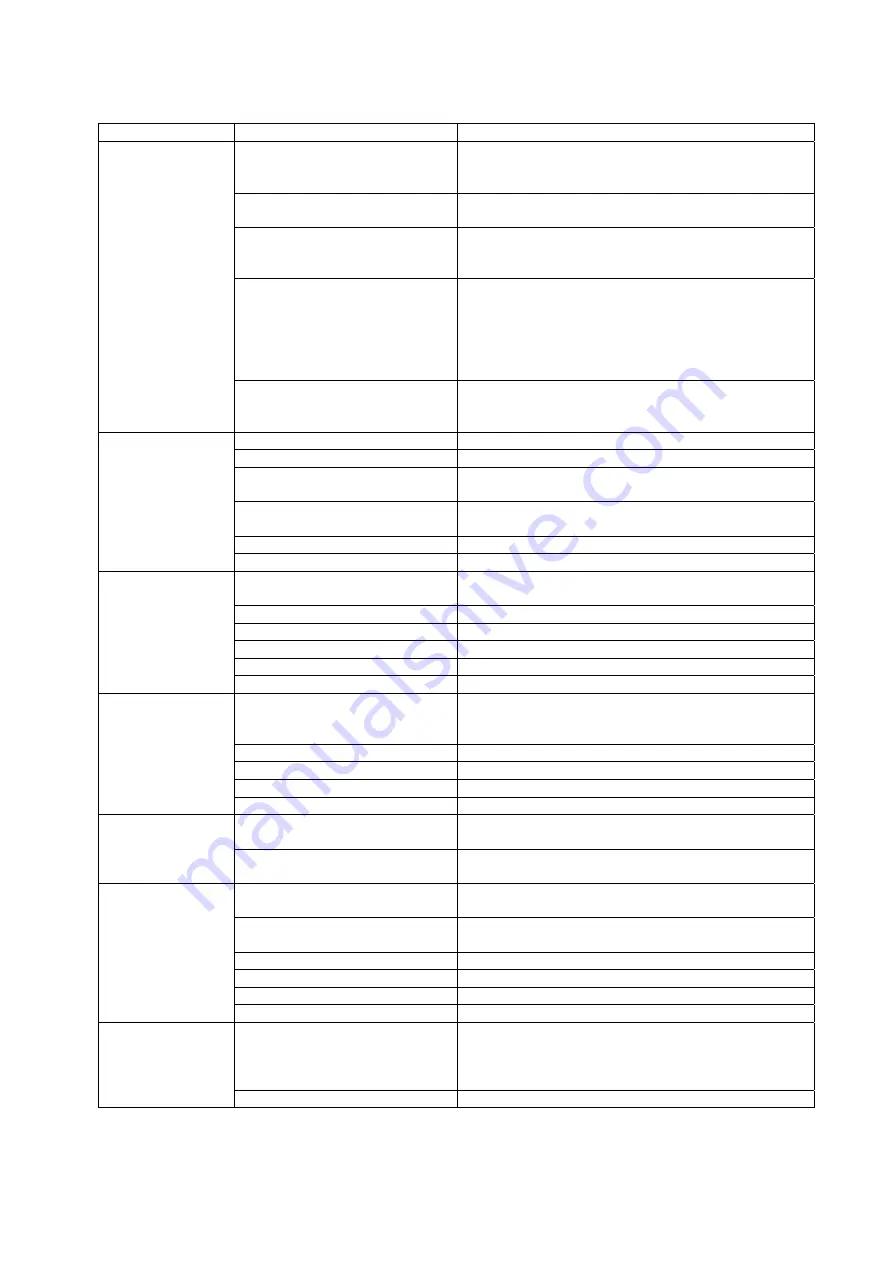
CompAir UK Ltd
PUBLICATION 98407/1050
Page 37
Fault
Probable Cause
Recommendation(s)
Faulty suction or delivery
valve(s).
Service valve(s) as necessary.
NOTE: A faulty suction valve gives excess
pressure in previous stage.
Pressure gauge inaccurate.
Check gauge against instrument of known
accuracy.
Pipeline restriction.
Existing Installation:
Check functioning and setting of all control valves.
Clean pipeline filters and service elements.
New Installation:
Ensure all protective plugs are removed from ports
and control valves are set correctly.
Check pipework is of adequate dimensions with
minimum of bends. Check joint gaskets for correct
positioning and size.
EXCESSIVE
PRESSURE
Final delivery pressure control
fault or pressure switch fault.
Automatic Control:
Inspect control equipment for malfunction, rectify
as necessary.
Blocked suction filter.
Remove and service.
First stage suction valve fault.
Remove, examine and rectify/replace.
Air leakage from machine /
system.
Locate and rectify.
Check drain valves are closed.
Wear.
If general wear is suspected, strip machine,
examine components and renew as necessary.
Loss of drive.
Check vee-belt drive and tension.
INSUFFICIENT
PRESSURE OR
VOLUME
Excessive blowby.
Check piston rings.
Operating above maximum
recommended duty.
Reduce operating duty.
Insufficient cooling air.
Check location and area ventilation.
Reduced cooling efficiency.
Examine cooler(s) for partial blockage.
Cooling fan clogged.
Clean fan.
Cylinder fins clogged or dirty.
Clean cylinder fins.
OVERHEATING
Wrong rotation.
Reconnect electrical supply to give correct rotation.
Machine or pipework system
vibration.
Examine machine seating, tighten mounting bolts.
Check pipework system is firmly secured. Check
clearances and tension of vee-belts.
Oil level low.
Refill to correct level.
Pulley loose.
Tighten pulley.
Belt drive worn.
Replace belts.
EXCESSIVE
NOISE
Worn bearings.
Remove from bearing housings and replace.
Speed too low.
Check motor speed.
Check vee-belt drive tension.
EXTENDED
RUNNING
Air leak on machine or
pipework.
Locate and rectify.
Excessive speed and / or
pressure.
Operate within specified limits.
Dirty air and / or suction
pipeline.
Examine filters and renew elements. Clean out
suction pipeline.
Incorrect lubricant.
Change to correct lubricant.
Incorrect oil level.
Fill to correct level.
Excessive side or end thrust.
Correct alignment, adjust belt tension.
EXCESSIVE
WEAR
Incorrect belt tension.
Adjust belts to correct tension.
Seizure.
If machine can not be rotated freely by hand when
unloaded this indicates a serious fault. Examine
and replace any broken or damaged components
before attempting to re-start the compressor.
FAILURE TO
START
Electrical or control fault.
Trace and rectify or consult a qualified electrician.
Summary of Contents for 5211.2.IA
Page 2: ......
Page 14: ...CompAir UK Ltd PUBLICATION 98407 1050 Page 12...
Page 16: ...CompAir UK Ltd PUBLICATION 98407 1050 Page 14 REMARKS DATE REMARKS DATE...
Page 22: ...CompAir UK Ltd PUBLICATION 98407 1050 Page 20...
Page 32: ...CompAir UK Ltd PUBLICATION 98407 1050 Page 30...
Page 38: ...CompAir UK Ltd PUBLICATION 98407 1050 Page 36...
Page 61: ......