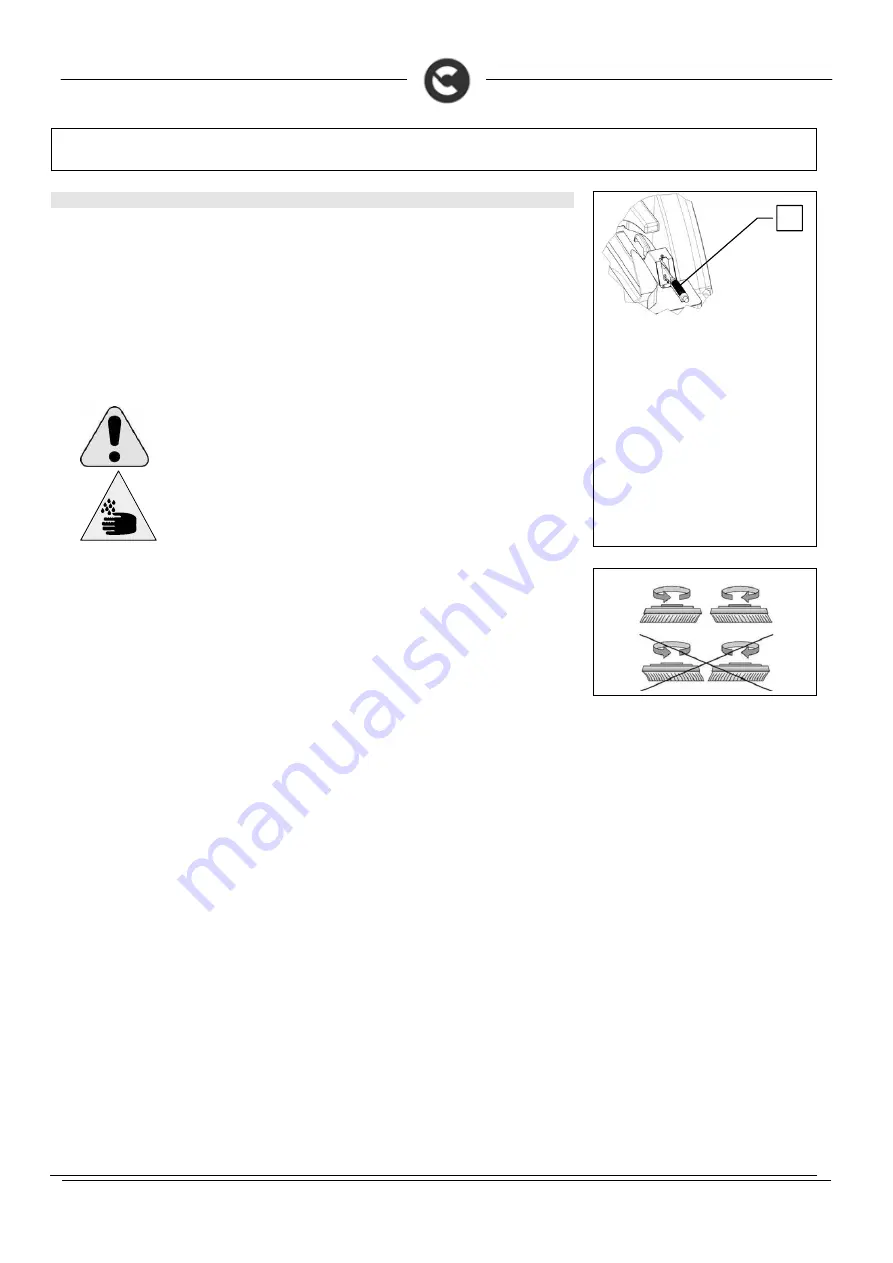
38
DAILY MAINTENANCE
40. DISC BRUSH DISASSEMBLY
To remove the brushes proceed as follows:
1.
Connect the electrical system connector to the battery connector
2.
Turn the key switch to the “1” position
3.
Lift the brush head unit by operating the knob (1), if it is not already raised
4.
Turn the key switch to the “0” position and remove the key from the instrument panel
5.
Engage the parking brake (2)
6.
Disconnect the electrical connector from the battery connector
7.
Rotate the brush anticlockwise until it comes out of the brush-holder plate seat, as shown in the
figure.
The photo shows the direction of rotation for releasing the right brush. Rotate in the opposite direction
for the left brush.
WARNING: Before performing any maintenance, remove the keys from the
panel and disconnect the battery connector of the machine.
WARNING: This operation must be carried out using gloves to protect against
contact with dangerous solutions.
You are advised to invert the right and left-hand brushes every day. If the brushes are not new however,
and have deformed bristles, it is better to reassemble them in the same position (the right-hand one on the
right, and the left-hand one on the left), to prevent the different inclination of the bristles producing an
overload on the brush motor as well as excessive vibrations.
2