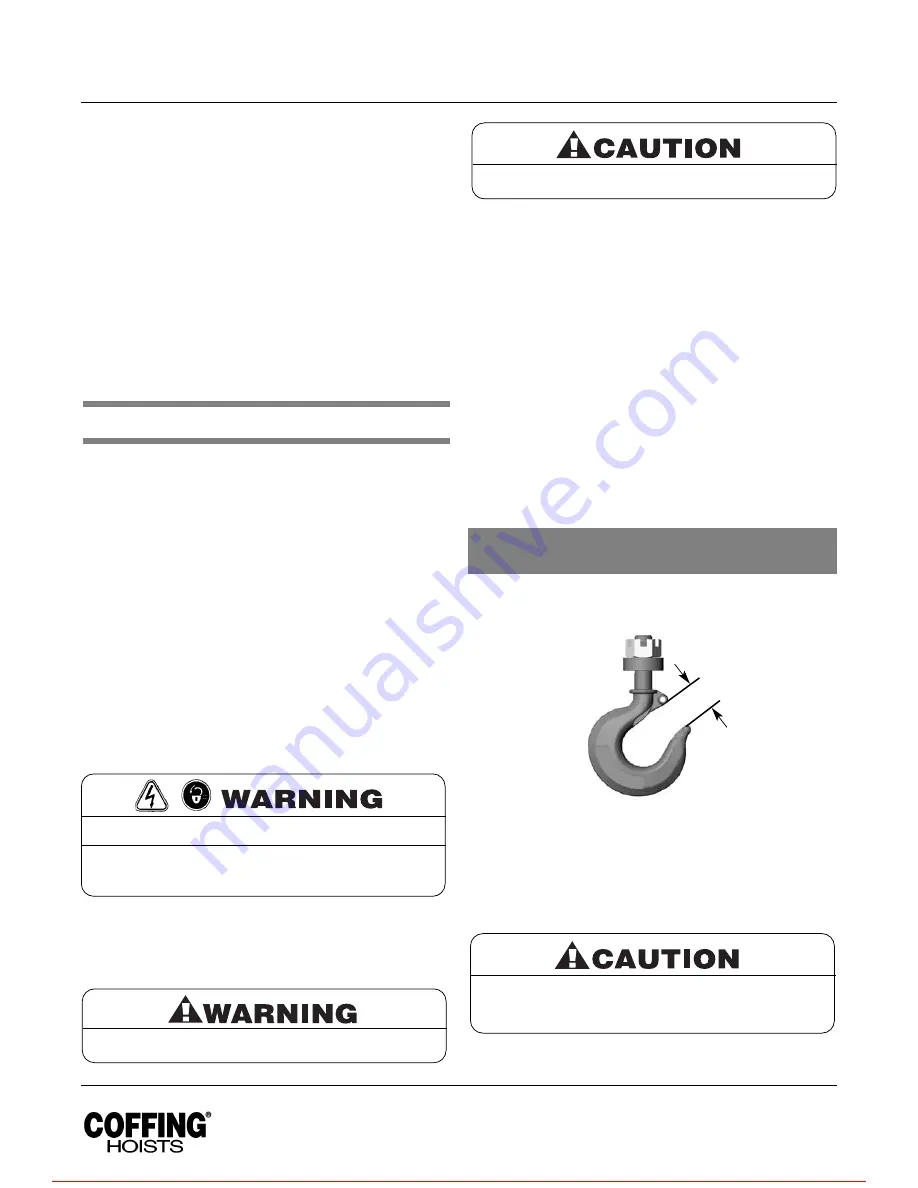
rigging before continuing to raise the load. Load must be
supported in saddle of hook, not by hook tip or hook latch.
5. Do not stand beneath a moving load! Do not move a load in
such a manner as to endanger personnel.
6. Do not lower into areas where visibility is obscured unless
someone else is guiding the operation.
