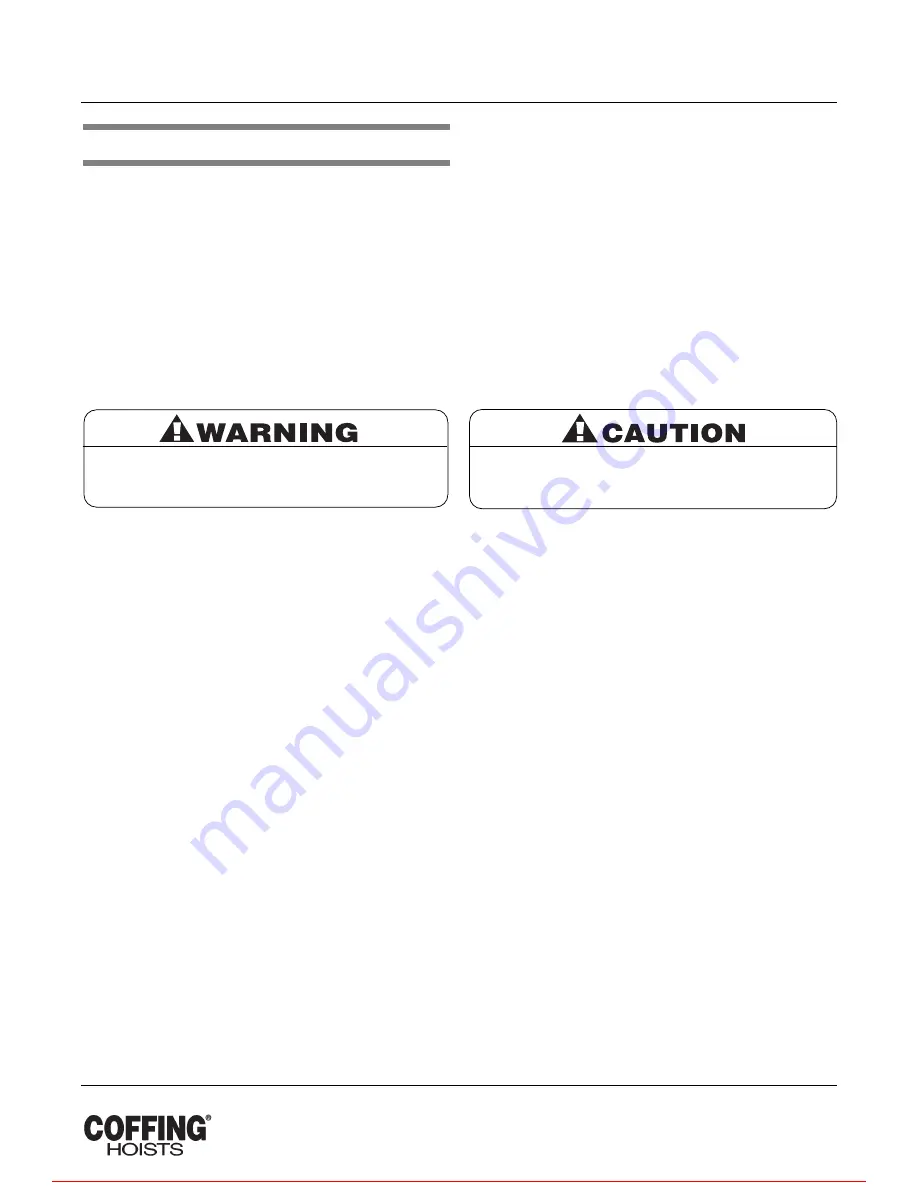
2
Country Club Road
P.O. Box 779
Wadesboro, NC 28170 USA
TEL: (800) 477-5003
FAX: (800) 374-6853
SAFETY PRECAUTIONS
Each Coffing JLC Series Electric Chain Hoist is built in
accordance with the specifications contained herein and at the
time of manufacture complies with our interpretation of applicable
sections of *American Society of Mechanical Engineers Code
(ASME) B30.16 “Overhead Hoists,” the National Electrical Code
(ANSI/NFPA 70) and the Occupational Safety and Health Act
(OSHA). Since OSHA states the National Electrical Code applies
to all electric hoists, installers are required to provide current
overload protection and grounding on the branch circuit section in
keeping with the code. Check each installation for compliance with
the application, operation and maintenance sections of these
articles.
