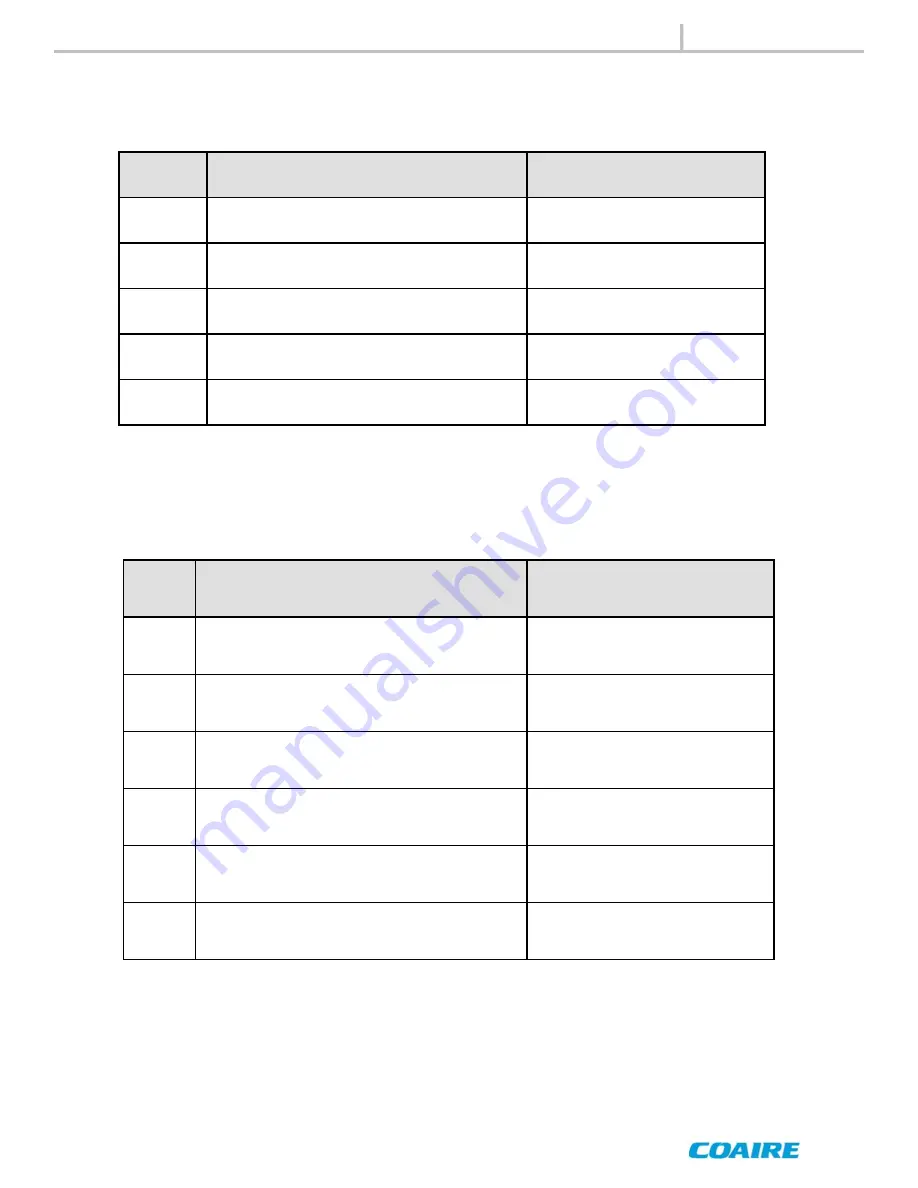
27
CONTROL
7-3-5 Digital Input Symbols
7-3-6 Digital Output Symbols
Symbol
Description
Remark
DI1
Over-load Main Motor #1
fault (open)
DI2
Over-load Main Motor #2
fault (open)
DI4
Emergency Switch
fault (open)
DI5
Remote Start/Stop Control
Run (closed)
DCM
INPUT
fault (open)
Symbol
Description
Description
N1
Compressor #1 Main Magnetic Contactor
On
N2
Compressor #2 Main Magnetic Contactor
On
NC1
N1, N2
N4
Run
On
N5
Alram
On
NC2
N4, N5