7. Use common sense at all times when operating a lifting motor.
8. Do not operate if direction of hook travel is not the same as
indicated on button being pushed.
9. Do not operate unless hook travel limit devices function.
Test without load each shift.
10. Do not operate when lifting motor is not centered over load.
11. Do not operate if chain is not seated properly in sprockets
or sheave grooves.
12. Do not operate a damaged or malfunctioning lifting motor.
13. DO NOT USE LIFTING MOTOR TO LIFT, SUPPORT OR
OTHERWISE TRANSPORT PEOPLE.
MAINTENANCE
INSPECTIONS
A planned inspection routine should be established for this
lifting motor based upon frequency of use, severity of use, and
environmental conditions. Some inspections should be made
frequently (daily to monthly) and others periodically (monthly to
yearly). It is strongly recommended that an Inspection and
Maintenance Check List and an Inspector’s Report, similar to
those shown in Figures 8A and 8B, be used and filed for
reference. All inspections should be performed or overseen by
a designated inspector. Special inspections should be made
following any significant repairs or any operating occurrence
leading one to suspect that the lifting motor’s capability may
have been impaired.
LOWERING WITHOUT POWER
If the power fails with a load suspended, the lifting motor will
automatically stop. In an emergency the load can be lowered
without power as follows:
1. DISCONNECT LIFTING MOTOR FROM POWER SUPPLY
AND REMOVE ELECTRICAL COVER.
2. Open disc brake manually by using two screwdriver blades,
one on each side of the brake at a point close to the brake
spring posts. Apply pressure to the underside of the
armature plate (points “X”, Figure 4, page 9) to close the
solenoid and release the brake.
3. Use several quick releases instead of holding brake open
continuously. Do not exceed normal lowering speed.
HOOKS
Refer to Figure 2.
1. Inspect hooks once daily for cracking, extreme wear or
spreading. Replace hooks showing any of these signs. If the
throat openings are spread wider than the maximum
permissible 15% increase listed here, the hooks have been
overstressed and must be replaced. Any hook that is bent or
twisted more than 10° from the plane of an unbent hook
must also be replaced.
2. The hook latches should be inspected to ensure that they
close the hook throat opening in a secure manner when a
load is applied. Inspect the hook shank and nut for any
stripping of the threads or other damage. The hook nut should
be fully restrained by the retaining pin.
3. In addition to above, hooks should be inspected for cracks
by the magnetic particle, dye penetrant or other suitable
crack testing inspection method. This should be done at
least once a year.
1 Ton & Under
1
11
/
32
"
1
7
/
32
"
2 ton
1
11
/
32
"
1
11
/
32
"
(*) Maximum permissible throat opening of hook.
CHAIN
Chain is to be kept clean and lubricated (See LUBRICATION,
page 9). Visually check chain every time lifting motor is used.
The lifting motor must not be operated when chain is twisted or
kinked. An important phase of lifting motor maintenance is
chain inspection. Check individual links and check for chain
elongation.
6
Do not allow screw driver blades to touch rotating
friction disc “C” (See Figure 4, page 9).
Do not allow the load to descend rapidly. This causes
the motor to race and serious damage may result.
“X” Dimension*
Lifting Motor Load
Suspension
Capacity
Hook
Hook
The chain used on this lifting motor has very
carefully controlled dimensions and has been heat
treated. Do not attempt to substitute any other
manufacturer’s chain.
Failure to follow proper lockout/tagout procedures may
present the danger of electrical shock.
TO AVOID INJURY:
Disconnect power and lockout/tagout disconnecting
means before removing cover or servicing this
equipment.
Country Club Road
P.O. Box 779
Wadesboro, NC 28170 USA
TEL: (800) 477-5003
FAX: (800) 374-6853
X
Figure 2 — Hook
Inspection
For more information contact: Sievert Crane and Hoist, (708) 771-1600, parts@sievertelectric.com, www.sievertcrane.com