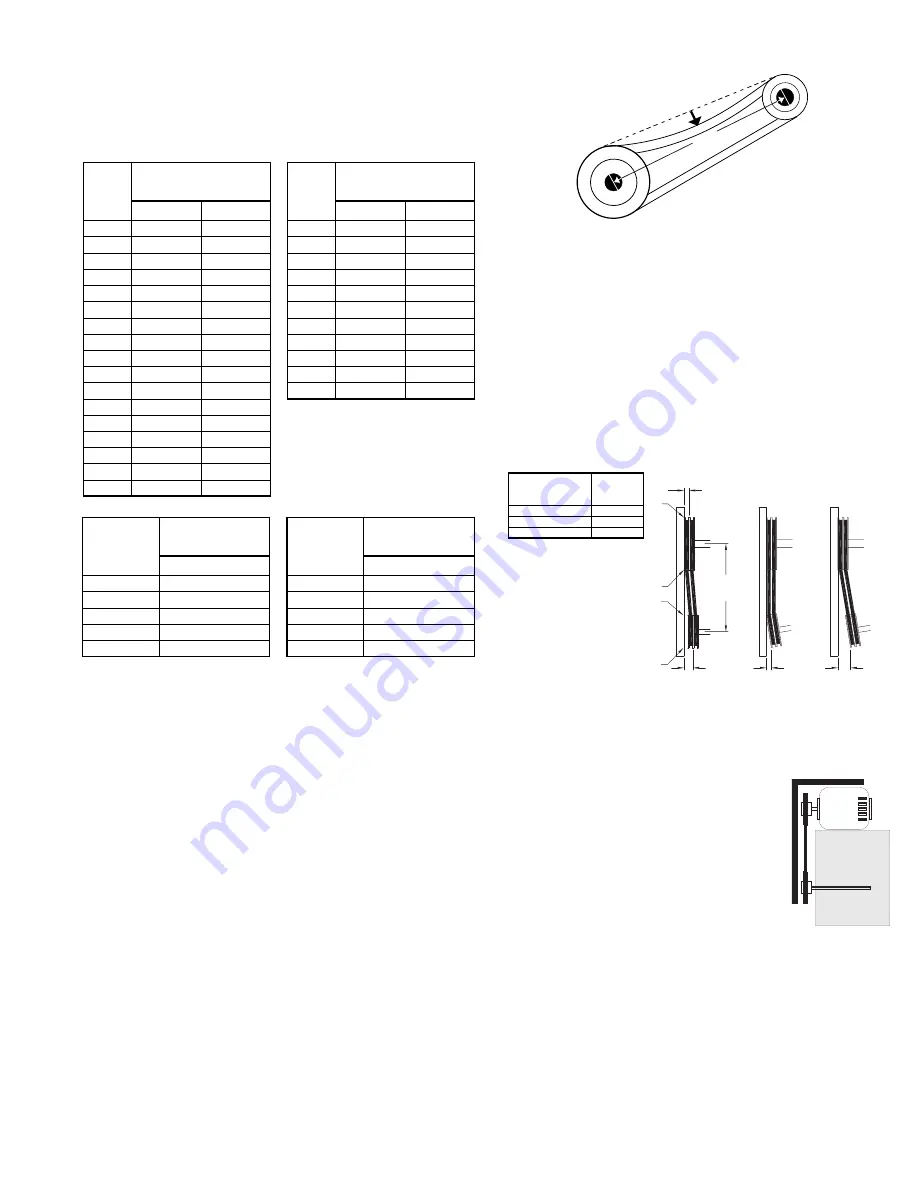
5
Replacing Pulleys and Belts
a. Clean the motor and fan shafts.
b. Loosen the motor plate mounting bolts to relieve the
belt tension. Remove the belt.
c. Loosen the pulley setscrews and remove the pulleys
from the shaft.
If excessive force is required to remove the pul-
leys, a three-jaw puller can be used. This tool,
however, can easily warp a pulley. If the puller is
used, inspect the trueness of the pulley after it is
removed from the shaft. The pulley will need
replacement if it is more than 0.020 inch out of
true.
d. Clean the bores of the pulleys and place a light coat of
oil on the bores.
e. Remove grease, rust and burrs from the pulleys.
f. Place fan pulley on the fan shaft and the motor pulley
on the motor shaft. Damage to the pulleys can occur
when excessive force is used in placing the pulleys on
their respective shafts.
g. After the pulleys have been correctly placed back onto
their shafts, tighten the pulley setscrews.
Belt and Pulley Installation
Belt tension is determined by the sound of the belts when
the fan is first started. The belts will produce a loud squeal,
which dissipates after the fan is operating at full capacity. If
belt tension is too tight or too loose, lost efficiency and
damage can occur.
Do not change the pulley pitch diameter to change tensi-
sion. The change will result in a different fan speed.
a. Loosen motor plate adjustment bolts and move motor
plate so that the belts easily slip into the grooves on
the pulleys. Never pry, roll, or force the belts over the
rim of the pulley.
b. Slide the motor plate back until proper tension is
reached. For proper tension, a deflection of approxi-
mately 1/4” per foot of center distance should be
obtained by firmly pressing the belt. Refer to
Figure 1
.
c. Lock the motor plate adjustment bolts in place.
d. Ensure pulleys are properly aligned. Refer to
Figure 2
.
Pulley Alignment
Pulley alignment is adjusted by loosening the motor pul-
ley setscrew and by moving the motor pulley on the motor
shaft.
Figure 2
indicates where to measure the
allowable gap for the drive alignment toler-
ance. All contact points (indicated by
WXYZ) are to have a gap less than the tol-
erance shown in the table. When the pul-
leys are not the same width, the allowable
gap must be adjusted by half of the differ-
ence in width.
Figure 3
illustrates using a
carpenter’s square to adjust the position of
the motor pulley until the belt is parallel to
the longer leg of the square.
Bearing Replacement
The fan bearings are pillow block type ball bearings.
a. Remove the old bearing.
b. Remove any burrs from the shaft by sanding.
c. Slide new bearings onto the shaft to the desired loca-
tion and loosely mount bearings onto the bearing sup-
port. Bearing bolts and setscrews should be loose
enough to allow shaft positioning.
1 foot
1/4 inch
Figure 1
OFFSET
ANGULAR
OFFSET/ANGULAR
A
W
X
Y
Z
B
CENTER
DISTANCE
(CD)
GAP
GAP
Figure 2
Tolerance
Center Distance
Maximum
Gap
Up thru 12”
1/16”
12” up through 48
1/8”
Over 48”
1/4”
Figure 3
Maximum RPM
VCR
Size
Maximum RPM
VCR-HP
Size
Maximum RPM
Standard
Reinforced
Standard
Reinforced
100
2002
-
150
1952
-
120
1671
-
165
1728
-
135
1574
-
180
1829
-
150
1520
-
195
1570
-
165
1295
-
210
1626
-
180
1546
-
225
1435
-
195
1353
-
245
1185
1234
210
1227
-
270
1025
1049
225
1086
-
300
980
1046
245
901
-
330
830
912
270
766
-
365
735
872
300
837
877
330
716
748
365
624
659
402
539
560
445
463
473
490
360
403
Maximum RPM
VCR-XP
Size
Maximum RPM
VCR-XP
Size
Maximum RPM
Standard
Standard
165
2508
245
1616
180
2396
270
1656
195
2100
300
1391
210
2126
330
1182
225
1879
365
1132