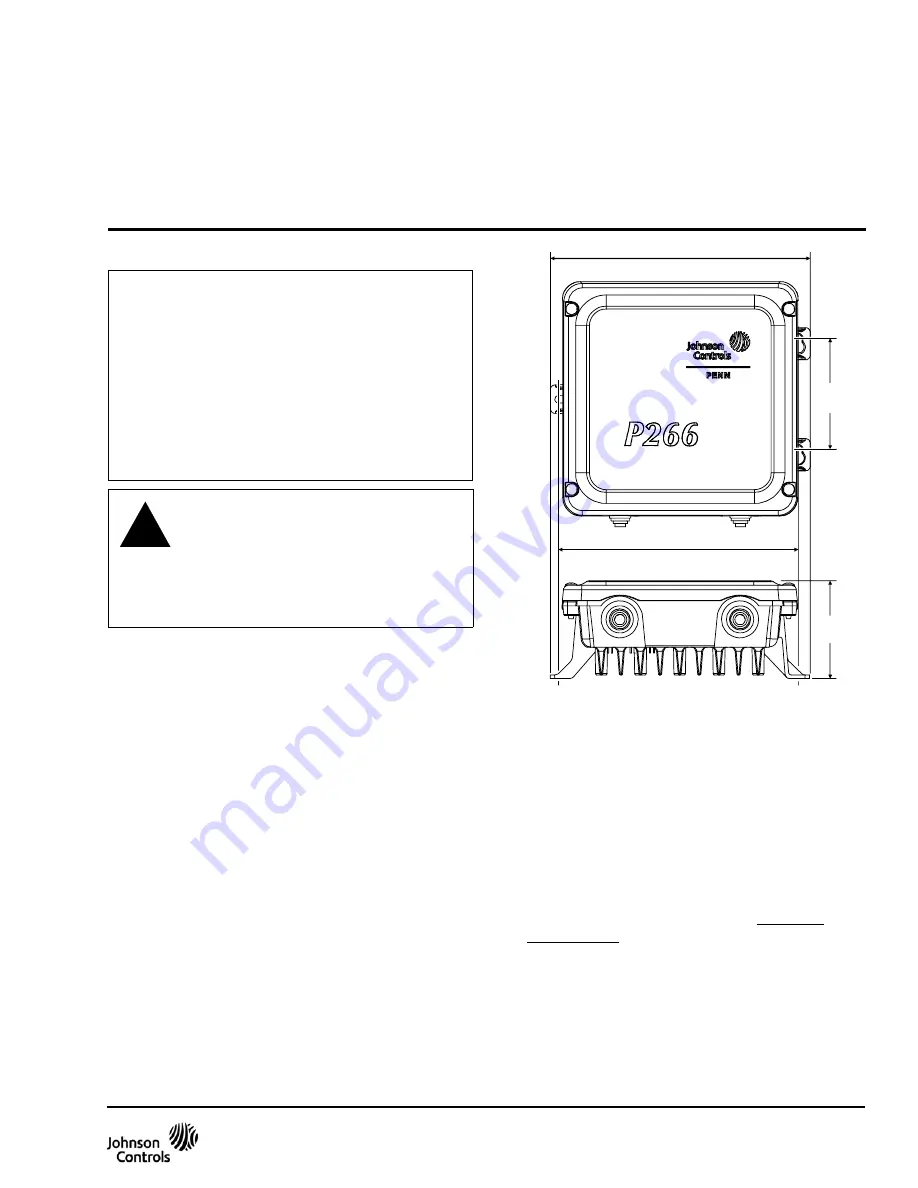
P266 Series Single-Phase Condenser Fan Speed Control Installation Instructions
1
Application
The P266 Single-Phase Condenser Fan Speed Control
is a cost-effective, compact, weather-resistant, and
durable speed control for single-phase, PSC motors
used in a wide variety of low-ambient refrigeration and
air conditioning condenser applications.
The P266 fan speed controls are designed to replace
the Johnson Controls® P66 Series and P215 Series
Fan Speed Controls and provide additional features
and application flexibility.
Mounting
Location and Mounting Considerations
Observe these guidelines when locating and mounting
a P266 fan speed control:
•
Ensure that the mounting surface and mounting
hardware can support the control and wiring.
•
Mount the P266 control upright on a vertical
surface with the heat sink fins oriented vertically
and the conduit/electrical holes facing down.
•
Ensure that air can flow through the heat sink fins
and provide 10 cm (4 in.) minimum clearance
around the heat sink.
•
Mount the P266 control in a location away from
sources of excessive heat and within the specified
ambient operating conditions. See
Technical
Specifications
for ambient operating conditions.
IMPORTANT:
Use this P266 Single-Phase
Condenser Fan Speed Control only as an operating
control. Where failure or malfunction of the P266 fan
speed control could lead to personal injury or
property damage to the controlled equipment or
other property, additional precautions must be
designed into the control system. Incorporate and
maintain other devices, such as supervisory or
alarm systems or safety or limit controls, intended to
warn of or protect against failure or malfunction of
the P266 fan speed control.
!
CAUTION: Risk of Property Damage
Use only single-phase Permanent Split
Capacitor (PSC) motors approved by the
manufacturer for speed control
application with the P266 control. Failure
to use a single-phase PSC motor may
damage the motor and other property.
Figure 1: P266 Single-Phase Condenser
Fan Speed Control Mounting Dimensions
165
(6-1/2)
178
(7)
76
(3)
66
(2-5/8)
F
IG
:p2
66_
di
m
s
P266 Series Single-Phase Condenser Fan Speed Control
Installation Instructions
P266xxx-x
Part No. 24-7664-2705, Rev. B
Issued April 29, 2009
Supersedes January 21, 2009
Summary of Contents for ACWC-180-EM-DR-LT-0-5
Page 35: ...Notes...