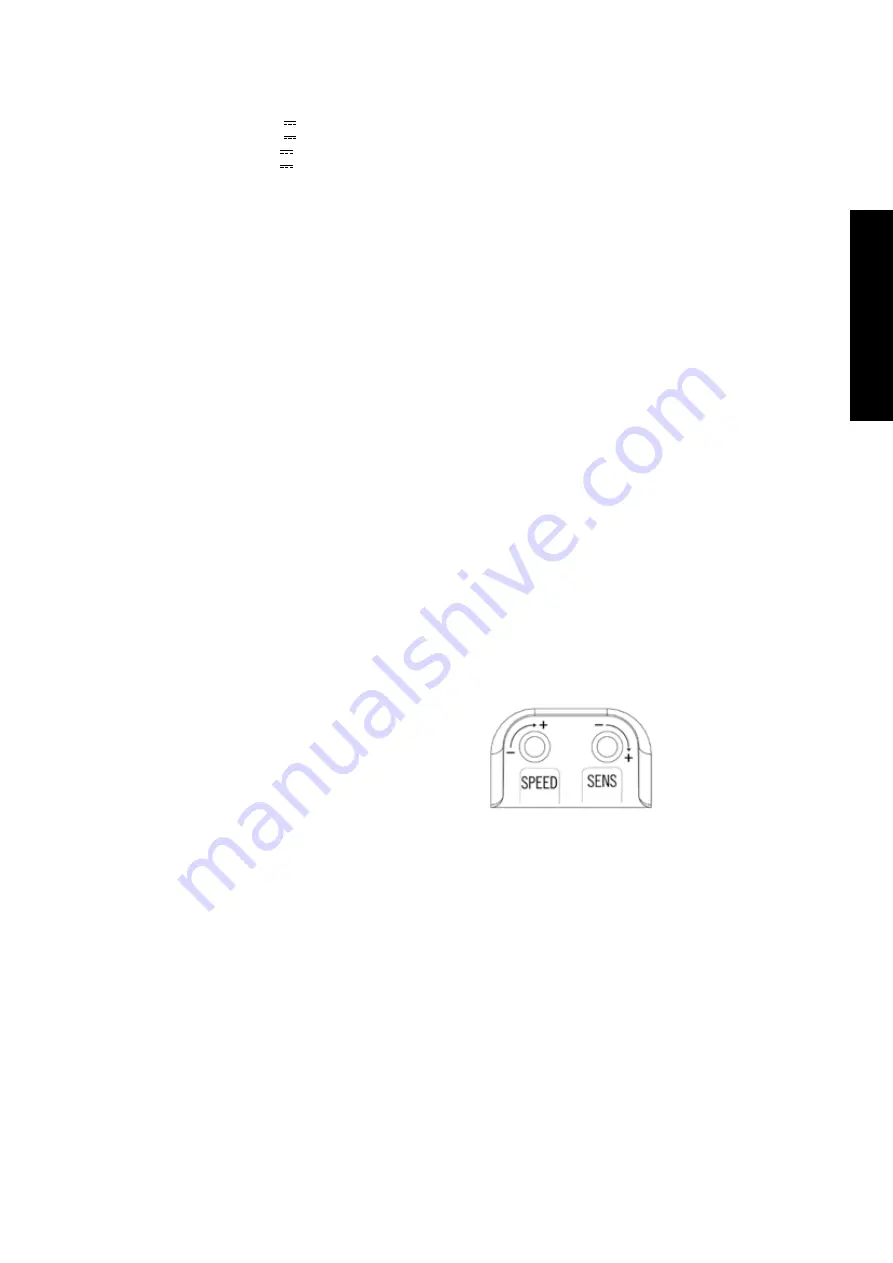
15
COMUNELLO
®Copyright 2014 - All right reserved
ENGLISH
TECHNICAL SPECIFICATIONS
Back-up Battery input:
24 V 7A/h max.
Flashing light output:
24 V 4 W max.
Operator outputs:
24V 1 x 50 W max.
Photocells power supply:
24V 5 W max.
Working temperature:
-20 ÷ + 50 °C
Radio receiver:
433 Mhz
Transmitters:
18 Bit or Rolling Code
Max TX codes stored in memory:
120 (CODE or PED CODE)
Board dimensions:
100x105 mm.
Maximum power consumption
150W
PRELIMINARY CHECKS
• Check that the product in the pack is intact and in good condition.
• Check that the place of installation is suitable and in compliance with the
minimum dimensions shown in FIG. 1.
INSTALLATION
• Drill the box in the four corners and then fix the control unit to the wall
(FIG. 2).
• Drill a hole in the underside of the box for the cable inlet. (FIG. 3)
The use of cable glands is recommended.
