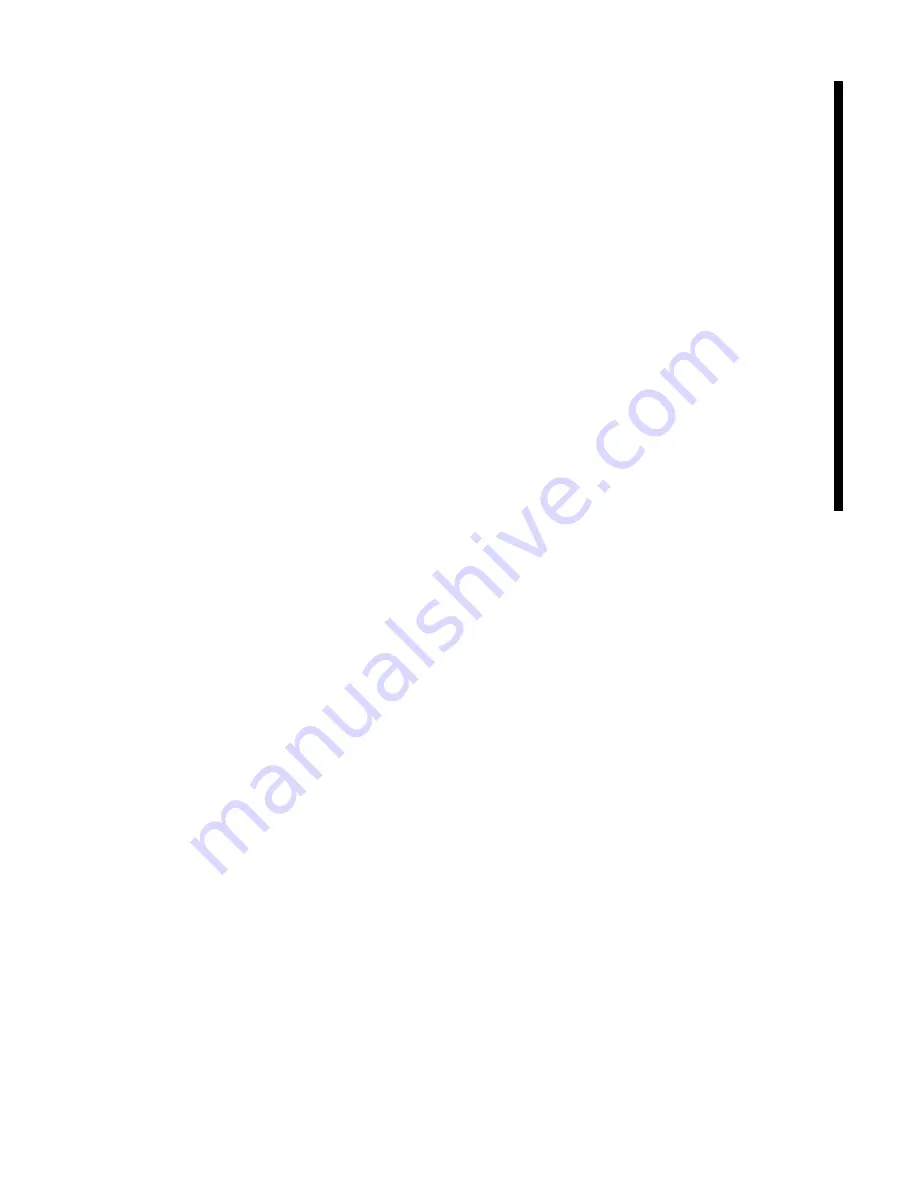
November 2011
1-00-01
CHAPTER 1
INTRODUCTION
1-00-00
SCOPE
1-00-01
Advisories
1-00-02
Related Publications
1-00-03
Service Documents
1-00-04
Service Reports and Inquiries
1-00-05
100% Replacement Parts
1-10-00
DEFINITIONS & ABBREVIATIONS
1-10-01
Abbreviations/Symbols
1-10-02
Definitions
1-10-03
Description of Engine Model Code
1-10-04
Basic Design Features
1-20-00
TOOLS
1-20-01
Special Tools
1-30-00
PRODUCTS
1-30-01
Product List
Summary of Contents for LTSIO-520-AE
Page 18: ...xviii February 1989 INTENTIONALLY LEFT BLANK ...
Page 34: ...1 10 10 February 1989 INTENTIONAllY LEFT BLANK ...
Page 80: ...1 30 06 February 1989 INTENTIONALLY LEFT BLANK ...
Page 81: ...CHAPTER 4 AIRWORTHINESS LIMITATIONS February 1989 4 00 01 ...
Page 82: ...4 00 02 February 1989 INTENTIONALLY LEFT BLANK ...
Page 84: ...4 00 04 February 1989 INTENTIONALLY LEFT BLANK ...
