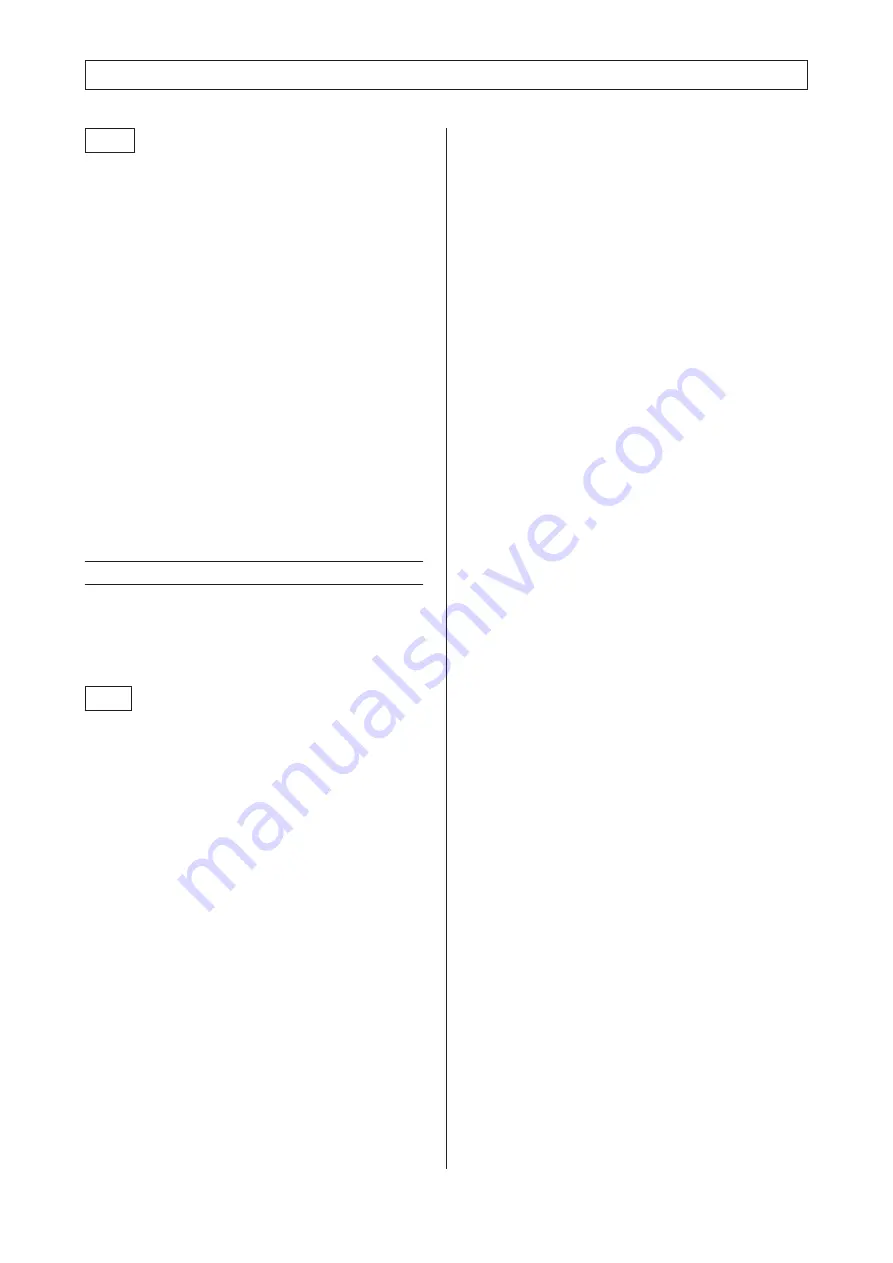
38
8. Servicing and maintenance
Note
Before first commissioning or re-commissioning - after
maintenance - of water-cooled units, bleed the air cool-
er through the bleed screw.
When operating water-cooled screw compressor units,
the following points must be taken into account:
• As a result of leakage in oil/water coolers, some oil
can get into the cooling water circuit.
• Cooling water must not be discharged in an uncon-
trolled manner into public sewage systems.
Uncontrolled overflowing of the oil separator tray
into public sewage systems must be ruled out.
Strictly observe the relevant waste-water regula-
tions.
• Maintenance and repair work has to be carried out
carefully.
Check dismantled bundles of pipes for damage prior
to reinstalling them. In the case of even the slightest
damage, the pipes have to be replaced.
Always use new seals when carrying out assembly
and installation work.
8.12
Lubrication of electric motors
The two bearings of the electric motor must be lubri-
cated at specified intervals, which are determined by
the type of motor.
Additional maintenance data can be found on the in-
dividual motor nameplates.
Note
In the case of 60 Hz drive, strictly observe the infor-
mation on the nameplate !
For lubrication, use lithium-saponified roller bearing
grease that meets the following requirements:
• Consistence class (NLGI):
3
• Worked penetration:
220 - 250
• Drop point:
> 180 °C
• Ash content:
< 4 %
• Water content:
< 0.4 %
This corresponds to lubricating grease to DIN 51 825,
part 1, KH 3R. Roller bearing greases with different
thickeners (soap basis) should not be mixed. The same
is valid for lubricating greases with P additives.
If changing over to another grease cannot be avoid-
ed, please consult the manufacturer of the electric mo-
tor/machine.
Grease recommendation:
• Aral/Aralup
4193
• Esso/Unirex
N3
• SKF/Grease
LGHT3
• SKF/Grease
LGHQ3
• Statoil-UNIWAY
HTC
Lubricate the unit through the two identified lubricat-
ing points located on the outside of the panelling.
Lubricate the compressor unit at the identified lubri-
cating points while the unit is running and use a suita-
ble grease gun.
When lubricating the bearing of the electric motor, al-
ways use the grease quantities as indicated on the in-
dividual motor nameplates.
In order to check the required for lubrication, weigh
the grease gun before and after lubrication of the indivi-
dual electric motor bearings.