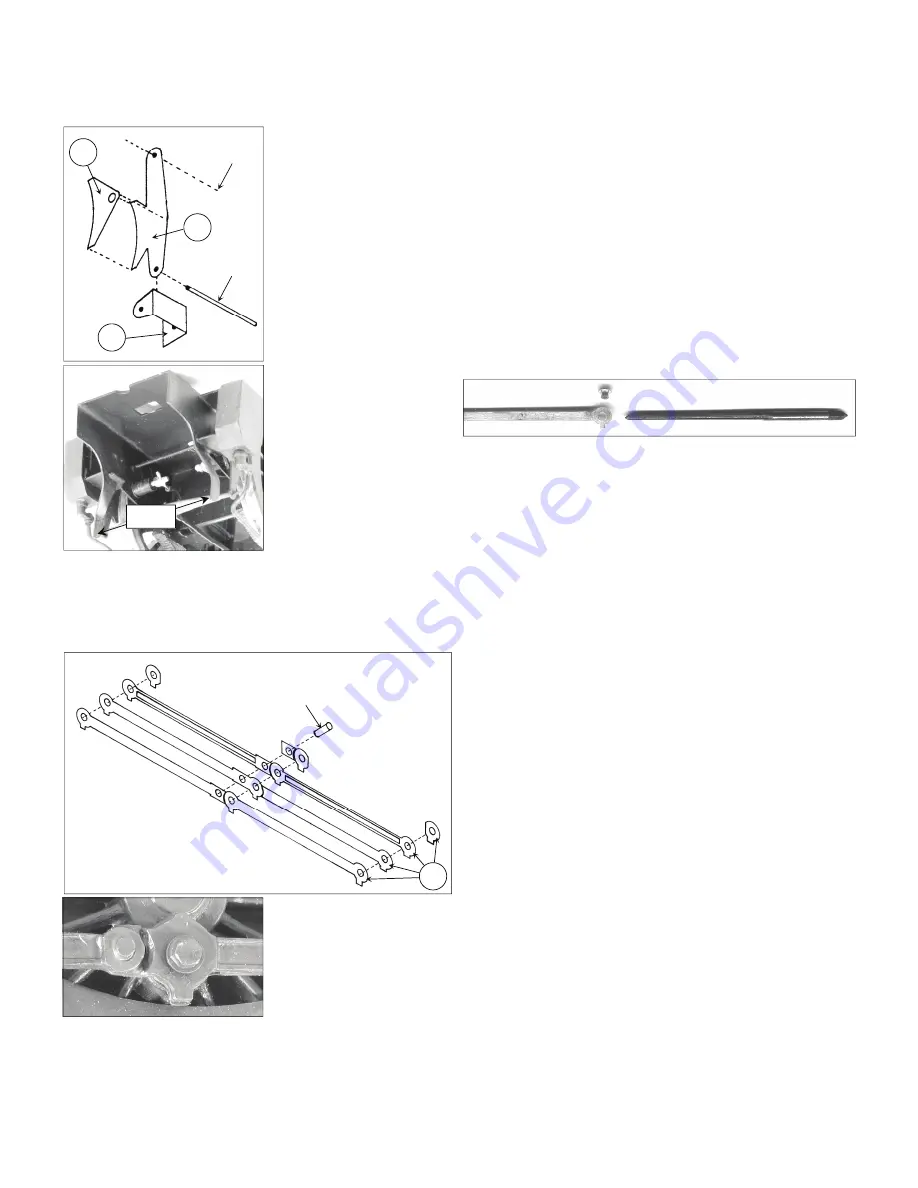
11.
