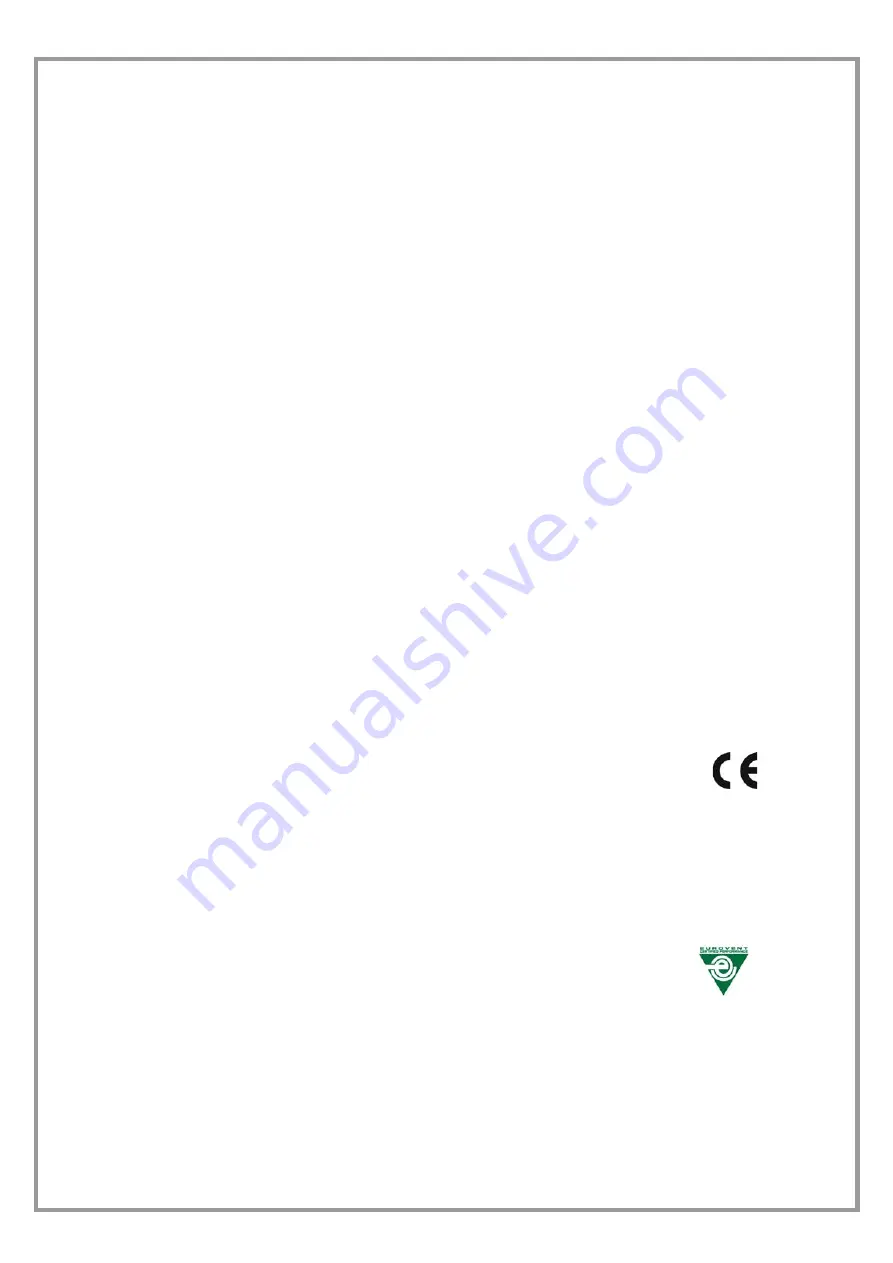
M03Q40G6-03 30/07/08
pag
8
GENERAL WARNINGS
MANUAL PURPOSE
This manual has been designed to enable the unit to be
installed, started up and maintained correctly.
