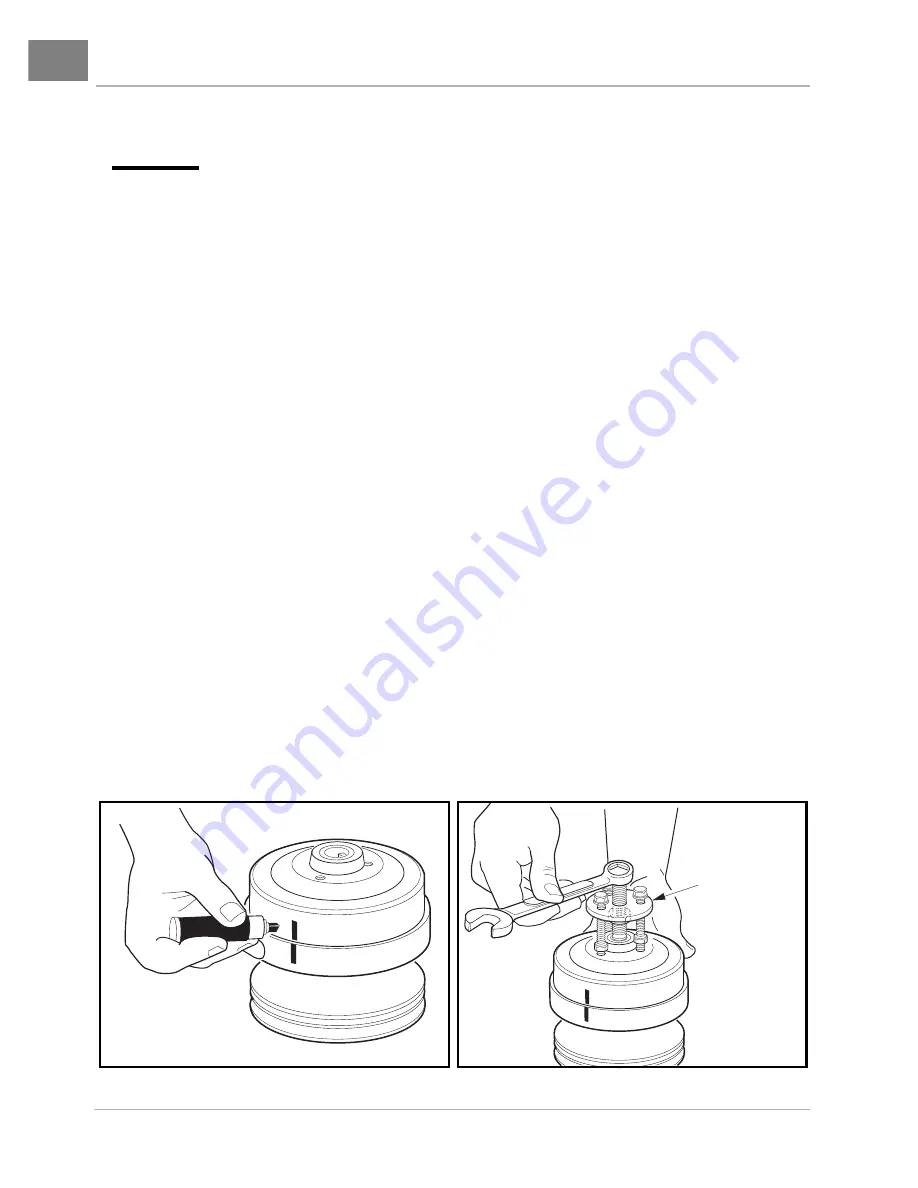
TORQUE CONVERTER
Drive Clutch
Page 17-6
2006-2010 Turf/Carryall 272/472 and XRT 1200/1200 SE Maintenance and Service Manual
17
DRIVE CLUTCH DISASSEMBLY
CAUT ION
• The drive clutch is balanced as an assembly. Before disassembly, make match marks on the
clutch cover and on the moveable face assembly so they can be reassembled in the same
positions (Figure 17-5, Page 17-6).
1. Make match marks on the clutch drive hub and on the moveable face casting
NOTE:
The following procedure applies to the Drive Clutch Hub Puller (CC P/N 1014497). Other types of
pullers may vary in operation and sequence of procedure.
2. Remove the clutch drive hub (8)
.
2.1. Remove the three plastic plugs (9) from the clutch puller attachment holes in the drive hub (8)
.
2.2. Thread the center bolt of the Drive Clutch Hub Puller (CC P/N 1014497) into clutch until the stop
nut touches the clutch hub or the bolt bottoms out, then back the bolt out one-half turn
NOTE:
The stop nut has been mechanically crimped and locked into position acting as an integrated
assembly with the bolt.
2.3. Thread the three small bolts of the puller into the puller attachment holes in the clutch. Tighten bolts
evenly, making sure the face of the puller plate is parallel to the clutch face
NOTE:
The nuts on each of the three, small puller bolts are mechanically crimped and locked into position.
2.4. Unscrew the hub puller center bolt from the clutch, forcing the stop nut up against the puller plate,
lifting the drive hub (8) from the fixed face shaft (2)
3. Remove the thrust washer (11) from the moveable face (13).
4. Remove the drive buttons.
4.1. Remove the screws, flat washers, drive button take-up spring, and drive buttons
Figure 17-5 Mark Clutch Cover
Figure 17-6 Remove Clutch Drive Hub
Mark the clutch
cover and its
corresponding
position on the
moveable casting.
DRIVE CLUTCH
HUB PULLER
TOOL
(CCI P/N 1014497)
Summary of Contents for CARRYALL 272
Page 2: ......
Page 14: ......
Page 18: ...1...
Page 52: ...5...
Page 90: ...6...
Page 110: ...7...
Page 112: ...8...
Page 128: ...10...
Page 170: ...11...
Page 224: ...13...
Page 284: ...16...
Page 302: ...17...
Page 308: ......
Page 309: ...Club Car R NOTES...
Page 310: ...Club Car R NOTES...
Page 311: ......