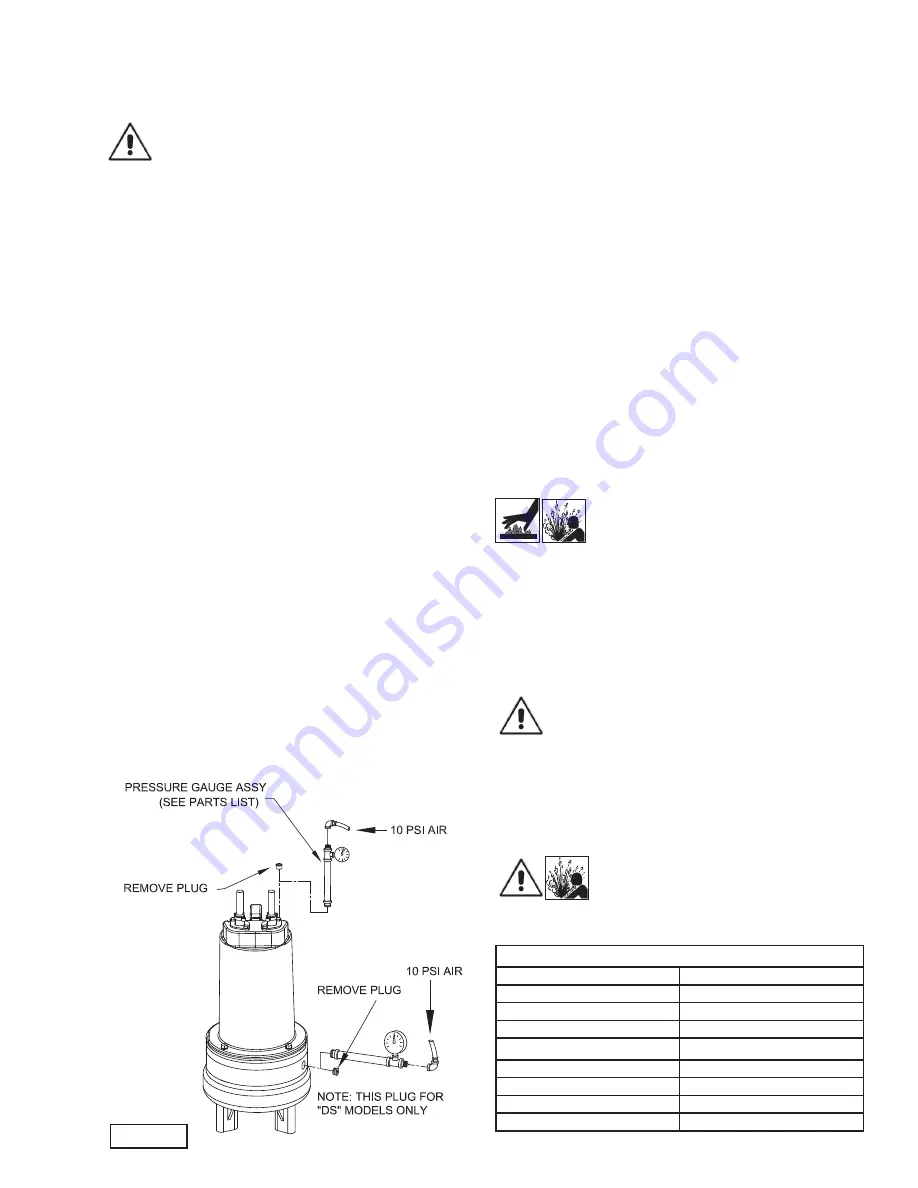
11
SECTION F: SERVICE AND REPAIR
NOTE:
All item numbers in ( ) refer to Figures 16 thru 21.
CAUTION ! - Operating pump builds up heat and
pressure; allow time for pump to cool to room
temperature before handling or servicing. Slowly
remove pipe plug prior to servicing as housing
may be pressurized.
F-1) Lubrication:
Anytime the pump is removed from operation, the cooling oil in
the motor housing (6) should be checked visually for oil level
and contamination.
F-1.1) Checking Oil:
Motor Housing -
To check oil, set unit upright. Remove pipe
plug (39) from housing (6). With a flashlight, visually inspect
the oil in the motor housing (6) to make sure it is clean and
clear, light amber in color and free from suspended particles.
Milky white oil indicates the presence of water. Oil level should
be just above the motor when pump is in vertical position.
F-1.2) Testing Oil:
1.) Place pump on it’s side, remove pipe plug (39), from motor
housing (6) and drain oil into a clean, dry container.
