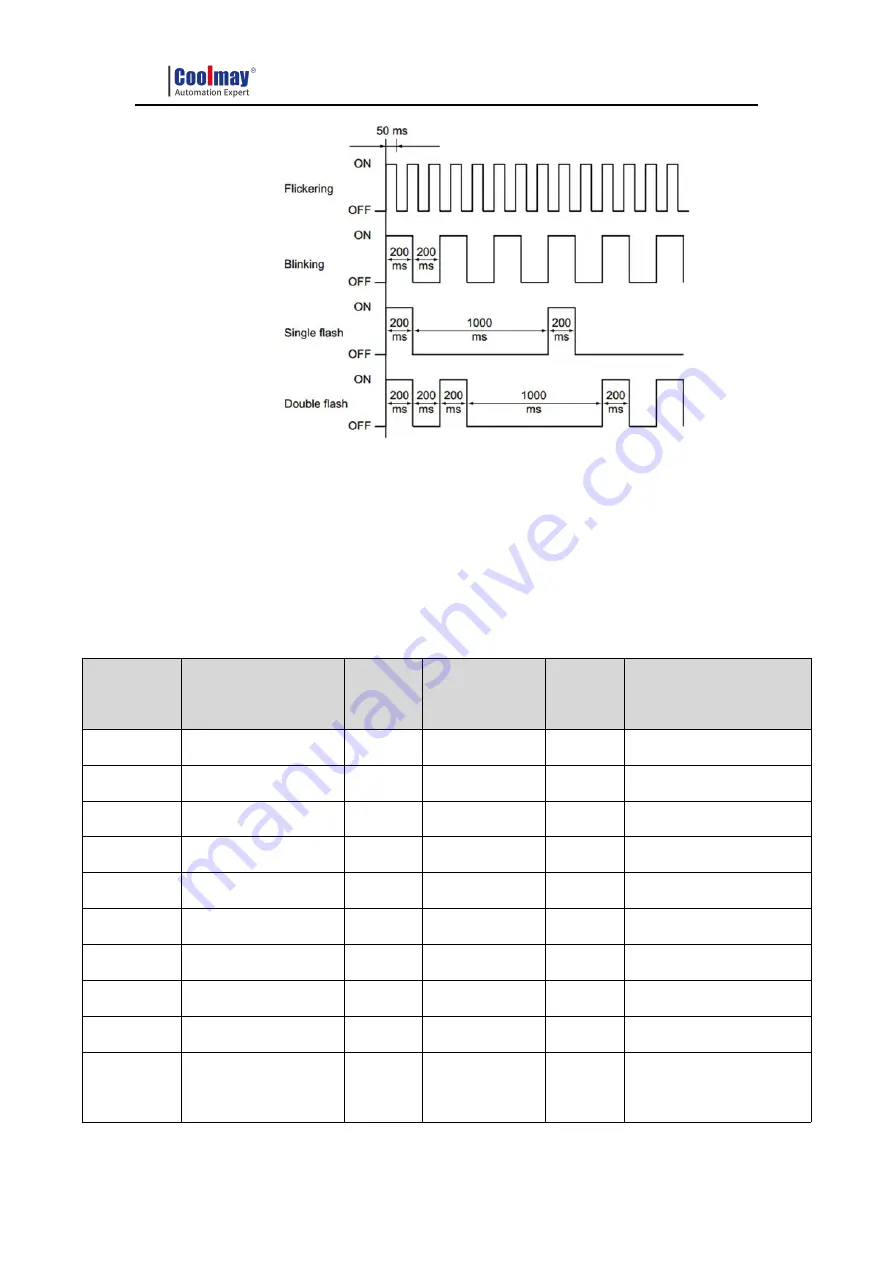
C100E EtherCAT AC Servo Drive
www.coolmay.com
19
Pic 4.7 Indicator Flashing Time
4.3.3 Communication Object
The parameters include communication parameters, factory defined
parameters and 402 group parameters.
Address
Name
Read/
Write
Default
Value
Range
Introduction
1000h
device type
R
0x00040192
1001h
wrong register
R
0
1008h
device name
DSX00E
1009h
Hardware version
V1.0
100Ah
software release
V1.0
1018h+01
Manufacturer ID
R
0x00445653
1018h+02
Product code
R
0x00000001
1018h+03
Modified coding
R
0x00000001
1018h+04
serial number
R
0x00000001
1600h
RXPDO
mapping object0
RW
It can configure the
number and content