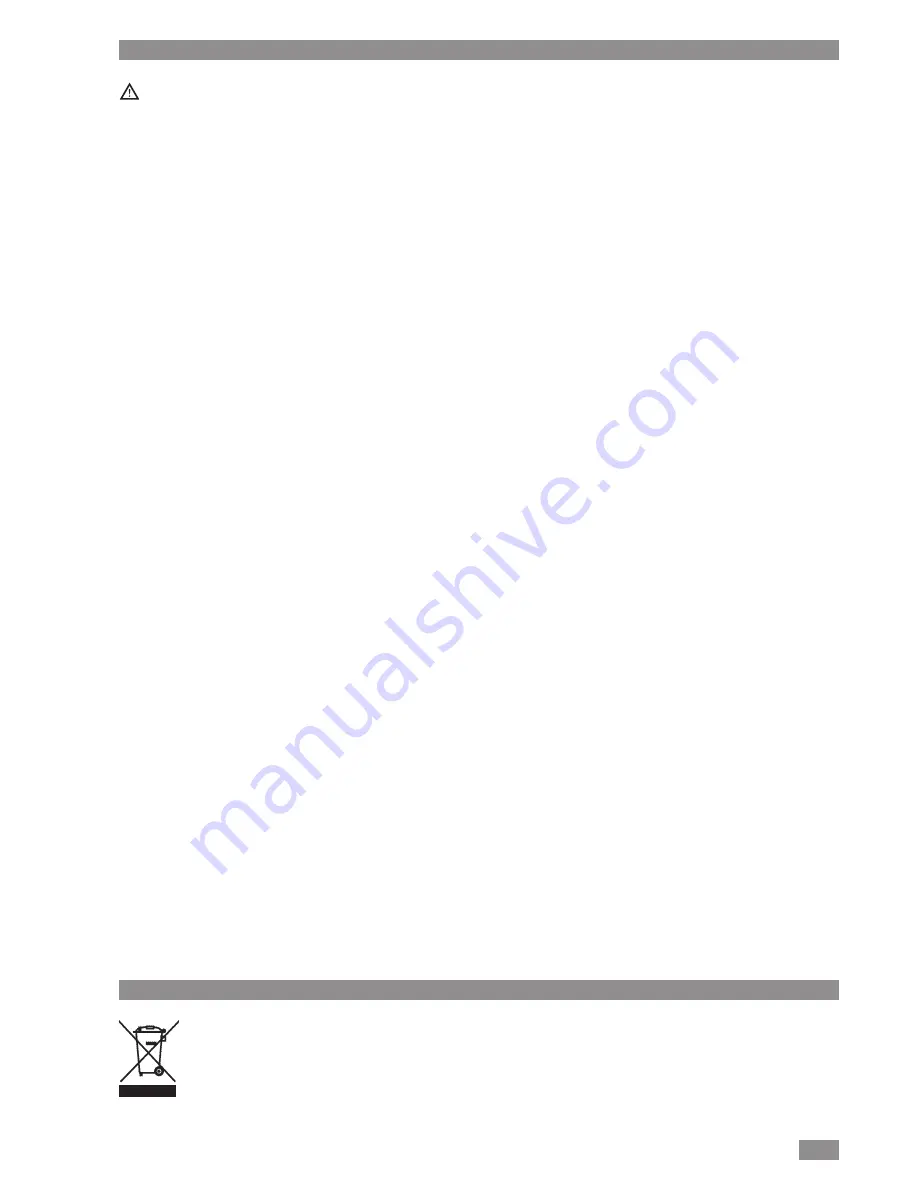
EN
i-ACCURATE i-AX - i-AW - i-AD - i-AT - i-AF
63
MAINTENANCE
Every components replacement (compressor, safety presso-
stat, liquid receiver, ecc.) have to consider the main compo-
nent list enclosed in the unit.
This section, aimed above all for the end user, is extremely impor-
tant for the correct operation of the appliance.
Just a few operations completed scrupulously and regularly will
avoid serious damage to the components. Only authorized and
specialist personnel can operate into the units.
The maintenance operations can be summarised as follows:
- Clean the air filter.
- Check and clean the condenser coils
- Check the water-cooled condensers for fouling.
- Check and clean the drains.
- Check the humidification system.
- General examination of the overall operation of the appliance.
- Visual check of the condition of the pressurised containers.
