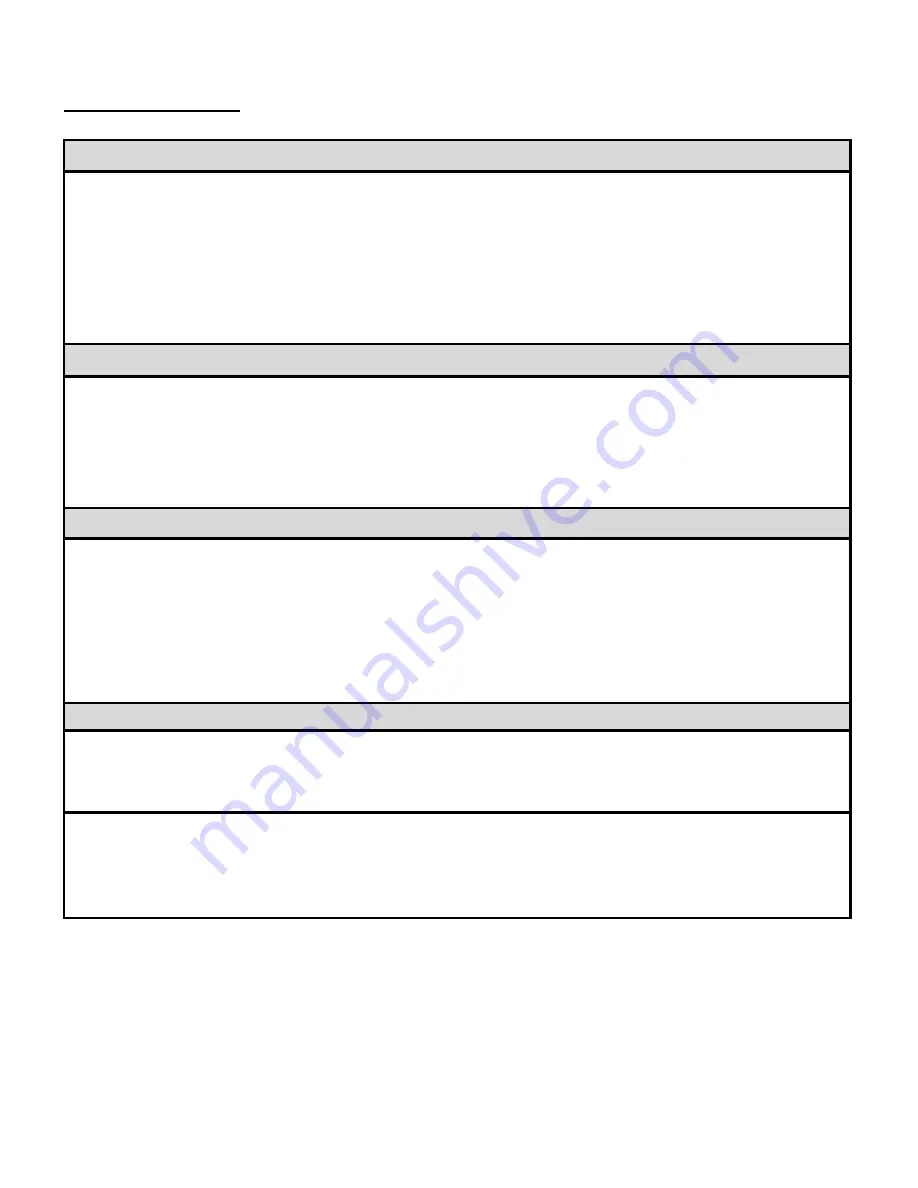
2
FS-EP Series
380V/400V/415V
REVISION # 0000
DATE: 03/22/2021
SPECIFICATIONS
MOTOR
Type:
Restricted cycle duty (30 cycles per hour)
Horsepower:
1/3 hp, 1/2 hp, 3/4 hp
Speed:
50Hz – 1400 RPM, 60Hz – 1700 RPM
Voltage:
380V/400V/415V – 3 phase
Current:
See motor nameplate
ELECTRICAL
Transformer:
24VAC
Wiring Type:
Momentary pressure open, stop, constant pressure close
(provided standard), with provision for momentary pressure close
*
Limit Adjustment:
Linear driven, fully adjustable screw type cams.
MECHANICAL
Drive Reduction:
43:1 (1/3 hp & 1/2 hp), 57:1 (3/4 hp)
Output Shaft Speed:
50Hz - 32 RPM (1/3 hp &1/2 hp), 25 RPM (3/4 hp)
60Hz - 39 RPM (1/3 hp &1/2 hp), 30 RPM (3/4 hp)
Door Speed:
6 - 8” per sec. average (typical)
Brake:
Solenoid actuated brake
ENTRAPMENT PROTECTION
Sensing Edge*:
(Optional) Sensing device attached to the bottom edge of the door.
Non-Contact Device*:
(Optional) Photo eye device.
* Per the requirements of UL Standard 325, the door operator is setup for constant
pressure to close the door. As an alternative, the door may be provided with a monitored
entrapment protection device that will reverse the door upon contact with or detection of
an obstruction during closing. Adding an entrapment device would enable momentary
close operation.
Notes:
1. Non-contact device (photo eye) can be used on doors up to 45 ft. wide (or maximum rated range of
device if less than 45 ft.). Use a sensing edge to provide entrapment protection on doors over 45 ft.
wide.
2. Sensing edge can be used on all doors.
Summary of Contents for FS-36EP Series
Page 18: ...17 FS EP Series 380V 400V 415V REVISION 0000 DATE 03 22 2021 ...
Page 19: ...FS EP Series 380V 400V 415V REVISION 0000 DATE 03 22 2021 18 ...
Page 20: ...FS EP Series 380V 400V 415V REVISION 0000 DATE 03 22 2021 19 ...
Page 21: ...FS EP Series 380V 400V 415V REVISION 0000 DATE 03 22 2021 20 ...
Page 29: ...FS EP Series 380V 400V 415V REVISION 0000 DATE 03 22 2021 28 APPENDIX 4 1 NO 2 OFF ON PK PK ...