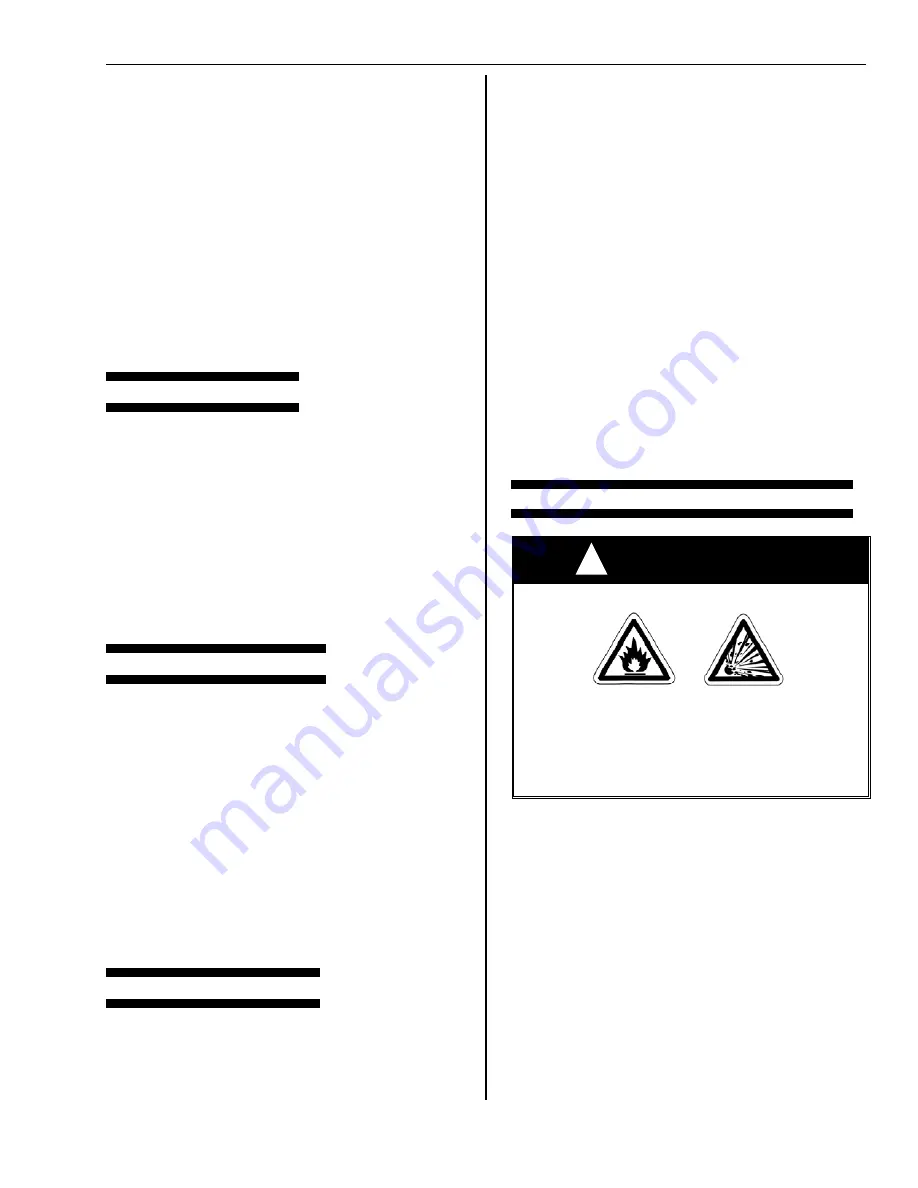
Reflect-O-Ray
®
Oil Fired EDS 3.5
Installation, Operation & Service
Combustion Research Corporation
Page 39
Regular preventive maintenance is important in
applications that place a heavy load on system controls,
such as in the commercial cooking and agricultural and
industrial industries because:
1. In applications where the equipment operates 100,000-
200,000 cycles per year. Such heavy cycling can wear
out the oil controls in one to two years.
2. Exposure to water, dirt, chemicals, and heat can
damage the oil control and shut down the control
system.
The Oil control Components should be
replaced if
:
1. It does not perform properly on checkout or trouble-
shooting.
2. The oil control is likely to have operated for more than
200,000 cycles.
CLEANING OF SYSTEM
Periodic cleaning of the reflectors can be done with a mild
soap and water solution. Wipe excess dirt and grim off the
top and underside of the reflectors which may have
collected.
Burner assembly may also be cleaned in the same
manner.
Do not attempt to operate system for one (1) hour after
any cleaning process which may have included water.
In the unlikely event the radiant tube system requires
internal cleaning a 3.5" round brush assembly must be
used. Contact your representative or the factory for
guidance in obtaining this brush and the appropriate
method for cleaning.
MAINTENANCE PROGRAM
The maintenance program should include a regular check
out of the oil control. Maintenance frequency must be
determined individually for each application. Some
considerations are:
1.
Cycling frequency.
Appliances that may cycle
100,000 times annually should be checked monthly.
2.
Intermittent use.
Appliances that are used seasonally
should be checked before shutdown and again before
the next use.
3.
Consequence of unexpected shutdown
.
Where the
cost of an unexpected shutdown would be high, the
system should be checked more often.
4.
Dusty, wet or corrosive environment.
Since these
environments can cause the oil control to deteriorate
more rapidly, the system should be checked more
often.
CHECKOUT PROCEDURE:
Before leaving installation, several complete operating
cycles should be observed to see that all components are
functioning properly.
1. Before turning on the main electrical power switch, be
sure all oil supply lines are purged of air.
2. Turn on main electrical power switch and close
thermostat contacts.
3. After the control is powered it will automatically
energize the spark and the oil valve.
4. The Cad Cell detects the presence of the flame and
the control de-energizes the spark and the valve will
remain open. Check valve outlet and other
downstream pipe connections for fuel oil leaks.
5. Turn the thermostat to a low dial setting to open
contacts. The main flame should be extinguished.
6. For 100% shutoff check, set thermostat to low dial
setting (system off). Disconnect sensing probe lead at
control terminal.
7. Turn thermostat to a high dial setting to energize spark
ignition and valve. The oil should ignite. After 30
seconds, the system should "lockout" and burner
functions are off (no oil flow, no spark). If the system
does not go into "lockout," follow the installation
instructions to replace the control. Repeat the 100%
shutoff check. Note blower will not shut down when
ignition "lockout" occurs.
8. Set thermostat again to a low dial setting (system off),
connect probe lead to control terminal. Set thermostat
to normal setting to put system back in service.
CHECK SAFETY SHUTDOWN PERFORMANCE:
WARNING
FIRE OR EXPLOSION HAZARD
IMPROPER INSTALLATION, ADJUSTMENT,
ALTERATION, SERVICE OR MAINTENANCE
CAN CAUSE DEATH, SEVERE INJURY
AND/OR PROPERTY DAMAGE.
Perform the safety shutdown test anytime work is done
on a system
.
NOTE:
Read steps 1-7 below before starting safety
shutdown or safety lockout tests for the ignition
module.
1. Turn oil supply off at the burner assembly.
2. Set the thermostat or controller above room
temperature to call for heat.
3. Watch for ignition spark immediately or following pre-
purge. See DI module specifications.
4. Time length of ignition operation. See DI module
specifications.
5. After the module locks out, open fusible link valve on
the burner and ensure there is no oil flow to main
burner.
6. Set the thermostat below room temperature and wait
one minute.
7. Reset the burner and operate system through one
complete cycle to ensure all controls operate properly.
!