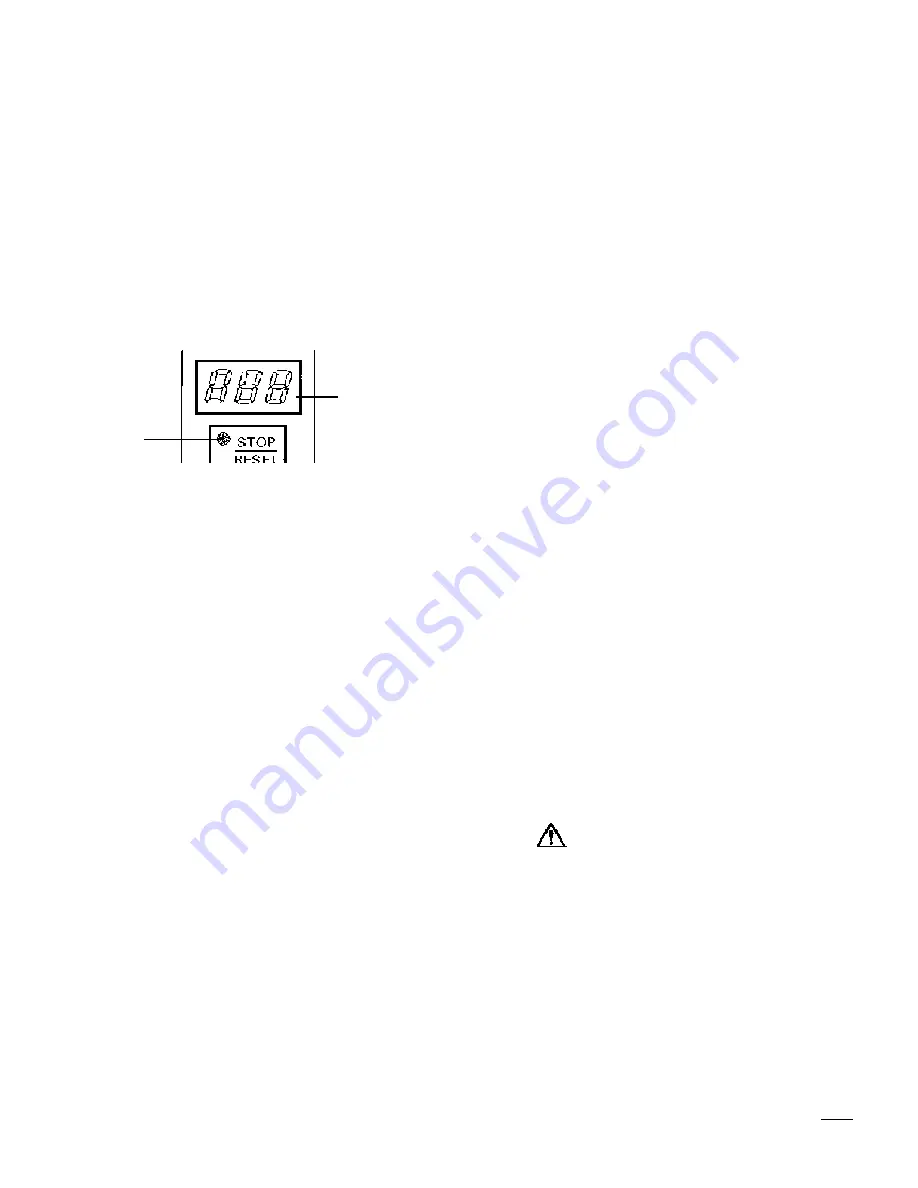
27
PART X
MAINTENANCE
Your COLDELITE machine has been designed, engineered and
manufactured to achieve high performance and long durability.
The life expectancy of a machine, any machine, does not depend
only on the quality of its components and design, but also on the
beneficial effects of basic maintenance procedures.
It is important to you, therefore, to become familiar with a few of
these basic procedures:
1) Remove O-rings only with the O-ring extractor supplied with
the machine.
2) Clean the machine according to the instructions.
3) Lubricate all O-rings and seals, as instructed.
4) The wearing or the improper cleaning of the beater shaft
seals, will result in leakage from the rear. Check the drip
chute pans frequently and replace seals, when so necessary.
5) Replace any O-ring that has a nick in it. If not replaced, it will
leak and interfere with the proper performance of the machine.
6) When all the spare parts supplied with the machine are used,
re-order immediately. Do not wait until the part is required
again.
7) NEVER use the AUTO position for washing, sanitizing and
initially filling the freezing cylinder.
8) IMPORTANT - During the washing and sanitizing period, run
the machine only for the time strictly necessary for this
operation. Prolonged use of the beater in the Cleaning
position may cause severe damage to the machine.
9) Always wash metal, plastic or rubber parts in lukewarm
water. NEVER, NEVER USE HOT WATER!
Important
If your Model is an air cooled machine, its efficiency depends on
the air cooled condenser. The fins of the condenser must be
cleaned every two or three months to assure efficiency.
Warning
Extreme care must be taken when removing side, rear or control
box panels.
Always turn the Selector Switch to the OFF position. Also, turn off
the Disconnect Switch on the electrical supply line before
exposing any electrical connections and/or moving parts, such
as belts, pulleys, fan blades and beater.
L1
570
A series of messages are available for interactive use of the
machine.
Message
When it appearsMeaning
- P_A
- Automatic /Stand-By
-Thermal sensor out
of order
- ICE
- Automatic
-Cylinder
temperature too low
- rtA
- At any time
- Overload relay
- 888
- At any time
- EPRON out of order
- MIP
- At any time
- Spigot head not
properly fixed;
thermal sensor out
of order
See page 28 for suggested remedy.
Power failure
In the event of a temporary power failure, when power supply
resets, the machine turns itself back to the same function before
power failure.
Power ON
When the machine is connected to the power supply, all leds and
displays illuminate on for 1 sec. to make a self test; just after, the
display shows for 2 seconds, 3 numbers corresponding to
thousands of cones extracted and then the display shows, for 2
seconds, other 3 numbers corresponding to the number of cones
extracted.
If you wish to Reset the number of cones, disconnect the machine
from the circuit breaker supply, push Stop and then turn ON the
Main circuit breaker while pushing Stop for the whole period of
display test.
D) PROXIMITY SWITCH
The sensitivity can be adjusted with a small screwdriver. The
trimmer rotation is limited to 270 degrees by a “stop”. When
adjusting towards “maximum” or “minimum”, be careful not to
exert excessive torque (max. 40 Nmm) against the “stop”.
Failure to do so would damage the trimmer permanently.
Adjusting Proximity Switch
The proximity switch pos. 152 been preset at the factory and its
range is 9 inches approx.
If modification is required, contact authorized service agency as
this operation must be carried out by specialized technicians.
Messages visible on the Monitor