Now
pre
pare the Slater’s
w
hee
ls. Rem
ove a
ny pl
astic
flash or
mould
ing
p
ips
fro
m the b
ack
s of th
e wheel
b
y ru
bbing
them
fla
t o
n a
piece o
f
fine e
mery
cloth (this
flash can
some
tim
es
interfe
re w
ith
the p
lung
er pickups). T
he cra
nkp
in
screw
head
needs to b
e f
lus
h w
ith
the b
ack
of t
he w
hee
l (it
ma
y interf
ere w
ith the
shou
lder of the b
earing o
th
erw
ise) so
it
will be necessar
y to drill a
countersink
hole. Us
e a 2.5mm
drill in a hand held pin ch
uck. Drill gently
and ke
ep checking
with
the
head
of the
screw
until
the ho
le is the
corre
ct
depth
.
Th
e scre
w is d
esi
gned
to se
lf t
ap in
to the
plas
tic
and t
hen
lock itsel
f. I don’t trust this and
prefer to screw
it in until the
head is just proud of
the w
heel b
ack
. I then fill the
counte
rsink h
ole w
ith
Ara
ldite
and then screw
it in until it
locks. Le
ave the
whee
ls un
til the Ara
ldite ha
s s
et and th
en
clean o
f a
ny e
xcess Araldite
by
rubbin
g the
whe
el
on the
emery
cloth
. This sh
ould leave the
scre
w h
ead
em
bed
ded in
Araldite and
p
rev
ent
the po
tential prob
lem of
the scre
w
turning
w
hen
yo
u are tr
ying
to
u
ndo
the cran
kp
in nut.
Y
ou m
ay f
ind
th
at the s
qua
re axle e
nd is a tigh
t f
it into the
centre of th
e w
he
el a
nd
th
is needs correcting
. W
ith
a f
ine
fla
t
file ge
ntly dress
each o
f th
e f
our
sides o
f the
a
xle
end
. I find i
t
helps to
lay the
bottom f
lat
of th
e axle end
onto th
e edge
of a
block
of w
ood. This help
s m
e k
eep
the f
ile parallel as I
file the
top fla
t. O
ffe
r the
axle end in
to the w
hee
l centre
an
d repeat i
f
nece
ssary
. Y
ou are
aimin
g to get a
gentle
push
fit bu
t w
ith
no
roc
king
or m
ove
me
nt on
the
squa
re. A go
od gu
ide is to
get it
so that you can rem
ove
the
whee
l fro
m the
axle with ju
st your
fing
er nails arou
nd the st
eel tyre. If
yo
u have
to
g
rip the
ty
re
with
your f
inger ends to
pull it off yo
u w
ill find it diff
icult to
rem
ove the w
hee
ls to p
aint th
e chassis.
Once h
app
y f
it
the
wheel sets int
o the ch
assis
remem
bering to
quarter the
whee
ls (the cran
kp
ins on on
e side sho
uld
lead t
he othe
r by
90°).
Ch
eck th
at th
e cha
ssis sit
s leve
l on a
fla
t su
rface
with
out
rock
ing (t
wist slig
htly
if re
quire
d). The
centre w
hee
ls a
re
raise
d sligh
tly
to preven
t th
e loco
rockin
g on
uneven
track
and so th
ese w
hee
ls w
ont
revolve if th
e chassis is push
ed
alon
g th
e be
nch.
12.
Make
up the cou
plin
g rods (p
arts 55) by
lamin
ating
togeth
er the three
parts
of ea
ch section
an
d then
fitting
the
separa
te bosses. The
ro
ds are desig
ned
to be
jointed b
y
overlapping
on th
e ce
ntre
crank pin. A sh
ort length
of
1.8
mm
copp
er
ro
d is fitte
d
into th
e couplin
g rod at
the
section that cosm
etically
represents the
prototyp
e
joint.
24
Copp
er rod to
fo
rm
joint pin
PAGE 14
No
w op
en
out the
cran
kp
in ho
les in the rod
s to
accept the
brass top h
at b
earing
bushes. T
his is b
est d
one
w
ith a
tape
red
broa
ch or
tape
red e
ngi
nee
rs re
ame
r (I ha
ve on
e tha
t
tapers f
rom
3mm
to 2m
m an
d is 40mm
long
(see y
ello
w
page
s fo
r a good
e
ngi
neers too
l m
erch
ant they ar
e not
cheap
but w
ill last a lifeti
me).
