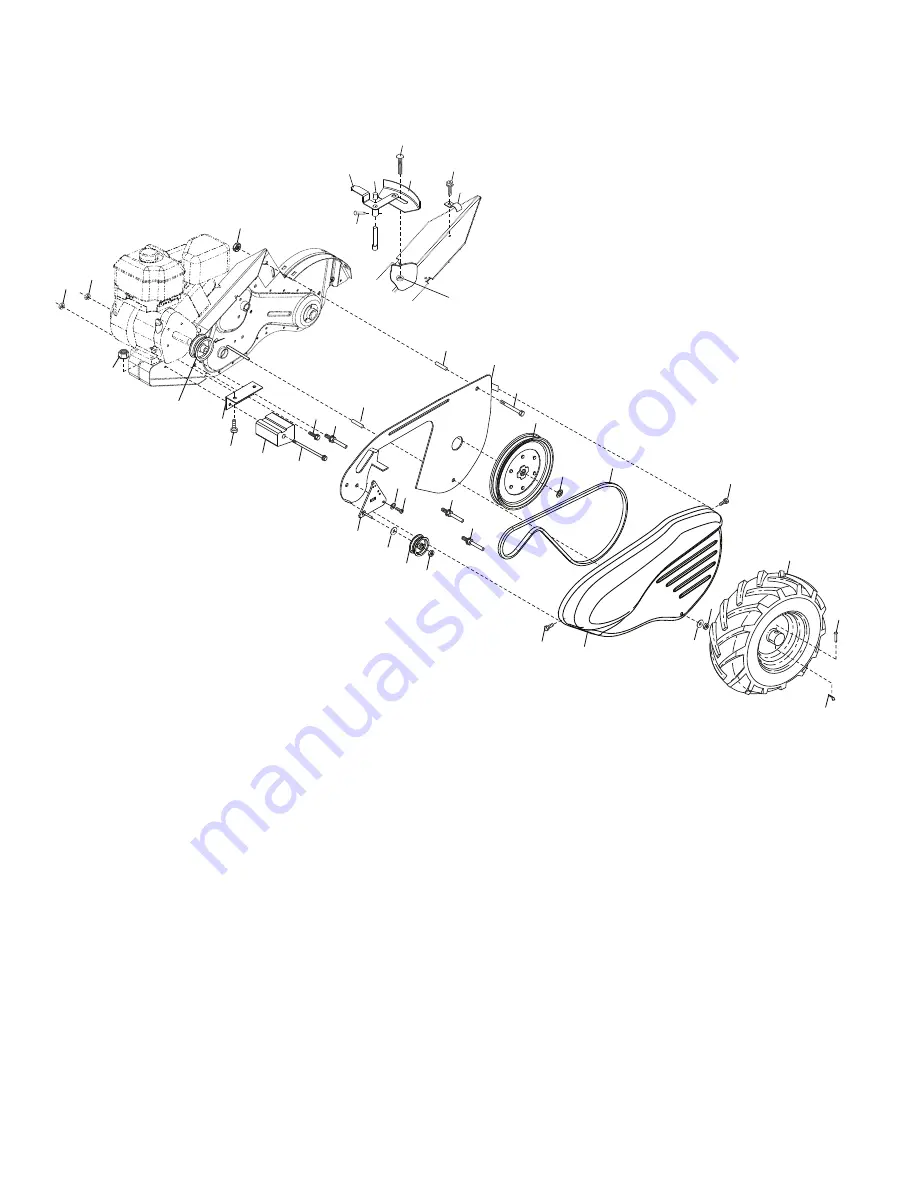
22
REPAIR PARTS
TILLER - - MODEL NUMBER 944.629673
MAINFRAME, LEFT SIDE
68
65
68
65
67
34
31
30
28
3
40
26
15
66
44
40
27
19
16
38
4
21
14
32
69
69
33
36
13
37
39
6
5
8
12
7
9
10
29
22
mainframe_left_25
24
23
25
KEY PART
NO. NO.
DESCRIPTION
27 132801 Belt,
V
28 104679X Pulley,
Idler
29 12000032 Ring,
Klip
30 159229 Bracket,
Idler
31
102384X
Bolt, Hex 5/16-16 x 12
32
102141X
Shaft, Idler Arm
33
STD523710 Bolt, Hex 3/8-16 x 1
34
102383X
Counterweight, L. H.
36
102331X
Bracket, Reinforcement, L. H.
37 130812 Sheave,
Engine
38
74760544
Bolt Hex 5/16-18 x 2-3/4
39 140062 Cap,
Plunger
40
170488
Screw Hex Wsh Slt #10-24 x .50
44
73800500
Nut, Lock Hex 5/16-18
65
73970500
Nut, Hex Flange
66
19131312
Washer 13/32 x 13/16 x 12 Ga.
67
74760524
Bolt Hex 5/16-18 x 18 x 1-3/4
68
STD541437 Nut, Keps 3/8-16 unc
69
164173
Keeper Belt Engine
NOTE:
All component dimensions given in U.S. inches.
1 inch = 25.4 mm
KEY PART
NO. NO.
DESCRIPTION
3
73930600
Nut Centerlock 3/8-16 unc
4
432420
Shield Inner Belt Guard
5
164329
Pin, Shift Lever
6
162756
Lever, Shift
7
STD532505 Bolt, Carriage 1/4-20 x 1/2 Gr. 5
8
161530
Plate, Shift Indicator
9
86777
Screw, Hex, Washer Head, Slotted
#10-24 x 1/2
10 9484R
Clip
12
73510400
Nut, Keps 1/4-20
13
23230506
Screw, Set, Hex 5/16-18 x 3/8
14
156117
Spacer, Split 0.327 x 0.42 x 1.220
15
STD551031 Washer 11/32 x 11/16 x 16 Ga.
16 145102 Sheave,
Transmission
19 12000028 Ring,
Retainer
21
110652X
Spacer, Split 0.327 x 0.42 x 2.09
22
74770508
Bolt Hex 5/16-2-1/2
23 102190X Tire
183122X613
Rim
795R Tire
Valve
24 126875X Rivet,
Drilled
25 STD624003
Clip,
Hairpin
26 165501X428
Guard,
Belt
Summary of Contents for 944.629673
Page 32: ...32 SERVICE NOTES ...
Page 33: ...33 SERVICE NOTES ...
Page 34: ...34 SERVICE NOTES ...
Page 36: ...ª ª ªªªª ª ª ª ª ª ª ª ª ª ª ª ª ª ª ª PRINTED IN U S A 02 02 12 TH ...