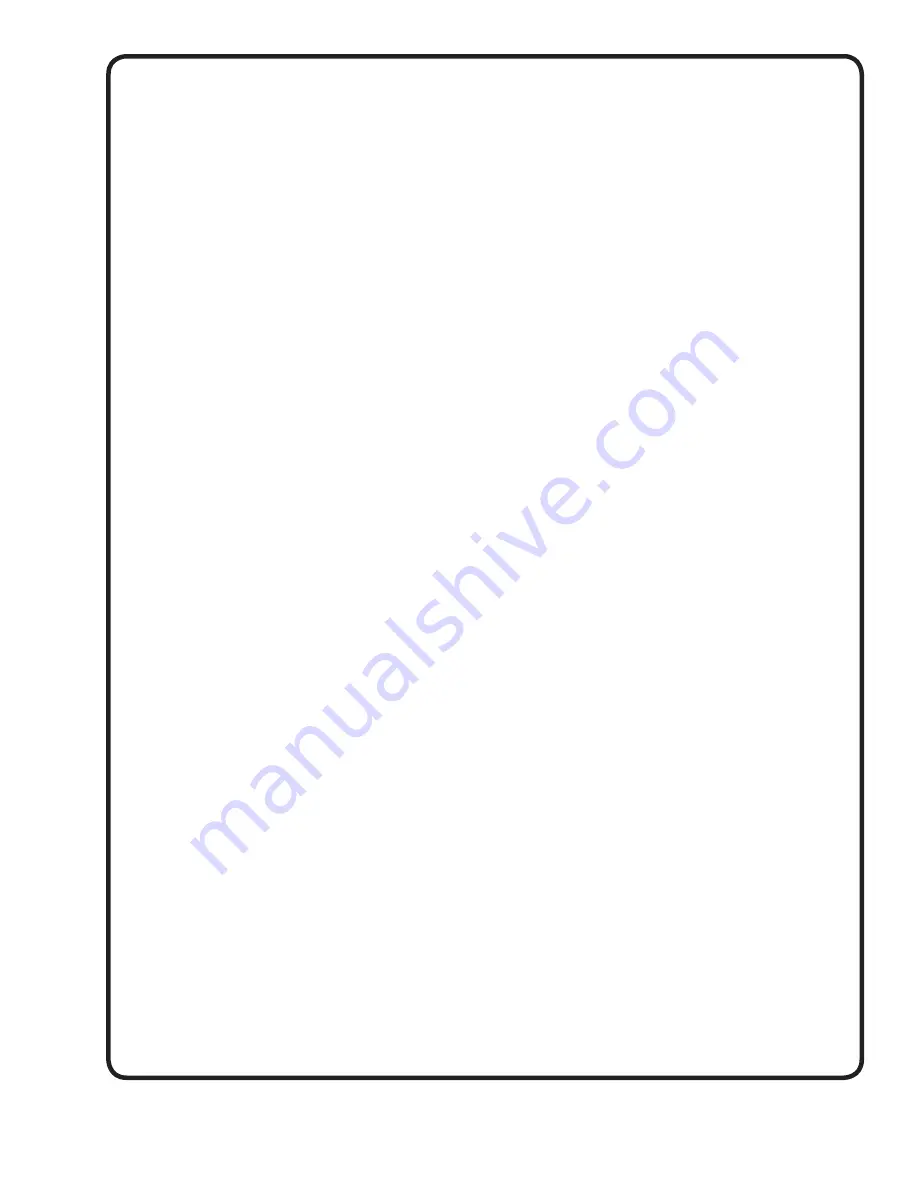
5
5. DOWELLING
After the unit has been running about one week the
coupling halves should be given a
fi
nal check for
misalignment, caused by pipe strains or temperature
strains, If the alignment is correct, both pump feet and
driver should be dowelled to the baseplate.
6. PIPING
The pump suction and discharge connections are not
intended to indicate the required suction and discharge
pipe sizes. The pipe diameter must be selected according
to the requirements of the pumping system and
recommended friction losses for the liquid being pumped.