W
ith the
ream
er gently w
ork
fro
m both
sides of the
rod un
til the b
ush is a s
moo
th f
ree
fit into
the
hole.
No
w f
it the rods and
ch
eck th
at the cha
ssis runs f
ree
ly and
that the w
heel
s w
ill turn w
ithout binding. If
yo
u do have
a
pro
blem
gently
revolve t
he
whee
ls w
ith
your f
ing
er tip
until
you h
it t
he tig
ht sp
ot th
en ch
eck th
e ro
ds. Y
ou
shou
ld find
that one rod still
mo
ves freel
y on the crank
pins a
nd
this side
is OK. Y
ou
should f
ind
th
at th
e rod
on th
e othe
r side
is tig
ht
on
the
crank p
ins a
nd this is
whe
re
the
proble
m is. Norm
ally
the pro
ble
m is a cran
kpin scre
w that is
not squ
are in the
whe
el (unle
ss
you
have
reamed
th
e hole
in the
rod o
ut o
f
squa
re).
W
ith
a ro
und
file
gent
ly f
ile o
val
the h
ole in
the r
od
until it f
its
fre
ely
onto th
e crank
pins an
d then ref
it t
he rod
and
chec
k th
e chas
sis again
.
At this stag
e don'
t w
orr
y abo
ut slig
ht tight
spots.
If y
ou ca
n
push the
chassis
along the
bench
w
itho
ut t
he w
heels
skidd
ing a
long
then
all is OK
. As the
whee
ls are
best
remo
ved fo
r p
ainting
th
e chassis th
e chan
ces ar
e that the
y
will not go
back on in th
e same
place. The
correct point to
mak
e f
ina
l a
djustm
ent
s is after pa
inting and
fitting pick
ups
but
be
for
e fitt
ing th
e mo
tor.
If
you
have
file
d a cra
nkpin
ho
le
in the r
ods ov
al it is
w
ort
h m
ark
ing this wheel
so that
you
can
match
them
up ag
ain on
re
assem
bly. No
w rem
ove the ro
ds
and
p
lace sa
fe
ly to
one si
de.
Using
long
nosed
plie
rs
ben
d sets into
the fr
ont
end
gua
rd iron
s so that
they
are
32m
m (r
ail ga
uge
) ap
art.
13.
Tak
e
the
brake
han
gers (parts
56)
and
solder brak
e blo
cks
(parts
57)
to them. Ma
ke
u
p thre
e
left
hand
and thre
e righ
t
hand
sets
. Th
read
leng
ths o
f
0.9
mm
brass w
ire acr
oss
the ch
assis and sp
ot solde
r
to
the in
side
o
f
th
e
sidefr
am
es. Fold u
p
the
bra
ke ha
nger
b
ra
ck
ets
(parts
58
) th
en th
re
ad
bra
cket an
d brake ha
nger
onto the w
ire. Solder th
e
brac
ke
t to
the sid
e f
ram
e
and lin
e up b
rake b
loc
k just
clear of th
e whe
el and
solder to
wire. I f
ind it helpfu
l
to hold
the b
rak
e ha
nger
usin
g a min
iature electrical
crocodile clip as I s
old
er it
in
positio
n. I f
it all six bra
kes
to roug
hly
line u
p w
ith
th
e w
heels
first an
d then
work
around t
weak
ing
with
plie
rs or resolde
rin
g
until I a
m hap
py th
at the
y are po
sitioned
correctl
y w
ith
n
o risk
of to
uchin
g a w
he
el.
32m
m
56
58
57
0.9m
m w
ire
Cross shaf
t
PAGE 15