Cleaning the air filter
The gradual fouling of the filters reduces the flow-rate of the con-
ditioned air, with a consequent reduction in cooling capacity.
In the direct expansion units, a reduction in the air flow-rate may
cause the activation of the low pressure switch and/or cause seri-
ous damage to the compressor.
This can be avoided by the periodical cleaning of the filters.
The frequency at which the filters must be checked exclusively
depends on the amount of dust in the environment.
In any case, the following are recommended:
- Every week check that the filters are clean
- Every two weeks clean the filters with a vacuum cleaner
- Every month wash the filters with soapy water
- Every 6 months replace the filters.
It is clear that the recommended times are purely indicative, and
in some cases it may be necessary to increase the frequency of
the checks and maintenance operations.
These operations must be carried out with the unit off and after
having made sure that the appliance is disconnected from the
power supply.
Checking and cleaning the condenser coils
In the hotter period, when the unit operates at maximum capaci-
ty, the condensing coils must be able to offer the maximum heat
exchange. Normally installed outside or communicating with the
outside, these may pick up dirt such as paper, dry leaves and dust,
thus reducing the heat exchange.
Make sure that this situation does not arise.
Failure to perform maintenance will cause the activation of the
high pressure switch and the unit to shutdown.
Frequently check the condition of the heat exchanger during the
poplar pollination period or the autumn (falling leaves).
Remove any objects accumulated on the coil and wash with a jet
of water. These operations must be carried out with the unit off
and after having made sure that the appliance is disconnected
from the power supply.
Checking the water-cooled condensers for fouling
To check the water-cooled condensers for fouling, simply check
the water inlet and outlet temperature and compare it against the
condensing temperature.
Normally, for good heat exchange, the difference between the
water outlet temperature and the condensing temperature must
be 5.8°C. Increases in these values, over time, indicate a reduction
in efficiency and consequently the fouling of the condenser.
The condenser is cleaned by chemical washing and must be per-
formed by specialist personnel. This operation must be carried
out with the unit off and after having made sure that the appliance
is disconnected from the power supply).
Checking and cleaning the drains
All the water drains (humidifier and condensate) must ensure
perfect drainage, to avoid flooding in the room.
When the humidifiers drain the water, they discharge a quantity
of lime scale that depends on the hardness of the supply water.
This lime scale may accumulate in the bottom of the drain hose
and block the flow of water. If cleaning is required, add ordinary
descaler to the section of circuit involved. This operation must be
carried out with the unit off and after having made sure that the
appliance is disconnected from the power supply.
Checking the drive belt
On the units with fans coupled to the electric motor by pulleys
and drive belts, after a certain number of operating hours the belt
may become loose, sliding on the pulleys and causing excessive
wear. This situation, if it persists, causes overheating and conse-
quently the breakage of the belt. Loosening can be resolved using
the special belt tightener fitted on the appliance (this operation
must be carried out with the unit off and after having made sure
that the appliance is disconnected from the power supply). Check
the tension of the drive belts once a month. Avoid excessively
tightening the belts, as this may cause damage to the bearings.
General examination of operation
This is a general examination aimed at comparing the operation
of the appliance with the last check performed. Consequently, any
differences in the operating characteristics over time can be high-
lighted. A detailed and periodical visual check of the appliance and
general cleaning are always important to ensure correct opera-
tion. The above-mentioned operations can in general be per-
formed once a month. Naturally, in special situations and specific
installations the frequency may change. A well maintained system
is unlikely to cause disruptions and stoppages to the production
cycles. After 10 years working a complete checking is recom-
mended.
Visual check of the condition of the pressurised containers
Check the condition of the pressurised containers at least once a
year (if these are fitted). It is very important to check that rust
does not form on the surface, that there is no corrosion and that
there are no visible deformations. If not controlled and stopped,
surface oxidation and corrosion will over time cause a decrease
in the thickness of the container and a consequent reduction in
its mechanical strength. Protect with paint and/or corrosion
proofing products. In the event of visible deformations, stop the
unit and contact the nearest service centre.
DISMANTLING
IMPORTANT INFORMATIONS FOR COR-
RECT DISMANTLING OF THE UNIT
ACCORDING TO CE 2002/96/CE
If the unit has to be dismantled, this operation must be done by
suitable local authority. The correct dismantling avoids any nega-
tive enviromental consequences and allows significant benefits in
terms of energy saving and resource.
Summary of Contents for i-accurate
Page 2: ......