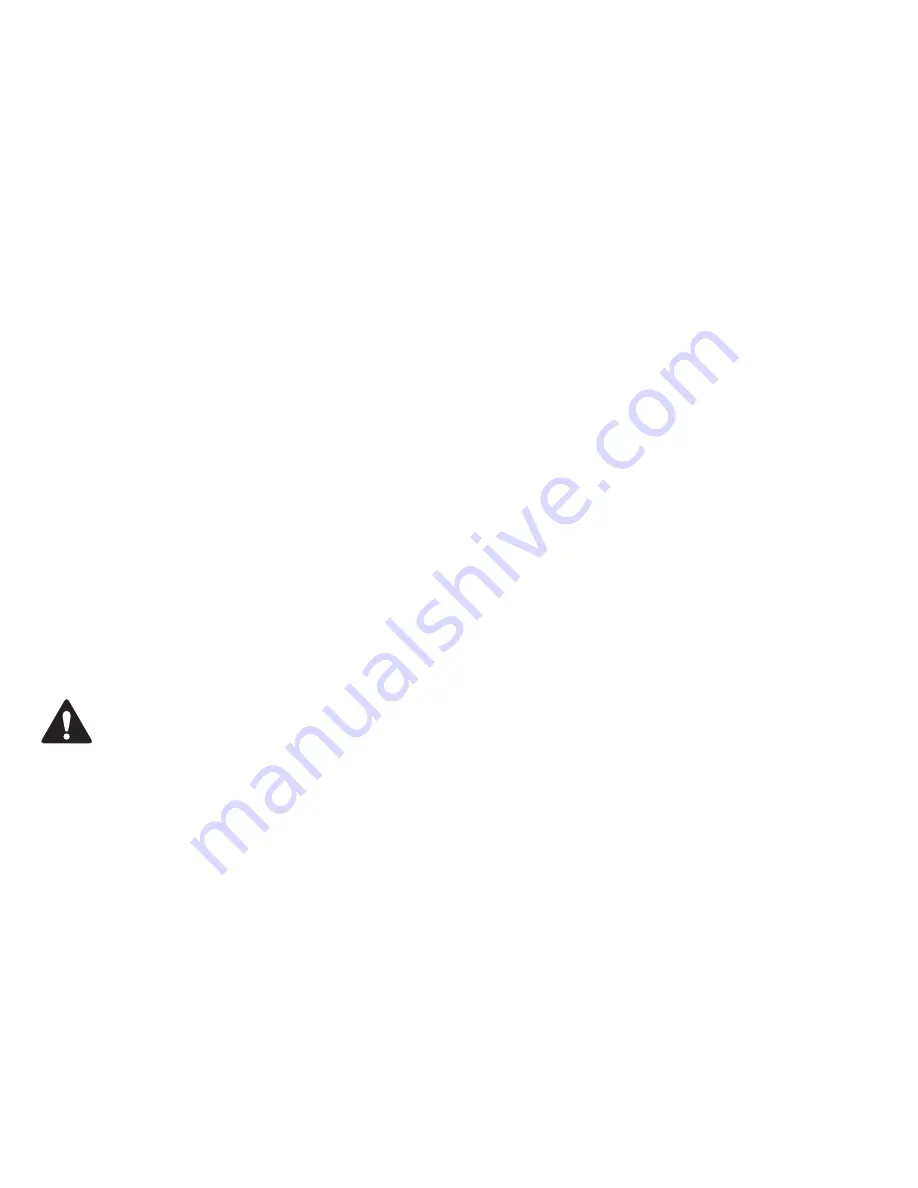
CTJTRJ22T 3
6/2/17
INSPECTION
Visual inspection should be made before each use of the jack, checking for leaking hydraulic fluid and damaged, loose or missing parts.
Each jack must be inspected by a manufacturer’s repair facility immediately, if subjected to an abnormal load or shock. Any jack which
appears to be damaged in any way, is found to be badly worn, or operates abnormally MUST BE REMOVED FROM SERVICE until necessary
repairs are made by a manufacturer’s authorized repair facility. It is recommended that an annual inspection of the jack be made by a
manufacturer’s authorized repair facility and that any defective parts, decals or warning labels be replaced with manufacturer’s specified
parts. A list of authorized repair facilities is available from the manufacturer.
SETUP
Please refer to the exploded view drawing on page 6 in this manual in order to identify parts:
1. Feed the black hose (#64) and orange hose (#63) coming out of the bottom of the handle (#60) through the handle (#52) while at the
same time lining up the hole in the handle (#52) with the hole in the handle connector (#55). Secure them together with the screw (#54).
