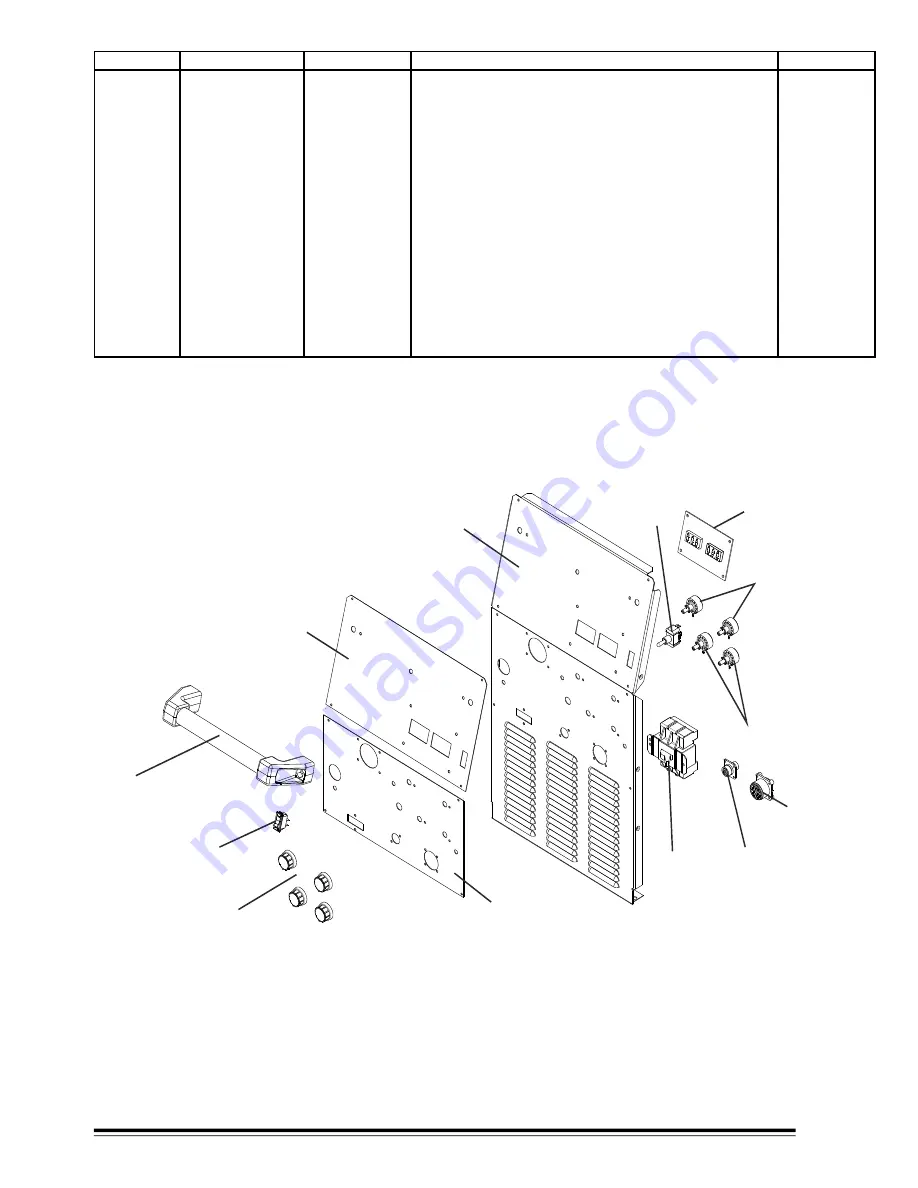
P M 13 7 9
16
1
2
3
4
5
6
7
8
9
11
12
10
13
Ref.
I.D.
Quantity
1
PF0955
Front panel
1
2
PP4656
Nameplate, upper
1
3
PP4655
Nameplate, lower
1
4
Handle assembly. Consisting of:
1
MS03936
Handle support
2
MT08195
Handle
1
5
MI01178
S2
Switch 15A 1P 1T
1
6
MP08416
Knob
4
7
MI00110
S3
Switch 1P1T.
1
8
PT1826
PC2
PC voltmeter/ammeter
1
9
MP02512
R1, 2
Potentiometer 10KOhms, 2W
2
10
MP03020
R3, 4
Potentiometer 500KOhms, 2W
2
11
MR00503
RC1
4 sockets, receptacle
1
12
MR02583
RC2
14 pin, receptacle
1
13
MI01288
S1
Switch, power.
1
Part No.
Description
FIGURE 7-2. FRONT ASSEMBLY