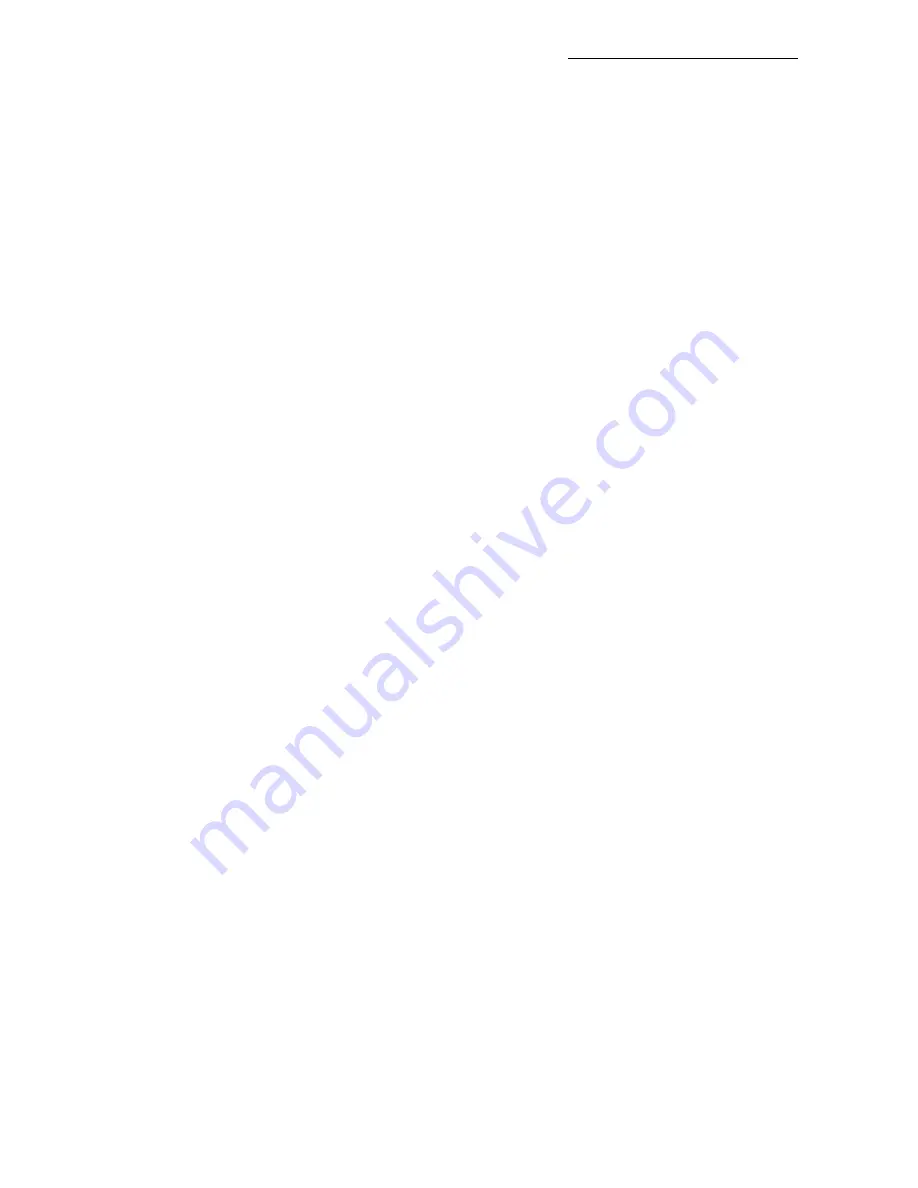
and connect the speedbrake to the servo output arm, which should be of the heavy-duty type.
In the ‘closed’ position the servo arm should angle forwards at about 45 - 50 degrees.
Wings
The wings (and vertical fins) are mounted using a 16mm OD thick-wall aluminium tube
(800mm/31.5” long), and a pair of 6mm diameter brass anti-rotation pins in each wing. They
are retained onto the fuselage, trapping the vertical stabs in between, with a pair of M6 x
40mm allen bolts that are fitted into the plywood wing roots, and screwed into T-nuts that are
factory-installed in the fuselage.
The elastic-hinged control surfaces have already been cut out for you. The slots in all 4 control
surfaces have also been milled for the phenolic horns at the factory. The servos are installed
from the bottom of the wing, with the linkages on the top wing surface. The vertical stabs also
have the elastic-hinged rudders cut loose for you, but you need to mill the slots for the pheno-
lic rudder horns to suit your servo location and linkage.
Install the aluminium tube spar into the fuselage, trial fit the 4 brass anti rotation pins into the
holes in the plywood wing roots and trial fit the wings onto the fuselage, without the vertical stabs.
The top surface of the trailing edge of the wings should be level with the top surface of the trail-
ing edge of the fuselage (see photo P21). A little adjustment of the holes in the fuselage roots
may be necessary, which can be done with a small round file. The brass pins should be a tight
fit in these holes, if they get a bit too big you can fill them with a slow epoxy and micro-balloons
mixture and re-drill.
When satisfied, glue the 4 brass pins permanently into the roots of the wings, leaving 22 - 24mm
(7/8” - 15/16”) projecting past the wing root (P20). Don’t forget to scuff up the ends of the brass
tubes to get a really good glue joint into the plywood root ribs and balsa blocks behind them. We
highly recommend that you use a slow epoxy and milled-fibre or microballoons mixture, or a filled
thixotropic epoxy like Aeropoxy/Hysol 9562. Tape both wings firmly in position on the fuselage
and check that the trailing edges match while the glue cures.
Fit a M6 x 40mm bolt into the hole provided in each wing root, and fit an M6 lock-nut on the out-
side. This nut must not be tight - it is just to prevent the bolt coming out and being lost when the
wings are removed (photo P22). Refit the wings again, this time with the vertical stabs sand-
wiched in between the wings and the fuselage and check that all holes align properly. The M6 T-
nuts for the wing bolts have already been installed in the fuselage at the factory, and you can
access the head of the wing bolts with a ball-ended allen/hex key through the milled slots in the
bottom of the wings.
Note:
Please make sure that the M6 wing bolts thread into the T-nuts at least 4 full turns. There
is some tolerance in the distance of the T-nuts from the wing roots, and we have now increased
the length of these bolts to 40mm for extra security.
Install the 4 phenolic servo horns provided in the pre-milled slots in each wing. Tape the outer
and inner surfaces together in the centres, tip and root at neutral. Make the milled slots a little
deeper, until they almost reach the bottom wing skin. Sand an angle on the bottom of the phe-
nolic horns as shown, so that the top linkage hole in all the horns is about 20mm (7/8”) from the
top wing surface, and about 3 - 4mm behind the hinge slot. Scuff up the surface of the phenolic
horns where they will be glued into the control surfaces to give a good gluing ‘key’.
Important:
The new Rookie is designed to be flown using
both
surfaces on each wing as
Composite-ARF New Rookie
techsupport@composite-arf.com
11