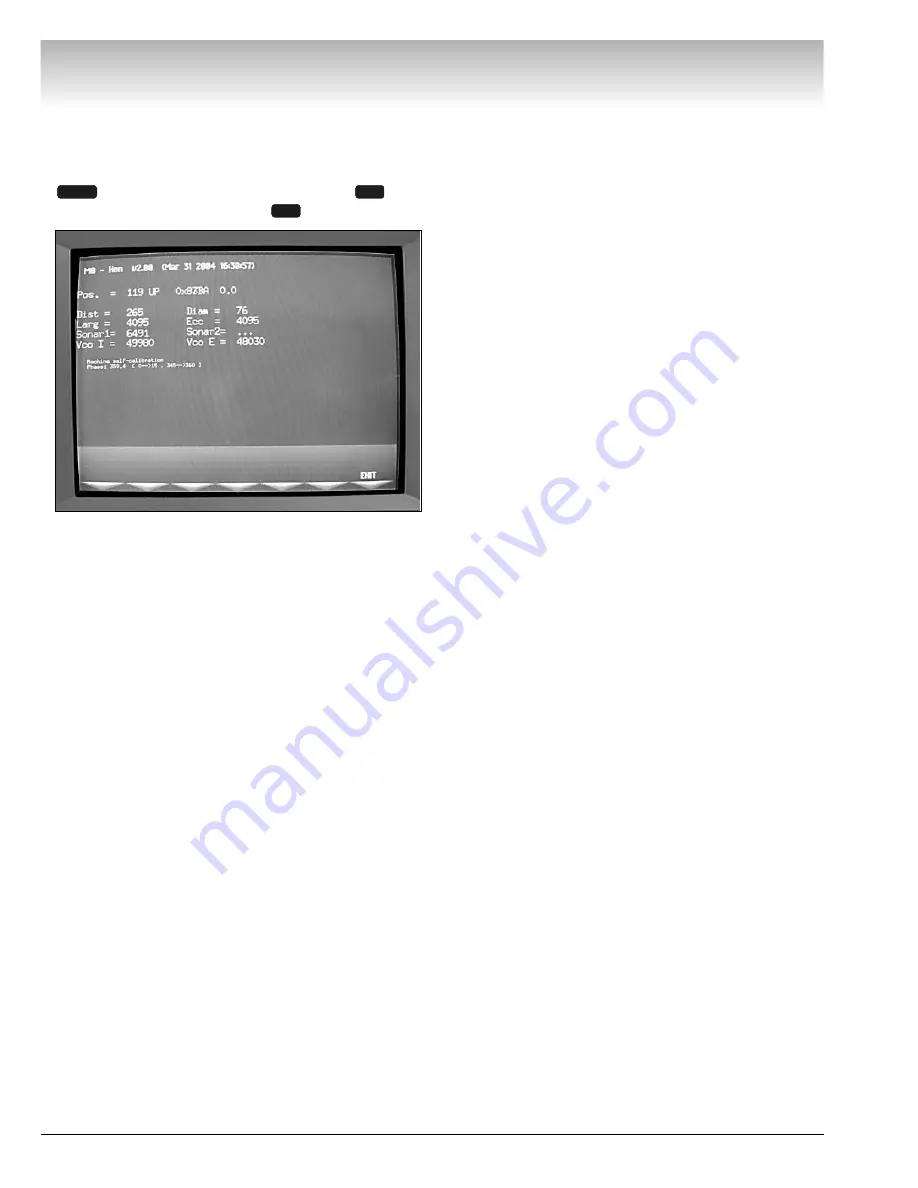
28 •
Important: Always read and follow the on-screen operating instructions.
V
Viid
de
eo
o B
Ba
alla
an
nc
ce
er
r
Machine Self-Test “Green Screen”
In the event of faulty wheel balancer operation, notify
a COATS
®
Service Technician of all the machine self
test readings. To view the self test screen, press the
key, select Special Functions option
, and
select Machine Self-Test option
.
Figure 45- Machine Self-Test Screen
A -
This line provides software version and other tech-
nical information.
B (Pos.) -
An encoder check. The word UP should
appear when rotated clockwise and DOWN when
rotated in the opposite direction.
C (Dist) -
Check for correct operation of the distance
arm gauge; the number increases when the gauge is
pulled out.
D (Sonar 1) -
If equipped, check of the hood width
sensor (option): the number decreases when a surface
is brought closer to the sensor device.
E (Vco I) -
Piezo Output.
F (Diam) -
Check for correct operation of the diame-
ter gauge; the number increases when the offset arm
is rotated outward.
G (Sonar 2) -
The reading should be 0.
H (Vco E) -
Piezo Output.
After Balance Vibration Problems
If vibration is still present after balancing the wheels
and driving the vehicle on smooth pavement, remove
the wheels and recheck the balance. If a wheel is out
of balance the cause maybe:
• Wheel was not mounted/centered correctly on the
balancer.
• A weight has come off the wheel (possibly the
wrong clip style). Remove the other weights from
the wheel and rebalance.
• Foreign material inside the tire. Remove the tire
from the wheel, remove the foreign material, and
remount. Remove wheel weights and rebalance
the wheel.
• Stones or other foreign objects caught in the tire
tread or rim. Remove the objects. Check and rebal-
ance if needed.
If the balancer still indicates the wheels are balanced
to within 0.05 ounces on both inner and outer displays,
the problem is not in the balance of the wheels. Check
the following possible sources of vibration:
• Tire pressure. Bring all tires up to the recom-
mended PSI.
• Radial or lateral runout in the tire or wheel. Replace
the damaged part.
• Unbalance in wheel covers or trim rings. Remove
the wheel covers or trim rings and test drive. If the
vibration is gone, remove the shaft and use an
appropriate adapter to mount the wheel to the bal-
ancer. Balance the wheel with the wheel cover or
trim ring attached to the wheel.
• Incorrectly mounted wheel. Remount correctly.
• Damaged wheel bolt holes. Replace wheel.
• Worn universal joints. Replace as required.
• Drive shaft unbalance or damaged. Balance, repair,
or replace.
• Unbalance in brake rotor(s) or drum(s).
• Suspension out of alignment. Align the vehicle and
replace any damaged or worn parts.
3
7
MENU