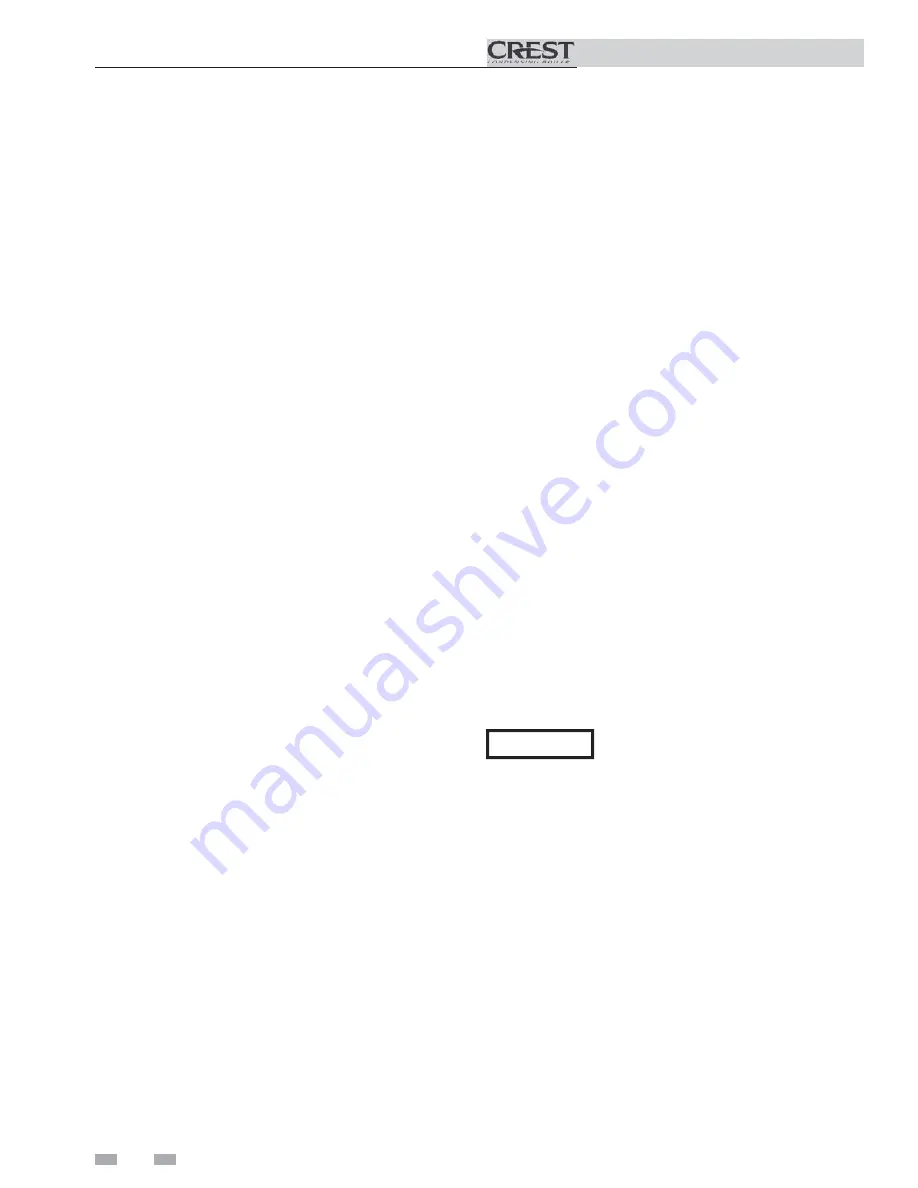
48
Installation & Operation Manual
10
Operating information
Monitor external limits
Connections are provided on the connection board for
external limits such as an additional high limit. The
SMART TOUCH control will shut off the burner and
inhibit relighting whenever any of these external limits
open.
Run-time and alarm outputs
The boiler provides dry contacts for indicating when the
boiler is running, and when it is unable to operate.
Run-time and cycle counting
The control uses four timers to monitor the total hours of
burner operation:
75 - 100%
50 - 75%
25 - 50%
<25%
The control uses four (4) ignition counters to monitor
the amount of boiler cycles. The first counter counts all
ignitions of the control. The second counter counts only
ignition attempts that have failed. The third and fourth
counters are the same as the first and second respectively,
but can be reset by the installer.
Service reminder
The control can be programmed for service reminder
notification. This notification will become active when
either a set amount of time has expired, or a set amount of
running hours or cycles has expired (all adjustable by the
installer). The service reminder notification can be reset
by the installer. The service company’s name and phone
number can be programmed to display when service is due.
Error logging
The control will hold in memory the last 10 blocking faults
as well as the last 10 lockout faults. The date and time of
the occurrence will be recorded as well. Only the 10 most
recent occurrences will be held in memory.
Boiler temperature regulation
Operating temperature (target)
The SMART TOUCH control module senses water
temperature and regulates boiler firing and firing rate to
achieve a target temperature. The target temperature can
be set between 32°F (0°C) and 185°F (85°C).
• Target temperature is fixed when the outdoor
sensor is not installed.
• Target temperature is calculated as described
under “Outdoor Reset Operation” and “Target
Temperature Boost” when the outdoor sensor is
connected.
High limit operations
The Crest SMART TOUCH control has two (2) integral limits,
one auto reset and one manual reset. The Crest also has one
auxiliary manual reset high limit. The integral and auxiliary
high limits are UL353 certified.
When the outlet temperature exceeds 195°F (90.6°C) (Installer
Adjustable Parameter), integral auto reset high limit action
occurs. The boiler will shut down until the outlet water cools
down and the timer expires.
If the outlet temperature exceeds 200°F (93.3°C) (User
Adjustable Dial), auxiliary manual reset high limit action
occurs. The boiler will shut down until the outlet water cools
down and the boiler is reset through the user interface.
If the outlet temperature exceeds 205°F (93.3°C) (Installer
Adjustable Parameter), integral manual reset high limit action
occurs. The boiler will shut down until the outlet water cools
down and the boiler is reset through the user interface.
Low water cutoff protection
A low water cutoff device with test and reset functionality is
provided in the boiler as standard equipment.
Flow sensing device
The SMART TOUCH control module uses temperature sensing
of both supply and return temperatures of the heat exchanger.
If the flow rate is too low or the outlet temperatures too high,
the control module modulates down and will shut the boiler
off. This ensures boiler shutdown in the event of low flow
conditions.
Outdoor reset operation, if used
Target temperature with outdoor reset
This feature improves the system’s efficiency as the outdoor
temperature warms up.
See the Crest Service Manual to change the settings.
Reset curve
The reset curve looks at outdoor air temperature and adjusts
the set point.
NOTICE
If a mechanical flow switch is required to
meet local code requirements the Crest
boiler can be equipped with a field supplied
outlet switch. Please reference page 38 of
this manual for more information.