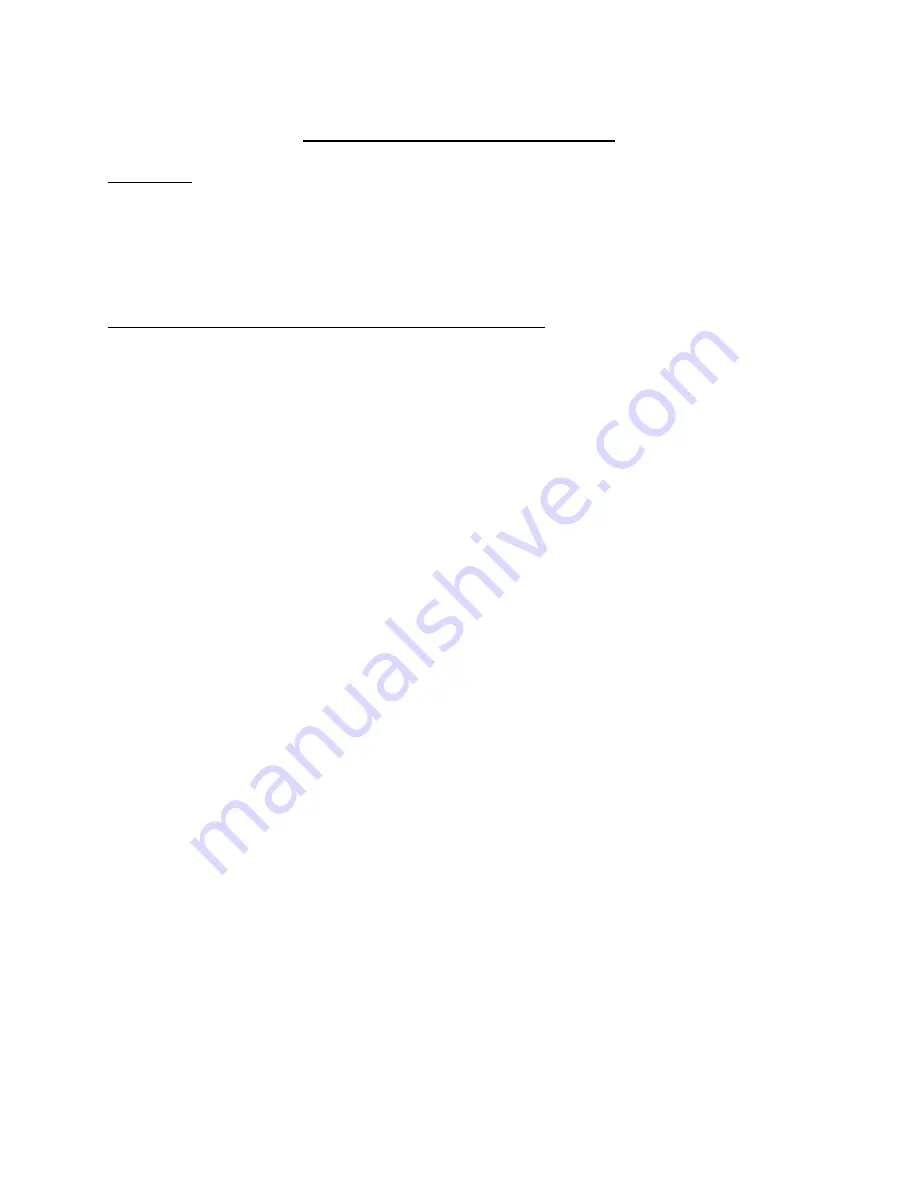
FIELD WIRING INSTRUCTIONS
GENERAL
Cleaner drives and variable controls are available for NEC Class II, Division I, Group G or
Class II, Division II, Group G applications. For additional drive installation instructions, see
the manual section for field wiring.
NEC CLASS II, DIVISION II, GROUP G INSTALLATION
The motors and drive controls supplied with the cleaner meet the requirements of the
National Cod for this type of installation. The customer power and field wiring requirements
are shown on the wiring drawing. All field wiring and electrical components must adhere to
the NEC and/or local electrical code requirements, and are not the responsibility of the
manufacturer.
The following instructions apply to CLIPPER Conquest cleaner installations where National
Electric Code requirements of Class II, Division II, Group G (TEFC motors, NEMA 4
enclosures) apply.
The cleaners with their respective motors, motor controllers and operator variable control
panels have been factory tested and adjusted. No further adjustment of the DC motor
controller should be required at the installation site. The installer should refer to wiring
drawing (TEFC) for wiring (shown in dashed lines) and power requirements (disconnects,
motor starter/relay. All field wiring and electrical components must adhere to the NEC
and/or local electrical code requirements, and are not the responsibility of A. T. Ferrell
Company hereafter referred to as the manufacturer.
All control line wiring should be run in separate conduit
Low voltage wiring between DC or AC motor controllers, operator stations or RPM
pickup leads must not be combined with high voltage power wiring in common
conduits. Movement of factory installed electrical components can affect warranty.