Page 86: ...5 00 02 February 1989 INTENTIONALLY LEFT BLANK ...
Page 88: ...5 00 04 February 1989 INTENTIONALLY LEFT BLANK ...
Page 90: ...5 10 02 February 1989 INTENTIONALLY LEFT BLANK ...
Page 94: ...INTENTIONALLY LEFT BLANK 5 20 04 February 1989 ...
Page 96: ...5 30 02 February 1989 INTENTIONALLY LEFT BLANK ...
Page 98: ...70 00 02 February 1989 INTENTIONALLY LEFT BLANK ...
Page 100: ...70 0 04 February 1989 INTENTIONALLY LEFT BLANK ...
Page 102: ...70 10 02 February 1989 INTENTIONALLY LEFT BLANK ...
Page 104: ...70 20 02 February 1989 INTENTIONALLY LEFT BLANK ...
Page 106: ...70 30 02 February 1989 INTENTIONALLY LEFT BLANK ...
Page 108: ...70 40 02 February 1989 INTENTIONALLY LEFT BLANK ...
Page 116: ...72 00 02 February 1989 INTENTI0 NALlY LEFT BLANK ...
Page 130: ...72 00 16 February 1989 INTENTIONALLY LEFT BLANK ...
Page 132: ...72 10 02 INTENTIONALLY LEFT BLANK ...
Page 153: ...INTENTIONALLY LEFT BLANK 72 10 23 ...
Page 171: ...INTENTIONALLY LEFT BLANK 72 10 41 ...
Page 173: ...7 9 10 12 11 2 81 FIGURE 72 10 15 CRANKCASE 72 10 43 ...
Page 178: ...72 10 48 INTENTIONALLY LEFT BLANK ...
Page 180: ...72 20 02 INTENTIONALLY LEFT BLANK ...
Page 196: ...72 20 18 February 1989 INTENTIONALLY LEFT BLANK ...
Page 211: ...FIGURE 72 30 08 TABLE OF LIMITS CHART 3 72 30 15 ...
Page 220: ...72 40 02 INTENTIONALLY LEFT BLANK ...
Page 238: ...72 40 20 INTENTIONALLY LEFT BLANK ...
Page 240: ...72 50 02 INTENTIONALLY LEFT BLANK ...
Page 258: ...72 60 02 INTENTIONALLY LEFT BLANK ...
Page 276: ...72 60 20 INTENTIONALLY LEFT BLANK ...
Page 278: ...72 70 02 INTENTIONALLY LEFT BLANK ...
Page 286: ...72 70 10 INTENTIONALLY LEFT BLANK ...
Page 288: ...72 80 02 INTENTIONALLY LEFT BLANK ...
Page 294: ...72 80 08 INTENTIONALLY LEFT BLANK ...
Page 296: ...73 00 02 INTENTIONALLY LEFT BLANK ...
Page 298: ...73 00 04 INTENTIONALLY LEFT BLANK ...
Page 304: ...73 10 06 INTENTIONALLY LEFT BLANK ...
Page 306: ...74 00 02 February 1989 INTENTIONALLY LEFT BLANK ...
Page 315: ...CHAPTER 75 AIR 75 00 00 GENERAL 75 00 01 ...
Page 316: ...75 00 02 INTENTIONALLY LEFT BLANK ...
Page 318: ...75 00 04 INTENTIONALLY LEFT BLANK ...
Page 320: ...76 00 02 February 1989 INTENTIONALLY LEFT BLANK ...
Page 322: ...76 00 04 February 1989 INTENTIONALLY LEFT BLANK ...
Page 384: ...76 00 66 February 1989 INTENTIONALLY LEFf BLANK ...
Page 386: ...77 00 02 February 1989 INTENTIONALLY LEFT BLANK ...
Page 388: ...77 00 04 February 1989 INTENTIONALLY LEFT BLANK ...
Page 402: ...78 00 02 February 1989 INTENTIONALLY LEFT BLANK ...
Page 404: ...78 00 04 February 1989 INTENTIONALLY LEFT BLANK ...
Page 406: ...78 10 02 February 1989 INTENTIONALLY LEFT BLANK ...
Page 408: ...78 20 02 February 1989 INTENTIONALLY LEFT BLANK ...
Page 410: ...79 00 02 February 1989 INTENTIONALLY LEFT BLANK ...
Page 412: ...79 00 04 February 1989 INTENTIONALLY LEFT BLANK ...
Page 414: ...79 10 02 February 1989 INTENTIONALLY LEFT BLANK ...
Page 416: ...79 20 02 February 1989 INTENTIONALLY LEFT BLANK ...
Page 418: ...80 00 02 February 1989 INTENTIONALLY LEFT BLANK ...
Page 437: ......
Page 438: ...www continentalmotors aero Continental Motors Inc ...