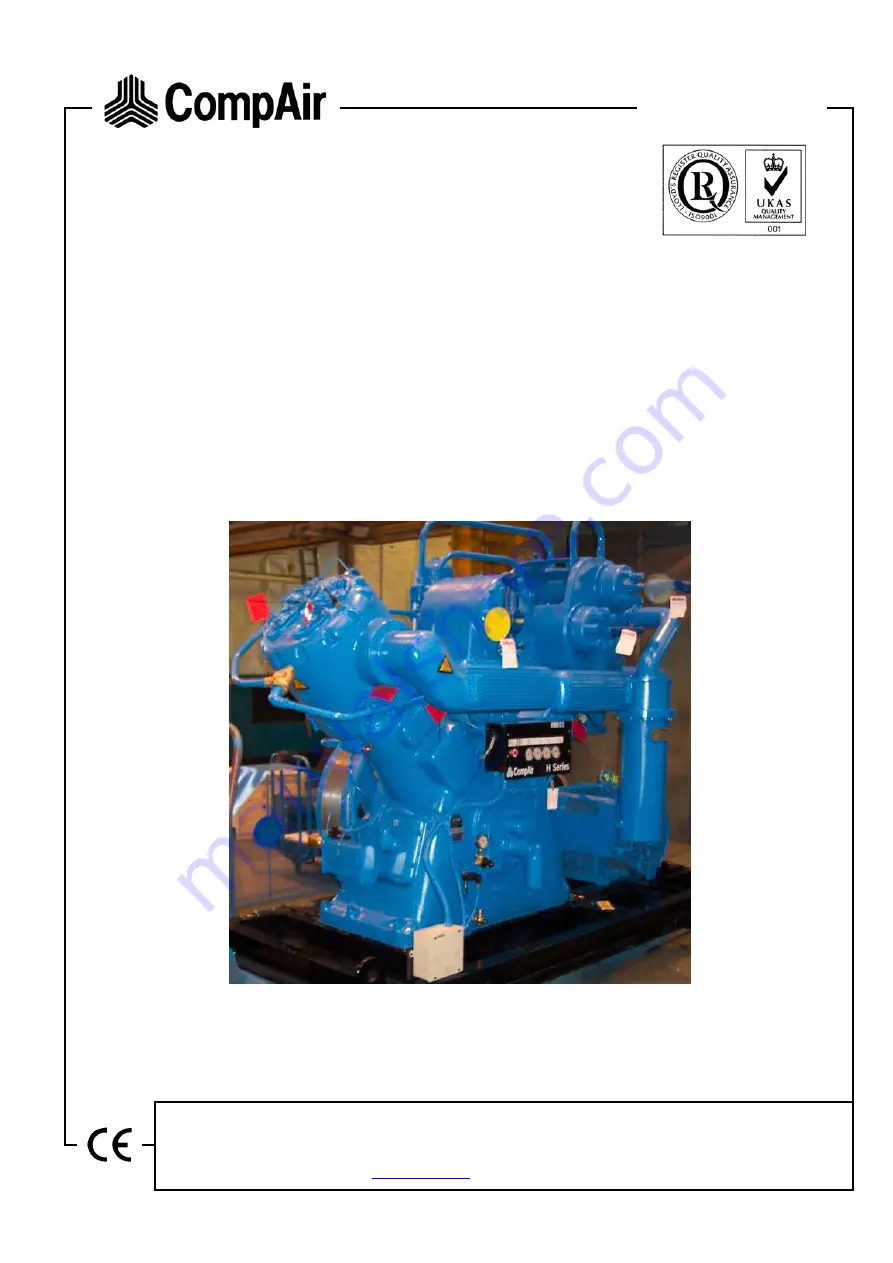
OPERATOR HANDBOOK
for a
5280D.1.IAC
Water-cooled
Air Compressor
In any correspondence please quote:
JOB NUMBER:
MACHINE
NUMBERS:
(on
nameplate)
PUBLICATION
NUMBER:
98407.1440
ISSUE DATE
MARCH 2006
CUSTOMER
ORDER
NUMBER:
CompAir UK Ltd. Reavell House
White House Road IPSWICH ENGLAND IP1 5PB
Telephone: +44 (0) 1473 242000 Fax: +44 (0) 1473 745451 Parts Fax: +44 (0) 1473 743468 S44 (0) 1527 838443
Ipswich@compair.com
CompAir UK Ltd
Summary of Contents for 5280D.1.IAC
Page 3: ...DATE REMARKS DATE REMARKS logsheet5280 d...