Usually, it is advisable to increase the size of both the
suction and discharge pipes at the pump nozzles to have
minimum acceptable friction loss, suction pipe should
never be smaller in diameter than the pump suction
nozzle. When suction pipe is of larger diameter than the
pump suction nozzle, an eccentric reducer is required
to eliminate possible air or vapor pockets at the pump
suction inlet.
Both suction and discharge pipes must be supported
independently near the pump, so that when piping is
connected to the pump, no strain will be transmitted to the
pump. Piping should be arranged with as few bends as
possible, and, preferably, with long radius elbow whenever
possible.
SUCTION PIPING
A horizontal suction line must have a gradual rise to the
pump. Any high point in the suction pipe can become
fi
lled
with air and prevent proper operation of the pump and
may cause loss of prime. The pipe and
fi
ttings must be
free of all air leaks.
Any valves or
fi
llings should located at a distance equal
to 5 to 10 times the diameter of the suction pipe from the
pump suction nozzle. If an elbow must be installed at the
pump suction, it should be installed in a vertical position
to reduce unequal
fl
ow into the pump, which may cause
cavitation in the pump.
NOTE:
A gate valve in the suction
piping should not be used as a throttling device, as this
may cause the liquid to overheat during operation.
7. WIRING
For electric motor drives, connect power supply to
conform with national and local codes. Line voltage and
wire capacity must match the ratings stamped on the
motor nameplate.
8. ROTATION
Before starting the pump, check the required direction
of rotation of the pump. The proper direction is indicated
by a direction arrow on the pump casing. Separate the
coupling halves, then start motor to see that it rotates in
the direction required by the pump. If it does not, reverse
any two main leads of the 3-phase wiring to the motor.
The coupling halves can be reconnected and the pump
primed for starting.
C - OPERATION
1. PRIMING
CAUTION:
Before starting the pump, the casing and
suction line must be
fi
lled with liquid, and air-vented
through the vent pipe plugs. The pump must not be run
until it is completely
fi
lled with liquid, because of danger
of injuring some of the parts of the pump which depend
upon liquid for lubrication. The discharge gate vale should
be closed during priming. Be sure the stuf
fi
ng box packing
or mechanical seal and power frame are supplied with the
proper lubrication. See LUBRICATION.
2. STARTING THE PUMP
On initial start up, the gate valve in the discharge piping
should be closed and slowly opened after pump is up
to speed and pressure developed.
DO NOT
operate
pump for any appreciable length of time against a
closed discharge valve, as this may heat trapped liquid
excessively and damage the pump, packing or seal.
The following important items should be checked as pump
is started and placed in operation.
a. Pump and driver securely bolted.
b. Coupling properly aligned.
c. Piping complete.
d. Correct pump rotation.
e. Pump shaft turns freely.
f. Discharge valve closed.
g. Suction valve open (if used).
h. Seal water valve open (if used).
i. Pump fully primed.
j. Pump and driver properly lubricated.
k. Liquid drips slowly from packing gland.
Only after these items have been checked should the
pump be started.
3. PUMP ADJUSTMENT
Open discharge valve as soon as operating speed has
been reached. After the pump has been started, the
packing box gland should be tightened to eliminate
excessive liquid loss. (Applies only to pumps using
packed stuf
fi
ng boxes). Packing should not be pressed
too tight, as this may result in burning the packing and
scoring the shaft sleeve. The best adjustment will allow
the liquid to drip slowly from the packing box gland. This
will permit proper lubrication of the packing and dissipate
generated heat.
As soon as the pump and driver have reached the normal
operating temperature, the unit should be shut down for
fi
nal coupling alignment. This should be done by following
the instructions found in Section B, Part 3. If correction
is necessary, it may be accomplished by the addition or
removal of shims from under the motor mounting feet.
Summary of Contents for Weinman B Series
Page 16: ...Notes ...