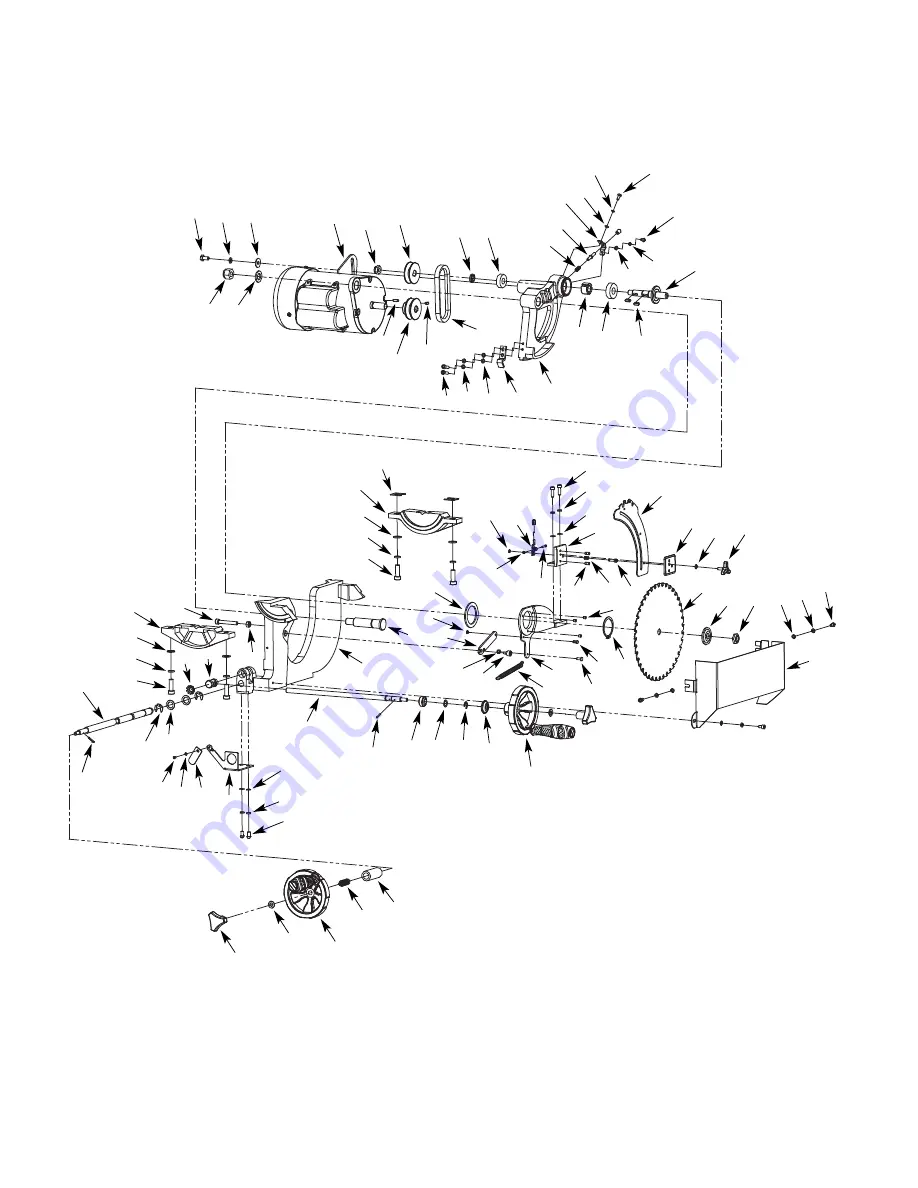
32
6
59
15
16
17
58
34
36
37
38
7
8
9
10
11
12
13
20 21
22
36
28
25
26
24
24
26
25
32
33
47
40
74
70
71
72
73
41
65
75
76
77
78
79
79
81
82 83
84 85
87
88
16
17
56
53 46 45 44
30
43
31
29
27
30
86
80
50
51
49
16
52
17 54
55
17
42
66
67
68
69
38
39
60
62
61
37
35
23
2
1
3
19
18
17
16
14
15
48
4
5
Model 351.218330
64
63
Figure 59 - Replacement Parts Illustration for Blade Drive