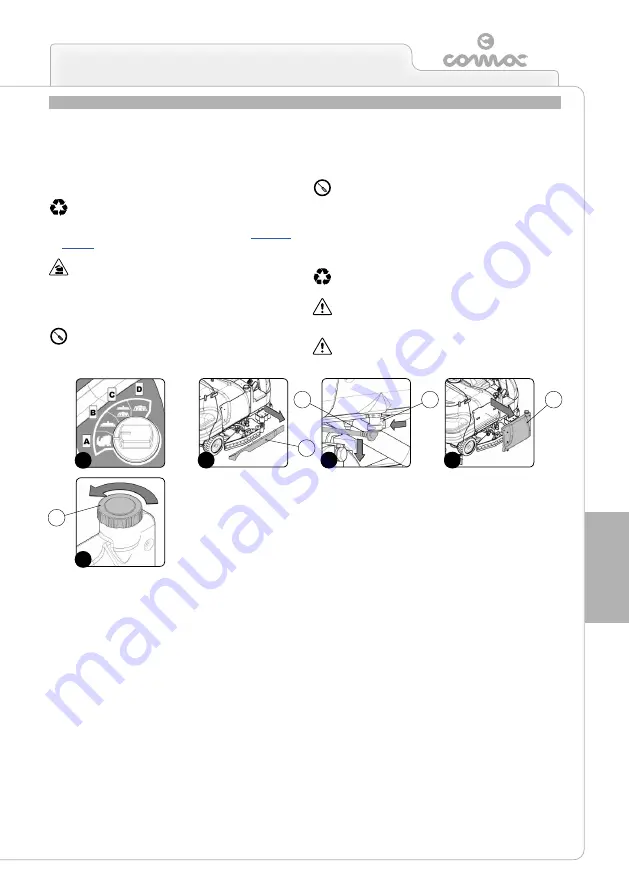
57
MAINTENANCE
Careful cleaning of the detergent canister guarantees better
efficiency of the machine water system, and therefore better
efficiency when cleaning the floor. To clean the detergent canister,
proceed as follows:
1. Select the i-drive program “transport” by rotating the knob to
position “A” as shown in (
Fig.1
).
2. Take the machine to the maintenance area.
ATTENTION:
the place designated for this operation must
comply with current environmental protection regulations.
3. Make sure the machine is in a safe condition (read “
ATTENTION:
protective gloves should always be worn when
handling detergents or acidic or alkaline solutions, to avoid
serious injury to the hands.
4. Remove the right-hand carter (1) from the machine (
Fig.2
), after
removing the nuts that fix it to the frame.
ATTENTION:
the equipment to be used for this operation is
not supplied with the machine.
CLEANING THE DETERGENT TANK (VERSIONS WITH CDS)
5. Disconnect the quick-connection rubber-holder (2) (located
behind the side carter) (
Fig.3
), to avoid any risk of it breaking
(CDS versions). Before pulling out the rubber-holder (2), press
the lever (3) in the female connection (
Fig.3
).
6. Remove the detergent tank (4) from the machine, after removing
the nuts that fix it to the frame (
Fig.4
).
ATTENTION:
the equipment to be used for this operation is
not supplied with the machine.
7. Remove the cap (5) of the detergent canister (
Fig.5
).
8. Remove any detergent residue.
9. Rinse the inside of the canister with a jet of running water.
10. Repeat the operations in reverse order to reassemble all the
parts.
ATTENTION:
the place designated for this operation must
comply with current environmental protection regulations.
ATTENTION:
be sure to respect current environmental
protection regulations, and never discharge the detergent
directly into the drain.
ATTENTION:
fill with clean water, at a temperature no greater
than 50°C and no less than 10°C.
1
5
4
2
3
1
5
2
3
4
Summary of Contents for ULTRA 120 B-G
Page 2: ......
Page 7: ...7 36 72 102 6 9 10 110 107 106 75 5 76 74 58 7 59 7...
Page 9: ...9 103 4 56 31 43 109 15 3 98 22 65 24 108 19 34 35 23 68 44 63 64 99...
Page 10: ...10 2 94 17 101 96 105 69 12 11 18 73 40 97 95 104 42...
Page 68: ...68 NOTES...
Page 69: ...69 NOTES...
Page 70: ...70 NOTES...
Page 71: ......