*Copies of this standard can be obtained from ASME Order
Department, 22 Law Drive, PO Box 2300, Fairfield, NJ 07007-
2300, U.S.A., www.asme.org, 800-843-2763.
1.
NOT
operate a damaged, malfunctioning or unusually
performing hoist.
2.
NOT
operate the hoist until you have thoroughly read and
understood the manufacturer’s Operating and Maintenance
Instructions or Manuals.
3.
NOT
operate a hoist which has been modified without the
manufacturer’s approval or without certification that it is in
conformity with ANSI/ASME B30 volumes.
4.
NOT
lift more than rated load for the hoist.
5.
NOT
use hoist with twisted, kinked, damaged, or worn load
chain.
6.
NOT
use the hoist to lift, support, or transport people.
7.
NOT
lift loads over people.
8.
NOT
operate a hoist unless all persons are and remain clear
of the supported load.
9.
NOT
operate unless load is centered under hoist.
10.
NOT
attempt to lengthen the load chain or repair damaged
load chain.
11. Protect the hoist’s load chain from weld splatter or other
damaging contaminants.
12.
NOT
operate hoist when it is restricted from forming a
straight line from hook to hook in the direction of loading.
13.
NOT
use load chain as a sling, or wrap chain around load.
14.
NOT
apply the load to the tip of the hook or to the hook latch.
15.
NOT
apply load unless load chain is properly seated in the
chain sprocket(s).
16.
NOT
apply load if bearing prevents equal loading on all load
supporting chains.
17.
NOT
operate beyond the limits of the load chain travel.
18.
NOT
leave load supported by the hoist unattended unless
specific precautions have been taken.
19.
NOT
allow the load chain or hook to be used as an electrical
or welding ground.
20.
NOT
allow the load chain or hook to be touched by a live
welding electrode.
21.
NOT
remove or obscure the warnings on the hoist.
22.
NOT
operate a hoist on which the safety placards or decals
are missing or illegible.
23.
NOT
operate a hoist unless it has been securely attached to
a suitable support.
24.
NOT
operate a hoist unless load slings or other approved
single attachments are properly sized and seated in the hook
saddle.
25. Take up slack carefully - make sure load is balanced and load
holding action is secure before continuing.
26. Shut down a hoist that malfunctions or performs unusually
and report such malfunction.
27. Make sure hoist limit switches function properly.
28. Warn personnel of an approaching load.
1. Maintain firm footing or be otherwise secured when operating
the hoist.
2. Check brake function by tensioning the hoist prior to each
lift operation.
3. Use hook latches. Latches are to retain slings, chains, etc.
under slack conditions only.
4. Make sure the hook latches are closed and not supporting
any parts of the load.
5. Make sure the load is free to move and will clear all
obstructions.
6. Avoid swinging the load or hook.
7. Make sure hook travel is in the same direction as shown on
the controls.
8. Inspect the hoist regularly, replace damaged or worn parts,
and keep appropriate records of maintenance.
9. Use Coffing Hoists recommended parts when repairing the
unit.
10. Lubricate load chain per hoist manufacturer’s
recommendations.
11.
NOT
use the hoist’s overload limiting clutch to measure load.
12.
NOT
use limit switches as routine operating stops. They are
emergency devices only.
13.
NOT
allow your attention to be diverted from operating
the hoist.
14.
NOT
allow the hoist to be subjected to sharp contact with
other hoists, structures, or objects through misuse.
15.
NOT
adjust or repair the hoist unless qualified to perform
such adjustments or repairs.
Improper operation of a hoist can create a potentially
hazardous situation which, if not avoided, could result
in death or serious injury. To avoid such a potentially
hazardous situation, THE OPERATOR SHALL:
Improper operation of a hoist can create a potentially
hazardous situation which, if not avoided, could result
in minor or moderate injury. To avoid such a potentially
hazardous situation, THE OPERATOR SHALL:
For more information contact: Sievert Crane and Hoist, (708) 771-1600, parts@sievertelectric.com, www.sievertcrane.com