Page 9: ...CompAir UK Ltd 5280D Compressor Publication 98407 1440 Page 6 1440 doc...
Page 29: ...CompAir UK Ltd 5280D Compressor Publication 98407 1440 Page 26 1440 doc...
Page 33: ...CompAir UK Ltd 5280D Compressor Publication 98407 1440 Page 30 1440 doc...
Page 39: ......
Page 40: ......
Page 41: ......
Page 42: ...CompAir UK Ltd 5280D Compressor Publication 98407 1440 Page 36 1440 doc...
Page 44: ...CompAir UK Ltd 5280D Compressor Publication 98407 1440 Page 38 1440 doc CRANKCASE 1...
Page 46: ...CompAir UK Ltd 5280D Compressor Publication 98407 1440 Page 40 1440 doc CRANKCASE 2...
Page 48: ...CompAir UK Ltd 5280D Compressor Publication 98407 1440 Page 42 1440 doc CRANKCASE 3...
Page 50: ...CompAir UK Ltd 5280D Compressor Publication 98407 1440 Page 44 1440 doc CYLINDER 1st STAGE...
Page 52: ...CompAir UK Ltd 5280D Compressor Publication 98407 1440 Page 46 1440 doc SUCTION VALVE COVER...
Page 60: ...CompAir UK Ltd 5280D Compressor Publication 98407 1440 Page 54 1440 doc CROSSHEAD 1st STAGE...
Page 62: ...CompAir UK Ltd 5280D Compressor Publication 98407 1440 Page 56 1440 doc PISTON 1st STAGE...
Page 64: ...CompAir UK Ltd 5280D Compressor Publication 98407 1440 Page 58 1440 doc GLAND 1st STAGE...
Page 66: ...CompAir UK Ltd 5280D Compressor Publication 98407 1440 Page 60 1440 doc OIL PUMP...
Page 68: ...CompAir UK Ltd 5280D Compressor Publication 98407 1440 Page 62 1440 doc OIL PUMP FILTER...
Page 70: ...CompAir UK Ltd 5280D Compressor Publication 98407 1440 Page 64 1440 doc INTERCOOLER...
Page 72: ...CompAir UK Ltd 5280D Compressor Publication 98407 1440 Page 66 1440 doc 1st STAGE PIPE WORK...
Page 74: ...CompAir UK Ltd 5280D Compressor Publication 98407 1440 Page 68 1440 doc...
Page 76: ......
Page 77: ......
Page 78: ......
Page 79: ......
Page 80: ......
Page 81: ......
Page 82: ......
Page 83: ......
Page 84: ......
Page 85: ......
Page 86: ...CompAir UK Ltd 5280D Compressor Publication 98407 1440 Page 70 1440 doc...
Page 94: ...CompAir UK Ltd 5280D Compressor Publication 98407 1440 Page 72 1440 doc...
Page 98: ...App 408 Customer PET controller installation guide user s manual Page 2 App 408C 98155 1015...
Page 120: ...CompAir UK Ltd APP 004 ANTI VIBRATION MOUNTS Page 2 app004 doc...
Page 122: ...CompAir UK Ltd PUBLICATION APP070 PRESSURE GAUGES GENERAL Page 2 app070 doc...
Page 128: ...CompAir UK Ltd PUBLICATION APP 138 3 WAY SOLENOID VALVES PS2197 Page 2 app138 doc...
Page 130: ...CompAir UK PUBLICATION APP034 ELECTRIC MOTOR MAINTENANCE GENERAL Page 2 APP034 doc...
Page 133: ...CompAir UK Ltd 5280D Compressor Publication 98407 1440 Page 74 1440 doc...