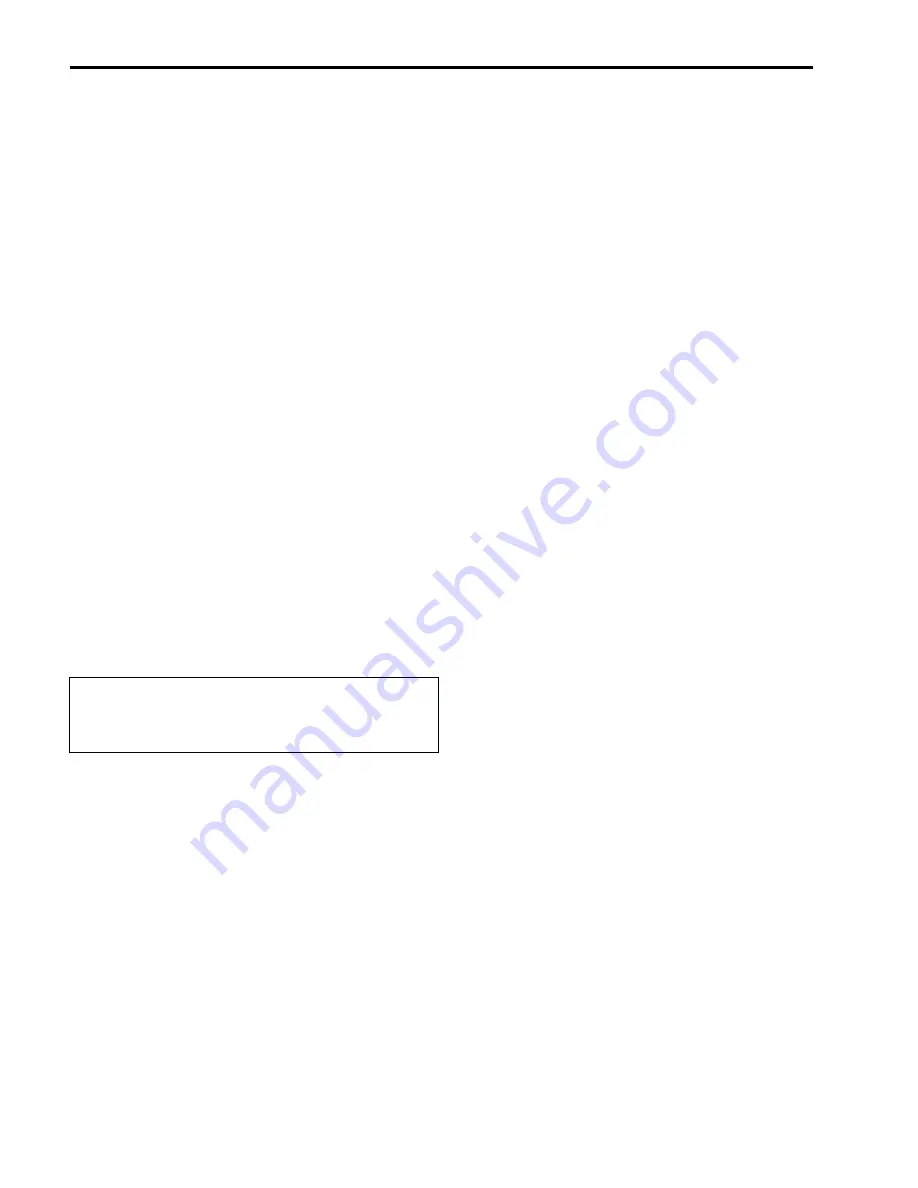
Chapter 6 - Parameter Description [FU2]
6-28
[P Control]
This is to compensate the error of a system
proportionally. This is used to make the controller
response fast for an error. When P control is used alone,
the system is easily affected by an external disturbance
during steady state.
[I Control]
This is to compensate the error of a system
integrally. This is used to compensate the steady state
error by accumulating them. Using this control alone
makes the system unstable.
[PI control]
This control is stable in many systems. If “D
control” is added, it becomes the 3
rd
order system. In some
systems this may lead to system instability.
[D Control]
Since the D control uses the variation ratio of
error, it has the merit of controlling the error before the
error is too large. The D control requires a large control
quantity at start, but has the tendency of increasing the
stability of the system. This control does not affect the
steady state error directly, but increases the system gain
because it has an attenuation effect on the system. As a
result, the differential control component has an effect on
decreasing the steady state error. Since the D control
operates on the error signal, it cannot be used alone.
Always use it with the P control or PI control.
Related Functions:
DRV-04 [Frequency Mode]
FU2-40 [Control Method]
I/O-01 ~ I/O-10 [Analog Signal Scaling]
EXT-15 ~ EXT-21 [Pulse Input Signals]
Summary of Contents for 30 HP30
Page 6: ......
Page 12: ......
Page 16: ...Chapter 1 Installation 1 4 BLANK ...
Page 18: ...Chapter 1 Installation 1 6 BLANK ...
Page 28: ...Chapter 1 Installation 1 16 Notes ...
Page 39: ...Chapter 2 Operation 2 11 Notes ...
Page 40: ......
Page 46: ......
Page 60: ...Chapter 4 Operation Examples 4 14 Notes ...
Page 83: ...Chapter 5 Parameter List 5 23 Notes ...
Page 84: ......
Page 92: ...Chapter 6 Parameter Description DRV 6 8 Notes ...
Page 105: ......
Page 106: ...Chapter 6 Parameter description FU1 6 14 Notes ...
Page 126: ...Chapter 6 Parameter Description FU2 6 34 Notes ...
Page 144: ...Chapter 6 Parameter Description I O 6 52 Notes ...
Page 162: ......
Page 188: ...Chapter 7 Options 7 26 Type 1 Max 400 Watt Type 2 Max 600 Watt A ...
Page 189: ...Chapter 7 Options 7 27 Type 3 ...
Page 194: ......
Page 204: ......
Page 210: ......