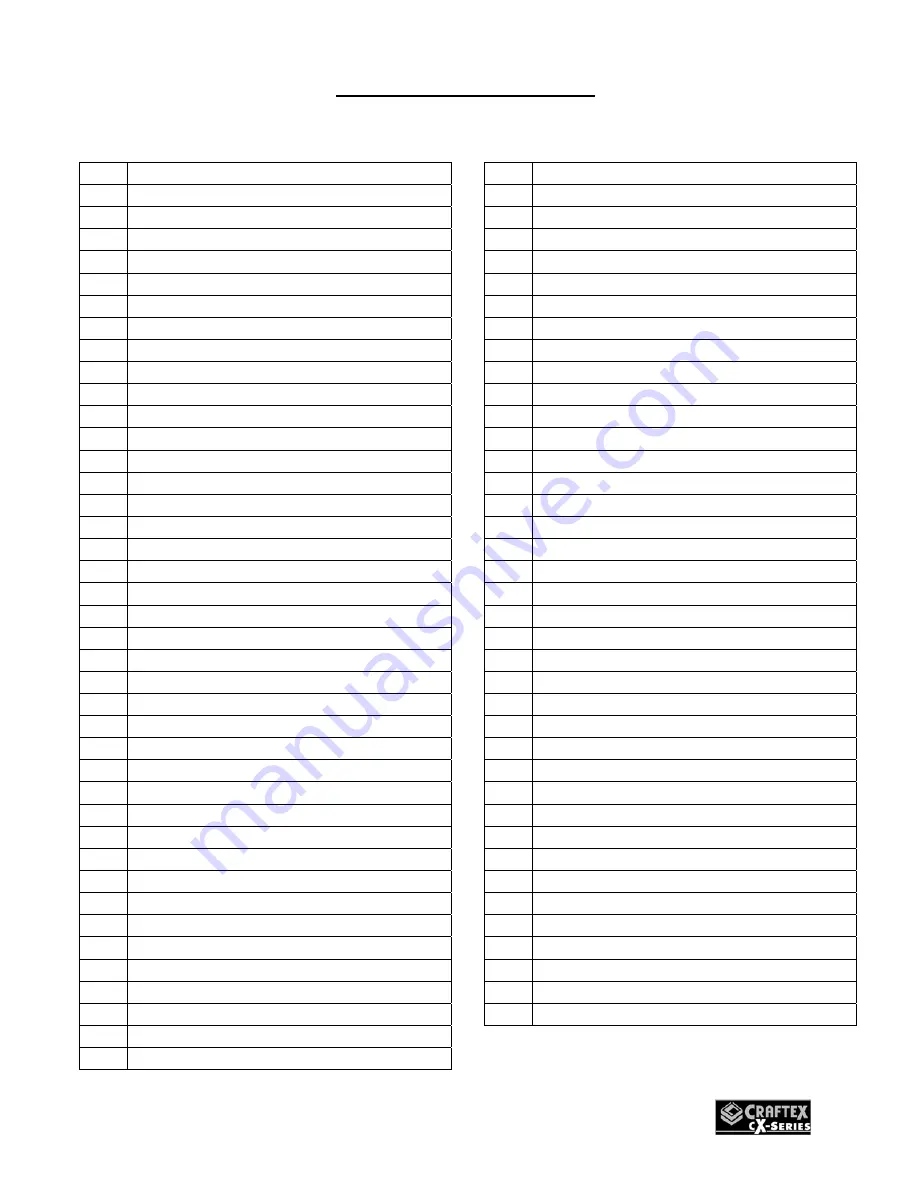
27
1 BODY
2
QUICK HANDLE BAR
3 T
TYPE
WASHER
4 UPPER
WHEEL
BRACKET
5 SCREW
6A
UPPER WHEEL SHAFT 17MM
7 BEARING
7A BEARING
8A
UPPER WHEEL - Cast Iron
9 WHEEL
PROTECTOR(TIRE)
10 C-RING
10A C-RING
11 RETAINER
NUT
12 BLADE
133"
13 HINGE
PIN
14 UPPER
GUARD
15 LOWER
GUARD
16
CAP SCREW 1/4"*3/8"
17 LOCK
WASHER
1/4"
18
HEX NUT 3/4"(L.H.)
19A LOWER WHEEL -CAST IRON
21A LOWER
WHEEL
SHAFT
22 LOCKNUT
3/8"
23A BEARING
23B BEARING
24 KEY
5MM
25 NUT
26A SPRING
WASHER
27 CORD
30A NUT 5/8
31 NUT
32 POINTER
33 SPRING
34 STRAIN
RELIEF
35
HEX NUT 5/16"
36 KNOB
5/16*2"
37 POWER
CORD
38
GUARD LOCKING KNOB
39 SCREW
40 CORD
41 PIN
42
HEX NUT 3/8"
43 SCREW
44 BEARING
COVER
45 NUT
46 SCREW
47 ADJUSTING
SCREW
48A
BEARING BASE
49 NUT
50 V-BELT
A41
51
SET SCREW 1/4"*1/4"
52A
WHEEL PULLEY
53 IDLER
PULLEY
54 MOTOR
PULLEY
55 V-BELT
A30
56 C-RING
57 SHAFT
58 WASHER
59 MOTOR
60 FLAT
WASHER
3/8"
62
HEX BOLT 3/8"*1 1/4"
63 SWITCH
COVER
63 TENSION
LABLE
64 SCREWM4*6
65
PHILLIPS HEAD SCREW M3*18
66 SCREW
67 SCREW
68
PHILLIPS HEAD SCREW 3/16"*1/2"
69
CONTROLLER COVER PLATE
70
HEX NUT 3/16"
71
MOTOR INVERTER SWITCH
72 SPEED
DIAL
73 SWITCH
W/LARGE
STOP
74
INVERTER RHYMEBUS RMG-5 1HP
75
HEX BOLT 5/16"*3/4"
76
HEX NUT 5/16"
77 BRUSH
BASE
78 SCREW
79 BRUSH
80
HEX BOLT 1/4"*3/4"
CX101 BODY PARTS LIST
REF# DESCRIPTION
REF# DESCRIPTION