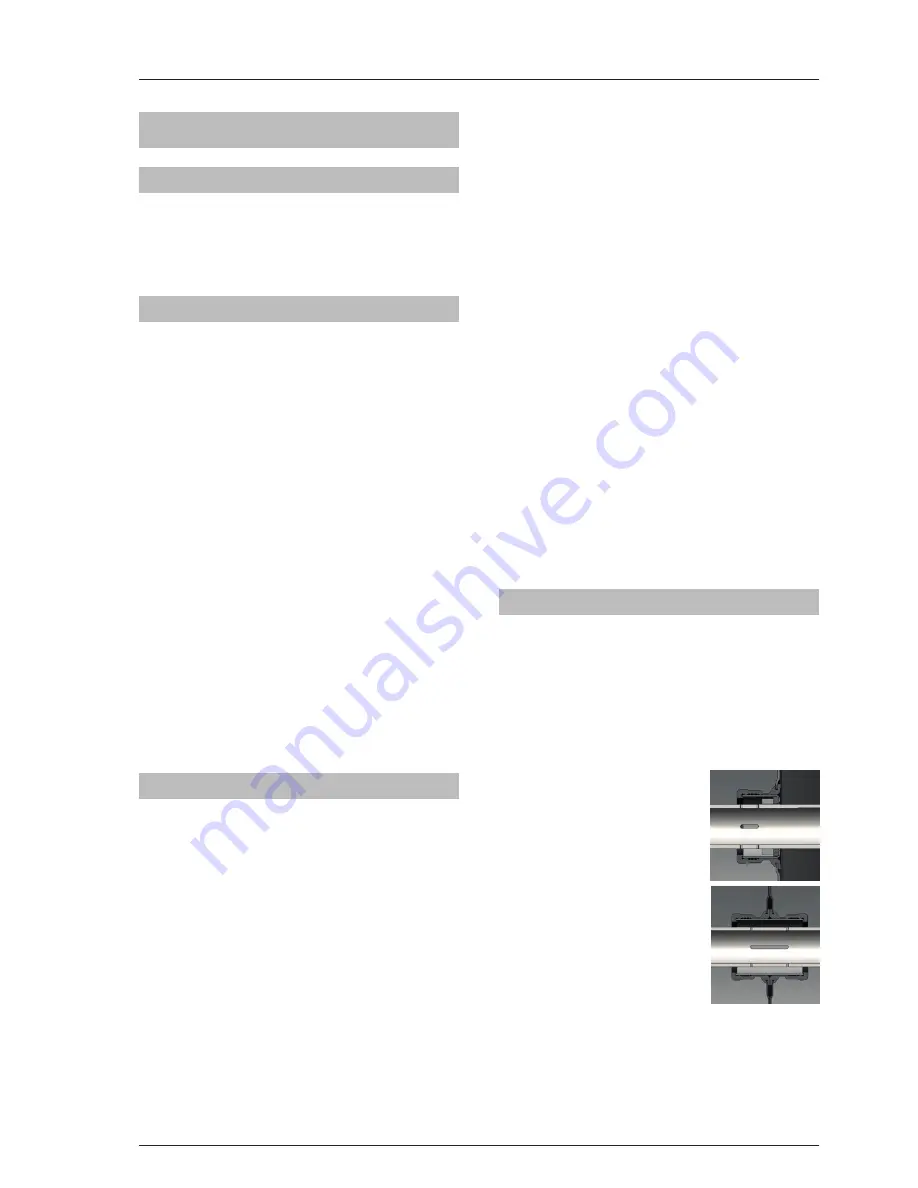
5
Heating circuit and fresh water station
All the connected heating circuits and transfer stations are
required to be diffusion proof. If this is not guaranteed, a
system separation has to be planed. Diffusion tightness ac-
cording to DIN 4726 (0.1 g/m³ and day) is not sufficient.
NOTE:
In the case of heating circuits where sludge formation
is likely we recommend the installation of a sludge filter or
separator (supplier such as Spiro).
It is recommended to use an heating circuit mixer, to ensure
the flow temperature depending on the outside temperature.
This will significantly reduce the energy consumption. Con-
densate formation in the lower store area must be prevent-
ed by control engineering and hydraulic measures to avoid
temperatures below room temperature.
Connection pipes:
Generally, siphoned connections are to be
used, see section 5.1. Otherwise it is imperative to install U
shaped pipe runs with appropriate offset in proximity to the
store. This is required to prevent inadmissible tension on the
store connection during thermal expansion.
NOTE:
After assembly the store must undergo a pressure
test with at least 1.2 times the maximum of the operating
pressure, i.e. 3 bar. For this purpose shut-off facilities to the
connected heating system should be provided.
3�4 Modular design of buffer store
The modular design of the buffer allows an easy increase of
the storage capacity.
Seal of the pipe penetrations
For the permanent sealing of pipe penetrations, a special
seal system was developed and carefully tested. It seals the
individual modules at the pipe penetrations against each
other through flat and lamel-
lar seals. It is based on proven
long-lasting elastomers in conjunc-
tion with stainless steel sleeves.
The seals act immediately without
pressure during filling and empty-
ing. With increasing pressure, the
sealing function increases. The seal-
ing system was successfully tested
in a pressure change test facility at
the ITW of the University of Stuttgart
with 20 000 cycles from 0 to 6 bar
at 20 °C and with 15 000 cycles at
90-60 °C.
3 Planning aids
3�1 Transport
The store modules must be transported upright. The indi-
vidual modules are delivered on a pallet and can be easily
transported with a forklift truck.
3�2 Notes on buffer water
Water quality
The water quality of the store should at least conform to the
guideline VDI 2035 for heating water. Further requirements
of the manufacturer are to be observed! We recommend
the use of de-ionised water to reduce the risk of corrosion
and calcification in store / heating system. In case of the
addition of substances such as antifreeze to the water cir-
cuit, ask your supplier of the substance wether it is compati-
ble with steel and EPDM.
NOTE:
It is to ensure that no other materials or substances
(such as sludge, sealants, anticorrosive, etc.) can get in the
store, e.g. from existing components of the heating system.
Do this through appropriate measures such as flushing of
the system, filters, etc.
Expansion tank safety
A volume expansion tank to compensate the thermal expan-
sion has to be sized and installed accordingly. A suitable
safety valve without shut-off facility must be connected to
the buffer.
Minimum room sizes for the module installation see 4�3
3�3 Connection to boiler and heating circuit
Boiler
The modular buffer store allows the connection of differ-
ent heating circuits and heat generators at the positions
corresponding to their temperature. Boiler and heating
circuits are connected directly to the store. This means up
to approx. 200 kw can be transferred depending on the
temperature difference. Larger capacities and flow rates
(see below) are possible by connecting to both sides of the
store. The modular buffer store is designed for low return
temperatures. With boilers which are sensitive to low return
temperatures precautions must be taken, especially if the
bottom connection is used.
Connections:
The connections of the modular buffer are lo-
cated in a vertical line on each end. They are connected via
pipes for low turbulence loading up to approx. 13 m³/h.
T D M A - VA R I C A L :
Planing aids