
animals or things.
Only those applications specifically indicated in this list
are permitted.
The warranty is void
if the above instructions are not
respected and if the unit is started up for the first time with-
out the presence of personnel authorised by the Company
(where specified in the supply contract) who should draw up
a “start-up” report.
The documents supplied with the unit
must be consigned
to the owner who should keep them carefully for future con-
sultation in the event of maintenance or service.
When the items are consigned by the carrier,
check that
the packaging and the unit are undamaged. If damage or
missing components are noted, indicate this on the delivery
note. A formal complaint should be sent via fax or registered
post to the After Sales Department within eight days from
the date of receipt of the items.
When operating equipment involving the use of electricity and water, a number of fundamental safety rules must be observed,
namely:
This publication is the sole property of
Climaveneta
. Any
reproduction or disclosure of such is strictly prohibited with-
out the written authorisation of
Climaveneta
.
This document has been prepared with maximum care and
attention paid to the content shown. Nonetheless,
Cli-
maveneta
waives all liability deriving from the use of such
document.
Read this document carefully. All work must be performed,
components selected and materials used in complete accor-
dance with the legislation in force in material in the country
concerned, and considering the operating conditions and
intended uses of the system, by qualified personnel.
The unit must not be used
by children or by unfit per-
sons without suitable supervision.
Do not touch the unit
with bare feet or with wet or
damp parts of the body.
Never perform any cleaning operations
before having
disconnected the unit from the mains power supply.
Do not modify safety
or control devices without authori-
sation and instructions from the manufacturer.
Do not pull
, detach or twist the electrical cables coming
from the unit, even when disconnected from the mains
electricity supply.
Do not open doors or panels
providing access to the
internal parts of the unit without first switching the unit
OFF.
Do not stand
or sit on the unit and/or rest objects of any
kind on top of it.
Do not spray
or throw water directly on the appliance.
Do not dispose of
, abandon or leave within reach of
children packaging materials (cardboard, staples, plastic
bags, etc) as they may represent a hazard.
Respect safety distances
between the unit and other
equipment or structures. Guarantee adequate space for
access to the unit for maintenance and/or service opera-
tions.
Power supply
: the cross section of the electrical cables
must be adequate for the power of the unit and the power
supply voltage must correspond with the value indicated
on the respective units. All units must be earthed in con-
formity with legislation in force in the country concerned.
Water connections
should be carried out as indicated in
the instructions to guarantee correct operation of the unit.
Add glycol to the water circuit if the unit is not used dur-
ing the winter or the circuit is not emptied (only if there is
the risk of freezing).
Handle the unit
with the utmost care (see weight distrib-
ution table) to avoid damage.