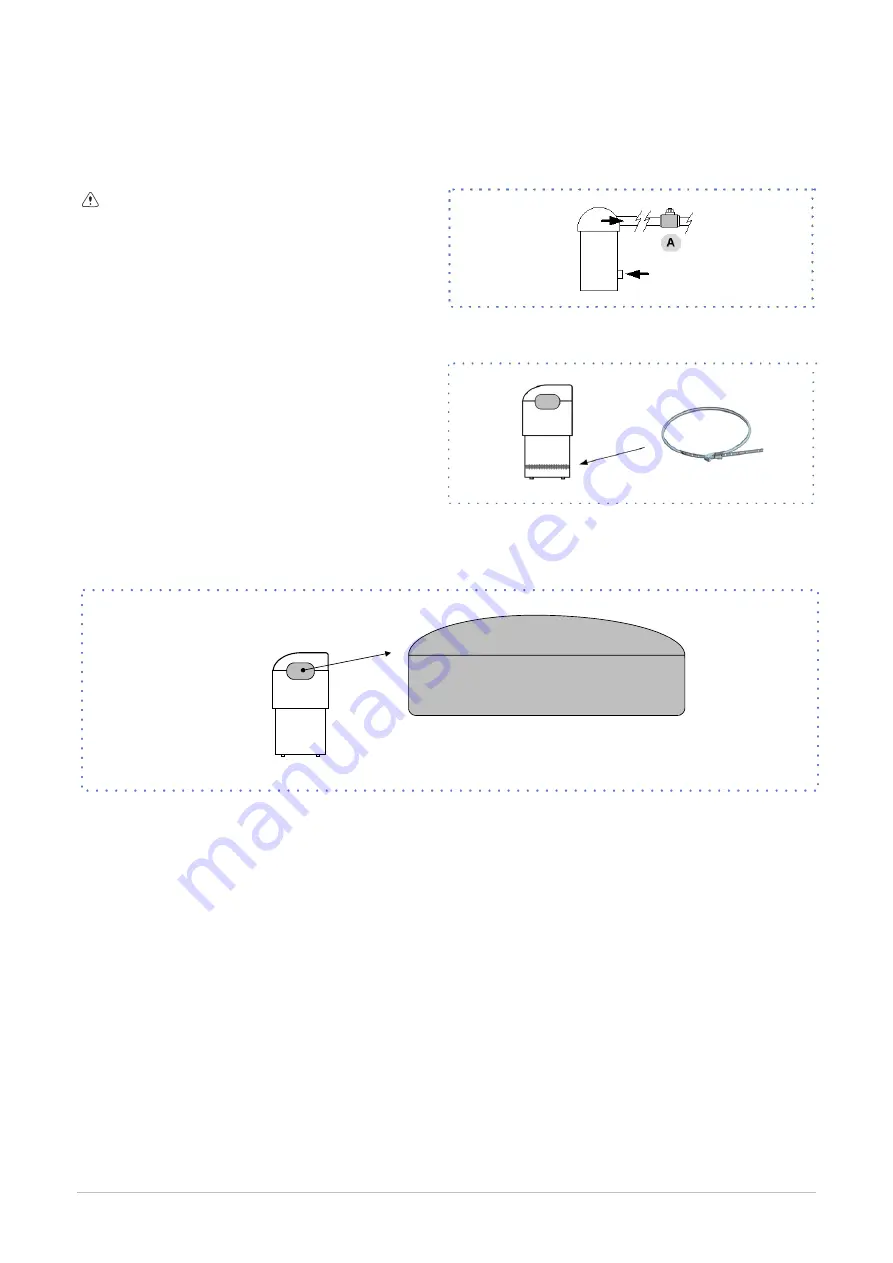
9.1
0
Compressor supply line shut-off valve
9.1
1
C
rankcase heather
Do not remove the seal
Remove only if authorized by the manufacturer.
Please contact the maker for informations.
Check:
•
closure
•
Operation
9.1
2
Copeland scroll compressor
Compressor may stop Pumping With Motor Running
Turn Off And Wait Until Cool
May need More Than 1 Hour To Reset
Advanced Scroll Temperature Protection
48
Summary of Contents for MSE-XSC3 100.4
Page 1: ...MSE XSC3 90 4 160 4 Installation and operating manual...
Page 3: ...Index of contents 1 4 2 6 3 8 4 10 5 14 6 18 7 26 8 35 9 47 10 52 11 53 12 54 57 3...
Page 19: ...Connections performed by the Customer 19...
Page 50: ...9 15 Compressor replacement 50...
Page 51: ...9 16 Exchanger replacement 51...