2. Thread two nuts (#53) all the way on the bottom of the tie rod (#50). Thread the bottom of the tie rod all the way inside the slotted pin
(#49). Now tighten one nut (#53) down on top of the slotted pin (#49) and tighten. Slip the spring (#51) down on the tie rod (#50). Insert the
tie rod (#50) through the bottom of the bracket that is welded to the handle (#52) so that the spring is trapped between the bracket and
the nuts (#53) that are tightened against the slotted pin (#49). Compress the spring until the cross hole in the tie rod (#50) is visible on the
other side of the welded bracket and install the R-Pin (#71) through the hole.
3. Thread another nut (#53) all the way on the tie rod (#56). Hold the handle lock (#58) down and away from the t-handle (#60) while
simultaneously threading the tie rod (#56) nut onto the tie rod (#50).
4. Raise the handle lock (#58) up so the slotted pin (#49) does not come in contact with any of the three holes in the handle position
seat assembly (#7). Remove the screw (#73) from the handle socket (#11). Insert the handle (#52) in the handle socket (#11) while
simultaneously inserting the slotted pin (#49) in the handle socket (#11) guide holes. Make sure the hole in the lower portion of the
handle (#52) aligns with the threaded hole in the handle socket (#11) and secure them together with the screw (#73). Move the handle
up and down while simultaneously pulling the handle lock down so the slotted pin (#49) will engage with any of the three locking holes
in the handle position seat assembly (#7). Make sure the slotted pin will engage all three holes. It might be necessary to adjust the
threaded connection between tie rods (#50 and #56) in order to get proper engagement. After final adjustment, tighten the nut (#53) to
secure the connection.
5. There are two air hoses that must be firmly inserted into the couplers (#48A and #48B). The orange hose (#63) fits in the coupler (#48B)
while the black hose (#64) fits in the coupler (#48A).
6. Install the air quick disconnect of your choice in the cross valve (#65). Put at least two wraps of pipe dope tape around the disconnect
threads before installation to prevent air leaks.
7. Install the bracket assembly (#77) on the handle tube in the position as shown on the cover of the Owner’s Manual and secure the
adapters in the bracket holes using the R-Pins (#69).
8. Due to the vacuum release system design of this jack, the jack’s hydraulic system very rarely becomes air bound. Indication of an air
bound system is a ram that does not rise smoothly. In some extreme case of an air bound system, air can be purged by following this
procedure:
PURGING AIR FROM THE HYDRAULIC SYSTEM:
a. Raise the ram (#32) to maximum height and then lower it all the way down following the activation directions on top of the handle.
b. Repeat step 'a' until all the air is purged out of the system.
OPERATION
This is the safety alert symbol used for the
OPERATING INSTRUCTIONS
section of this manual to alert you to potential personal
injury hazards. Obey all instructions to avoid possible injury or death.
IMPORTANT:
Before attempting to raise any vehicle, check
vehicle service manual for recommended lifting surfaces.
1. Become familiar with the identification and function of the operating jack components.
a. The ram (#32) is the shaft that comes out of the jack when you rotate the air lever to the right.
b. The ram (#32) is equipped with an extension screw which can be unscrewed to extend from the ram if there is not enough hydraulic
stroke to raise the load to the desired height. If additional height is required, extension adapters can be inserted in the hole on top of
the extension screw.
c. Larger diameter saddles can be inserted in the extension screw when requiring a larger diameter saddle surface.
2. Chock the vehicle's tires that will not be lifted off the ground prior to lifting the vehicle and if available, apply the emergency brake or any
other method of braking.
3. Position the jack at the designated lift point. Estimate the required ram travel to raise the vehicle to the desired height. If the desired
vehicle height exceeds the entire ram travel, unscrew the extension screw to make up the difference and add an extension adapter if
necessary.
4. Lock the handle in a position that will not interfere with the vehicle when raised or lowered. Keep the handle in that locked position until
the work is completed and you are ready to remove the jack from use.
5. With the jack in the lowered position, push the jack under the vehicle.
IMPORTANT: Use the vehicle manufacturer's recommended lifting procedures and lifting points before lifting loads.
6. In most cases 100 psig input air pressure (do not exceed 200 psig) will lift the maximum capacity load not to exceed 22-tons. Rotate
the air lever to the right until the top of the ram comes close to the designated lift point. Make sure the designated lift point is flat,
parallel to the ground and free from grease, any kind of lubricant, and debris. Proceed with pumping the jack in order to lift the vehicle
to the desired height. During lifting, inspect the position of the jack in relation to the ground and the ram in relationship to the load
to prevent any unstable conditions from developing. If conditions look like they are becoming unstable, slowly lower the load and make
appropriate setup corrections after the load is fully lowered.
7. When the vehicle or load is lifted to its desired height, immediately place safety support stands (jack stands) in their designated locations
and adjust the stands' support columns up as close to the designated vehicle support points as possible. Although jack stands are
individually rated, they are to be used in a matched pair to support one end of the vehicle only. Stands are not to be used to