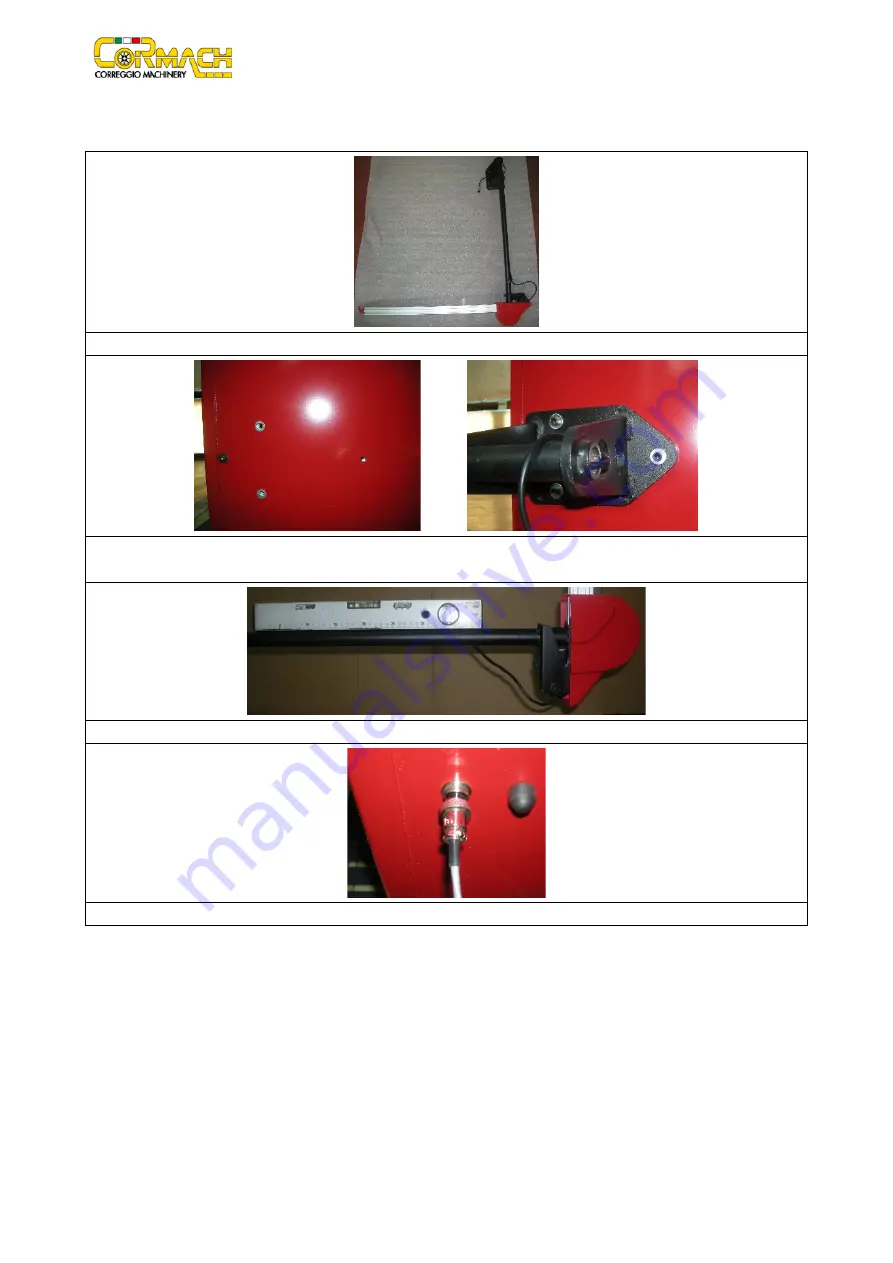
Technical Support Manual – 05/2018 Rel. 2.1.3
Page 11
Lar
Activation or deactivation of the width sensor (if present)
When present, the external sensor must be installed according to the pictures provided below.
Remove external sensor from the packaging.
There are holes at the back of the wheel balancer to attach the external sensor. Place the flange of external sensor on the three
holes.
Square the external sensor using a level. Tighten the 3 M6 screws.
Connect the cable of the external sensor to the machine and screw on the connector.
Summary of Contents for MEC 10
Page 1: ...WHEEL BALANCERS MEC 5 MEC 10 MEC 15 MEC 20 TECHNICAL SUPPORT MANUAL UK...
Page 2: ......
Page 38: ......