ELECTRICAL CONNECTIONS
CN1:
BATT+24V:
+24V Back-up Battery input
BATT-24V:
–24V Back-up Battery input.
LAMP+24V:
+24V Flashing Light Output.
LAMP-24V:
–24V Flashing Light Output.
MOT1+:
Operator 1 + Output.
MOT1-:
Operator 1 – Output.
CN2:
STOP:
Emergency stop input (NC)
GND:
Common GND input
FOTO+:
Photocells Control and Power Supply (24V 5W).
GND:
Photocells Control and Power Supply (GND).
FCC:
Operator Closing Limit Switch Input (NC).
GND:
Common GND input
FCA:
Operator Opening Limit Switch Input (NC).
DS1:
Safety Device Input (NC).
GND:
Common GND input
PP:
Pedestrian Pushbutton open-close command input (NO).
ANT-:
Antenna Ground Input.
ANT+:
Antenna Hot pole input.
CN3:
L:
230 V~ line input (phase).
N:
230 V~ line input (neutral).
TRANSFORMER CONNECTIONS
CN4 1st:
1:
230 V~ Transformer Primary Winding Input.
2:
230 V~ Transformer Primary Winding Input.
CN5 2nd:
1: Transformer SEC 1 Output 21.7V 7.5A no-load voltages.
2: Transformer SEC 1 Output 21.7V 7.5A no-load voltages.
FUNCTIONAL CHARACTERISTICS
AUTOMATIC OPERATION:
When either the remote or the low voltage pushbutton panel is used to
control the gate, operation is as follows:
the first command opens the gate until motor time elapses or until the gate
reaches its opening limit position; the second command closes the gate; if
another command is transmitted before motor time has elapsed or before
one of the two limit stops has been reached, the control unit reverses the
movement direction during both opening and closing.
STEP-BY-STEP OPERATION:
When either the remote or the low voltage control pushbuttons are used to
control the gate, operation is as follows:
the first command opens the gate
until motor time or until the gate
reaches its opening limit position; the second command closes the gate;
if another command is transmitted before motor time has elapsed or
before one of the limit stops has been reached, the control unit stops the
movement. Another command causes the gate to start moving again in the
opposite direction.
Step-by-step 1 operations:
When either the remote or the low voltage control pushbuttons are used to
control the gate, operation is as follows:
the first command opens the gate
until motor time or until the gate
reaches its opening limit position; the second command closes the gate;
if another command is transmitted before motor time has elapsed or
before one of the limit stops has been reached, the control unit stops the
movement during both opening and closing. Another command causes the
gate to start moving again in the opposite direction.
AUTOMATIC CLOSING:
The control unit can be set up to close the gate automatically without
sending any additional commands.
The selection of this type of operation is described in Pause time
programming mode.
PEDESTRIAN OPENING:
By means of the remote (CODE P. LED lit) the remote control makes it
possible to drive the Operator for a programmable time, typically to allow
pedestrian access.
EMERGENCY STOP INPUT:
The control unit allows the connection of an emergency stop pushbutton
(NC). Pressing this pushbutton irrespective of the current operating mode
of the control unit will cause immediate stopping of the gate movement. An
additional gate movement command will be valid provided the emergency
stop input is deactivated and, in any case, the control unit will execute the
gate opening cycle with 5 seconds preflashing.
IMPORTANT:
Jumper this input if it is not to be used.
PHOTOCELLS:
Photocells can be powered by and connected to the control unit in
accordance with directive EN 12453.
Tripping of the photocells during opening is disregarded, while during
closing it causes reversal of the direction of movement.
To allow operation in compliance with EN 13849-1, Category 2 a photocell
test is performed before each movement. The control unit enables the
movement only if the test is passed; if it is not, the control unit inhibits
all movements and an alarm condition is signalled by blinking of all the
programming LEDs on transmission of each command.
OBSTACLE DETECTION (SENS):
The electronic control unit is equipped with a “SENS” trimmer, completely
managed by the microprocessor, for adjustment of the opposing Force
required to detect the presence of an obstacle.
The adjustment can be made with a trip time from a minimum of 0.1
seconds to a maximum of 7 seconds.
IMPORTANT:
• If limit switches are connected to the control unit detection of an obstacle
will always result in movement reversal during closing and reversal for 2
seconds during opening.
• If there are no limit switches connected to the control unit detection of an
obstacle will always result in movement reversal during closing (except
in the final 5 seconds of the movement, when it will cause a Stop) and
reversal for 2 seconds during opening (except in the final 5 seconds of
the movement, when it will cause a Stop).
Obstacle detection system also works with automations without
encoder.
OPERATOR SPEED ADJUSTMENT (SPEED):
The electronic control unit is equipped with a “SPEED” trimmer for
operator speed adjustment, completely managed by the microprocessor.
Adjustment can be performed in a range of between 50% and 100% of