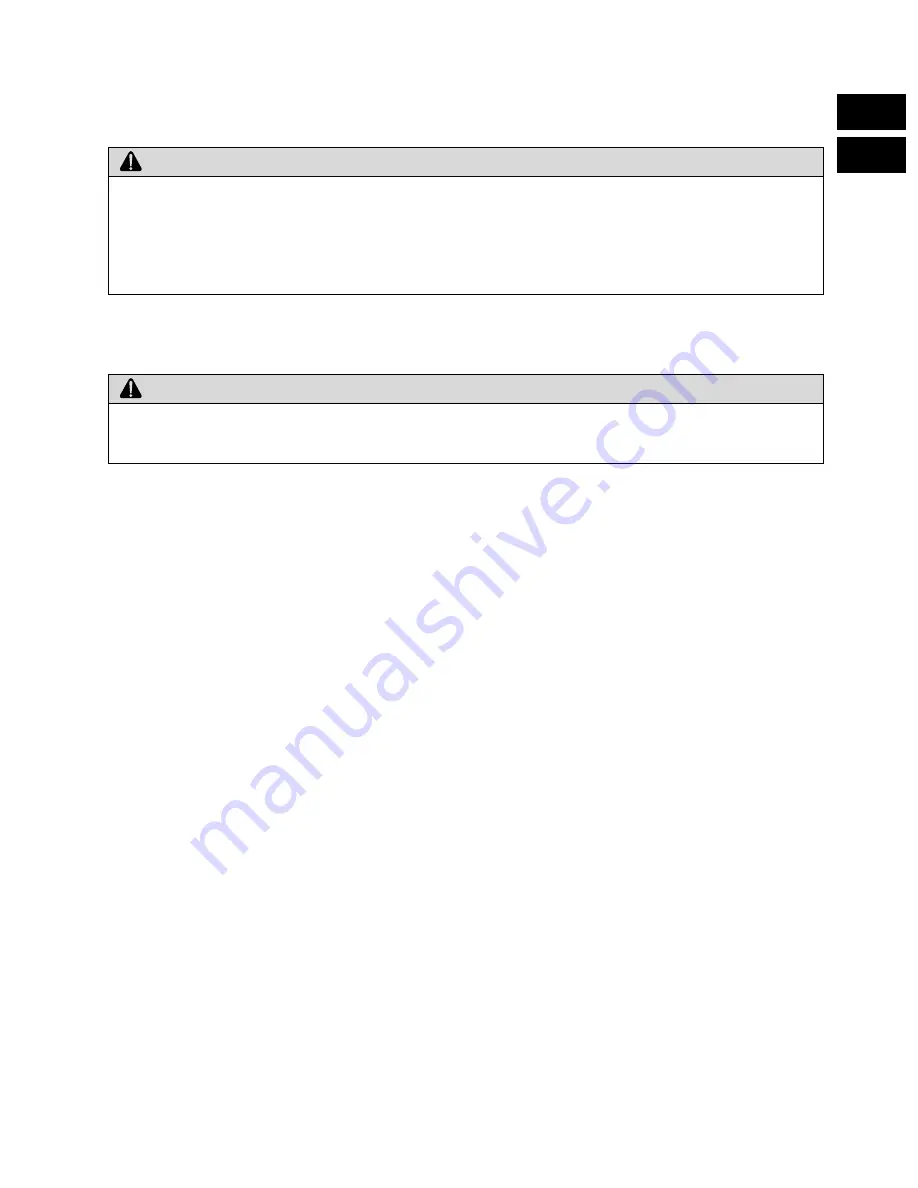
Page 21-43
E
21A
The energy displacement module is mounted on the vehicle frame, directly behind the batteries.
1. Raise the rear of the vehicle.
2. With the key switch ON and the forward and reverse rocker switch in FORWARD, slowly depress the
accelerator pedal halfway to the floor (the rear wheels will begin to turn). Hold the pedal in this position
and allow the vehicle to run for approximately one minute.