2.) Check oil for contamination using an oil tester with a
range to 30 Kilovolts breakdown.
3.) If oil is found to be clean and uncontaminated (measuring
above 15 KV. breakdown), refill the motor housing as per
section F-1.4.
4.) If oil is found to be dirty or contaminated (or measures
below 15 KV. breakdown), the pump must be carefully
inspected for leaks at the shaft seal (28), cable assemblies
(16) and (56 if used), square ring (27) and pipe plug (39),
before refilling with oil. To locate the leak, perform a
pressure test as per section F-1.3. After leak is
repaired, dispose of old oil properly, and refill with new oil
as per section F-1.4.
F-1.3) Pressure Test:
Pumps that have had the oil drained from the Motor
Housing -
Apply pipe sealant to pressure gauge assembly
and tighten into pipe plug hole (See Figure 4). Pressurize
motor housing to 10 P.S.I. Use soap solution around the
sealed areas and inspect joints for “air bubbles”. If, after
five minutes, the pressure is still holding constant, and no
“bubbles” are observed, slowly bleed the pressure and
remove the gauge assembly. Replace oil as described in
section F-1.4. If the pressure does not hold, then the leak
must be located and repaired.
Pumps that have NOT had
the oil drained from the Motor Housing -
The pressure
test may be done with the oil at its normal level. Remove
pipe plug (39) from motor housing (6). Apply pipe sealant to
pressure gauge assembly and tighten into hole (see Figure
4). Pressurize motor housing to 10 P.S.I. Use soap solution
around the sealed areas above the oil level and inspect joints
for “air bubbles”. For sealed areas below the oil level, leaks
will seep oil.
If, after five minutes, the pressure is still holding constant,
and no “bubbles”/oil seepage is observed, slowly bleed the
pressure and remove the gauge assembly. If the pressure
does not hold, then the leak must be located and repaired.
Seal Chamber (DS Units Only)-
Set unit on its side with
fill plug (44) downward, remove plug (44) and drain all oil
from seal chamber. Apply pipe sealant to pressure gauge
assembly and tighten into hole in outer seal plate (29).
Pressurize seal chamber to 10 P.S.I. and check for leaks as
outlined above.
CAUTION ! - Pressure builds up extremely
fast, increase pressure by “TAPPING” air
nozzle. Too much pressure will damage
seal. DO NOT exceed 10 P.S.I.
F-1.4) Replacing Oil:
Motor Housing-
Set unit upright and refill with new cooling
oil as per Table 1 (see parts list for amount). Fill to just above
motor as an air space must remain in the top of the motor
housing to compensate for oil expansion (see Fig 16, 18 or
20). Apply pipe thread compound to threads of pipe plug (39)
then assemble to motor housing (6).
IMPORTANT! - For single phase units, oil level
should be below capacitor.
Seal Chamber (DS Units Only)-
Set unit on its side, with
plug (44) upward, and refill with new oil as per Table 1 (see
parts list for amount). Apply pipe thread compound to threads
of pipe plug (44) and assemble to outer seal plate (29).
WARNING ! - DO NOT overfill oil.
Overfilling of motor housing with oil
can create excessive and dangerous
hydraulic pressure which can destroy the
pump and create a hazard. Overfilling oil
voids warranty.
TABLE 1 - COOLING OIL - Dielectric
SUPPLIER
GRADE
BP
Enerpar SE100
Conoco
Pale Paraffin 22
Mobile
D.T.E. Oil Light
G & G Oil
Circulating 22
Imperial Oil
Voltesso-35
Shell Canada
Transformer-10
Texaco
Diala-Oil-AX
Woco
Premium 100
FIGURE 4
Summary of Contents for 104872
Page 16: ...16 FIGURE 13 ...
Page 17: ...17 FIGURE 13 ...
Page 18: ...18 FIGURE 13 CONTIUED ...
Page 20: ...20 FIGURE 16 SE L 3SE L Series Single Seal ...
Page 21: ...21 FIGURE 17 SE L 3SE L Series Single Seal ...
Page 22: ...22 FIGURE 18 SE HT High Temp Series Single Seal ...
Page 23: ...23 FIGURE 19 SE HT High Temp Series Single Seal ...
Page 24: ...24 FIGURE 20 3SE DS Series Double Seal ...
Page 25: ...25 FIGURE 21 3SE DS Series Double Seal ...
Page 29: ...29 Notes ...
Page 30: ...30 Notes ...