MANUAL INSTRUCTIONS
It is essential to observe these instructions.
The manufacturer declines all liability for any damage that
may be caused whether directly or indirectly to persons or
things if these instructions are not heeded.
MANUAL STORE
This manual and the unit’s wiring diagram should be
carefully stored so that they are readily available to the
operator when required.
EXPERT PERSONAL
The unit must be installed, tested and maintained by expert
personal who meet the relevant legal requirements (Italian
law No. 46 of 5/3/1990).
LOCAL SAFET REGULATION INSTALLATION
The installation must be performed observing the local
safety regulations.
POWER SUPPLY
Make sure the power supply conforms to the data on the
unit’s rating plate, located inside the door of the main
electrical panel.
PACKAGING
The packaging material (plastic bags, polystyrene foam,
nails, etc.) is potentially dangerous and should therefore be
kept away from children and recycled in compliance with
the local regulations in force.
MAINTENANCE
Before performing any service operations, cut off the power.
Perform the operations in conformity with the local
regulations in force.
PERIODICAL INSPECTIONS
Perform periodical inspections to locate possible loosened
or broken parts. If the repairs are not performed, there will
be a higher risk for things and peoples to become damaged
and injured.
FAULT – POOR OPERATION
Switch off the unit in the event of faults or poor operation.
REPAIR
Only have repairs carried out by a service centre authorised
by the manufacturer, and insist on the use of original spare
parts only.
Failure to comply with the above may compromise the
safety of the unit.
MODIFICATIONS
The manufacturer will not accept any responsibility, and the
warranty will lapse, in the event of electric and/or
mechanical modifications. Any modification which is not
formally authorized, and which does not respect the
instructions given in this manual, will cause the warranty to
lapse.
INTENDED USE
The unit must only be used for the specific purpose it was
designed :
L'unità è destinata al raffreddamento/riscaldamento di
acqua o acqua glicolata per il condizionamento con i
limiti previsti dal bollettino tecnico e dal presente
manuale.
HEATING = only WSHH
Any use other than that specified does not imply any
commitment or constraint by the manufacturer in any way
whatsoever.
ADDITIONAL SAFETY PRECAUTIONS
This unit has been especially designed and manufactured
so to prevent any risk to persons and health hazard.
For this reason, design solutions fit to eliminate (where
possible) any cause of risk and sensibly reduce the
probability of danger have been adopted.
Please refer to the "Residual Risks" section of this manual
and strictly observe the behaviour prescriptions listed there
in order to prevent any possible risk that hasn’t been
possible to avoid in the design stage.
DATA UPDATING
The manufacturer may be able to modify the data without
prior notice as a consequence of constant improvements.
REGULATIONS AND
CERTIFICATIONS
UNI EN ISO 9001 CERTIFICATION
Clivet S.p.A., in order to guarantee customer satisfaction,
has chosen the ISO 9001 Quality System as the reference
for all its business activities. This is demonstrated by the
company’s commitment to ongoing improvements in the
quality and reliability of its products; its sales, design,
purchasing, production and after-sales service activities are
the means used to reach such purpose.
CE MARK
Clivet products bear the CE mark, in compliance with the
requirements of the following EC directives, including the
latest amendments, and with the corresponding national
approximated legislation:
•
- 98/37/CE
•
- 89/336/CEE as modified by the directives 92/31/CEE
and 93/68/CEE
•
- 73/23/CEE as modified by the directive 93/68/CEE
•
- 97/23/CE
EUROVENT
CERTIFICATION
Clivet is partecipating in the EUROVENT Certification
Programme "Liquid Chilling Packages". Products are listed
in the EUROVENT Directory of Certified Products and in the
site www.eurovent-certification.com. Eurovent Chillers
Certification Programme covers air cooled packaged
chillers up to 600 kW and water cooled packaged chillers up
to 1500 kW.