3. Release the accelerator pedal, turn the key switch OFF, and place the forward and reverse rocker
switch in NEUTRAL. Carefully check the energy displacement module for heat build-up by placing a
hand very close to, but not touching, the energy displacement module. If the module is warm or hot, the
dynamic braking solenoid is not functioning properly; replace the solenoid.
Test Procedure 30 - Energy Displacement Module Condition and 6 Gauge Green
Wire Continuity
1. Turn the key switch to OFF and place the forward and reverse switch in NEUTRAL. Disconnect the bat-
teries. Leave the Z plug connected to the controller.
2. Inspect the energy displacement module for a broken or cracked coil or loose connections at the
mounting plate.
3. Inspect the green wires from the resistor coil to the dynamic braking solenoid for loose connections,
signs of overheating, or broken or loose terminals ends.
4. Place the black (-) probe of a multimeter, set to ohms (
Ω
), on the large post of the dynamic braking
solenoid (with the 6 gauge green wire attached) and place the red (+) probe on the other end of the
green wire (at the energy displacement module). The reading should be continuity. If the reading is
incorrect, repair or replace the green wire (Figure 21-63).
5. Place the black (-) probe of a multimeter, set to ohms (
Ω
), on the other large post of the dynamic brak-
ing solenoid (with the other green wire attached) and place the red (+) probe on the other end of the
green wire (at the resistor coil terminal). The reading should be continuity. If the reading is incorrect,
repair or replace the green wire.
Test Procedure 31 - Battery Warning Light Circuit
1. Turn the key switch to OFF position and place the forward and reverse switch in Neutral. Disconnect Z
plug from controller; the battery wire will remain connected.
2. Disconnect the 18 gauge brown wire from the computer at the spade connector (See Figure 21-15,
Page 21-15).
3. Connect one end of a jumper wire to the male side of the spade connector, and connect the other end
of the jumper wire to the negative post of battery number 2. The light should illuminate. If it does not,
proceed to step 4.
• LIFT ONLY ONE END OF A VEHICLE AT A TIME. BEFORE LIFTING, LOCK THE BRAKES AND
CHOCK THE WHEELS THAT REMAIN ON THE FLOOR. USE A SUITABLE LIFTING DEVICE
(CHAIN HOIST OR HYDRAULIC FLOOR JACK) WITH 1000 LBS. (454 KG.) MINIMUM LIFTING
CAPACITY. DO NOT USE LIFTING DEVICE TO HOLD VEHICLE IN RAISED POSITION. ALWAYS
USE APPROVED JACKSTANDS OF PROPER WEIGHT CAPACITY TO SUPPORT THE VEHICLE.
• IF ALL ELECTRICAL COMPONENTS ARE FUNCTIONING PROPERLY, THE REAR WHEELS
WILL TURN WHEN THE ACCELERATOR PEDAL IS DEPRESSED.
WARNING
WARNING
Summary of Contents for 1996 DS Golf Car Gasoline
Page 2: ......
Page 28: ...Page 3 14 3 E G...
Page 38: ...Page 4 10 4 E G...
Page 76: ...Page 6 30 6 E G...
Page 110: ...Page 8 26 8 E G...
Page 136: ...Page 11 6 11 G...
Page 268: ...Page 15 4 15 G...
Page 286: ......
Page 316: ...Page 18 6 18 G...
Page 332: ...Page 19 16 19A E...
Page 350: ...Page 19 34 19A E...
Page 444: ......
Page 451: ...Page 21 59 E 21B FIGURE 21 85 2 4 5 7 8 1 9 6 5 4 3...
Page 452: ...Page 21 60 21A E...
Page 472: ...Page 22 20 22 E...
Page 524: ...Page 23 52 23A E...
Page 543: ......
Page 544: ...Golf Cars Club Car Inc P O Box 204658 Augusta GA 30917 4658...